When you’re building an over-the-top race car, like we are with Project BlownZ, you have to beef up areas that are often overlooked on your average 500 horsepower street car. One incredibly important area, especially when it comes to racing (which we intend to do with BlownZ), is reinforcing or replacing the driveshaft. GM never intended for the 2002 Camaro Z28 driven off of the dealership lot to get a 1,300 horsepower, supercharged 388 cubic-inch engine like the one for BlownZ. That motor would shatter the stock driveshaft the first time we put our foot into the throttle.

With 388 cubic inches of ProCharged LSX trying to twist the chassis every time we mash the gas, BlownZ's drivshaft had better be up to the challenge.
That’s why we contacted professional driveshaft builders Dynotech, who have over 80 years of experience in the business of balancing, and for the past 25 years have built aftermarket driveshafts for everything from stock cars to multimillion dollar yachts. Who better to build a driveshaft for Project BlownZ? So we called up Steve Raymond, the General Manager of Dynotech, who walked us through the different driveshafts they custom build, and how this integral piece of racing equipment is manufactured.
A History Of Performance
“The company started as a division of Balance Engineering,” says Raymond. “It evolved over the course of time to become a balancing company, and we evolved out of that balancing company to become a stand-alone driveshaft maker.” Dynotech’s meteoric rise to prominence has come with their wide-ranging use in many high horsepower-intensive motorsports. “We do everything from one-off, street rod applications to professional race teams. We’re doing 75-80% of NASCAR, pro-off road teams, boat racing, lots of drag cars, lots of door slammer drag cars, and the resto-mod market is becoming really good for us too.”
Dynotech’s prevalence among professional racers has made their driveshafts very popular with the amateur racing crowd too. And while we would never lump ourselves in with the professional racers and teams who do racing for a living every day, we aren’t building a 1,300 horsepower Camaro to go to the track and lose. That said, for a hollow tube whose sole function is to connect the transmission with the rear end, there are a surprising number of options and advantages to different types of driveshafts.
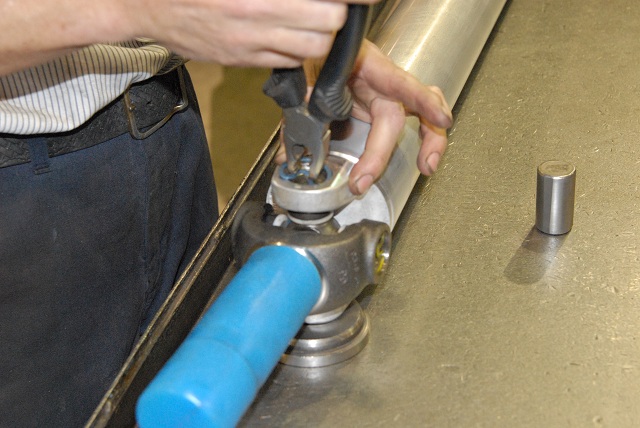
Most of the driveshafts Dynotech makes are of the aluminum variety, offering lightweight strength at an affordable price.
Aluminum, Chromoly, or Carbon Fiber?
The chromoly shaft is for serious racing applications, with increased torsional strength designed to resist well over 2,000 horsepower.
However, that won’t quite cut it for Project BlownZ. Our supercharged 388 should make around 1,300 horsepower, beyond the comfortable threshold for an aluminum driveshaft. That leaves just two more options; a chromoly driveshaft, or a carbon fiber-wrapped aluminum shaft. The carbon fiber-wrapped aluminum driveshaft is exactly what it sounds like; an aluminum driveshaft wrapped with a carbon fiber-composite weave, adding extra strength and enabling it to handle up to 1,500 horsepower and between 1,000 and 1,200 ft-lbs of torque. These driveshafts strike a great sweet spot between strength and low weight.
The chromoly shaft is for serious racing applications, with increased torsional strength designed to resist well over 2,000 horsepower. Unfortunately, there are a few trade offs that come with that much strength. The chromoly steel, while super strong, is significantly heavier than an aluminum unit of the same size. Ultimately though, we opted to go with the chromoly driveshaft for Project BlownZ to give us a wide safety margin and plenty of room to grow.
How To Build A Better Driveshaft
Save for the carbon fiber wrap, all of Dynotech’s driveshafts are built the same. “The manufacturing process and tolerances have increased over time, though the basic design of the driveshaft hasn’t changed much.” says Raymond. If you’re looking for a custom application, you’ll obviously need to start with the dimensions (length and diameter) and vehicle specifications the driveshafts will have to hold up to. Raymond tells us, “Application really matters; is this a drag car, an autocrosser, or just a show car with a big engine?”
Driveshaft construction starts with raw materials before being cut, welded, straightened, and balanced.
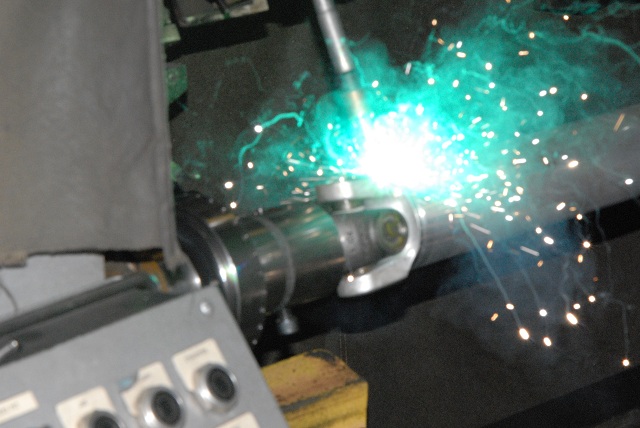
Dynotech fabricates each of their driveshafts to have less than 0.010" runout, and guarantees them to be within 0.0625" of the length you specify.
Once Dynotech has the dimensions, building the shaft starts with raw stock of hollow aluminum or chromoly tubes. The tube is then cut to length a rough length, and then put into a special lathe that will shave it to the excellent length. “All of our driveshafts are built to within 1/16th of an inch in their center-to-center dimensions,” says Raymond. Placing the driveshaft in the lathe also allows Dynotech engineers to ensure that the shaft is straight and true.
Once the u-joints and yoke are installed, then it is off to the high-speed balancer, a critical component in the production of any driveshaft. “It’s a time-consuming operation for us,” explains Raymond. “We completely clean the shaft, we measure it for straightness again, we go through a straightening operation on the balancer, and then we calibrate that driveshaft against the tooling in the balancer.” To balance a driveshaft requires adding small weights, and Dynotech hand-TIG welds all of their weights to ensure that they are never, ever coming off.
BlownZ Gets the “Shaft”…Literally
From start to finish, a single driveshaft takes the guys at Dynotech about 40 minutes to produce from raw stock to finished product ready for shipping. It didn’t seem to take much longer than that for us to get our custom chromoly driveshaft in our eagerly waiting hands. It was one of the last parts we needed before we could get the car on the dyno and start tuning, so we didn’t waste any time getting it installed and the driveline angles dialed in.
One of the most vital aspects of installing a driveshaft is making sure you have the proper driveline angles. Raymond tells us, 'Universal joints are incredibly tough, but nothing will wear them out quicker than forcing them to operate with too much angle on them.'
Hopefully we’ve been able to shed some light on the process of choosing a driveshaft, and how they come together. We feel secure knowing that the Dynotech driveshaft in Project BlownZ is more than up to the challenge of the 1,300+ horsepower we’ll be throwing at it this summer.