When it comes to building a hot rod, there is nothing more important than the foundation. If you start with a good chassis, you’re project is on the right track. It doesn’t matter how much money you put into the drivetrain, paint, upholstery, or whatever, if you’re sitting on an 80-year-old rusted frame, a solid foundation is not part of your equation. It’s crucial to start on the right foot, and where better to start than in Fife, Washington, at Art Morrison Enterprises.
What comes in as raw steel leaves the Art Morrison shipping area as a complete, beautiful frame.
Every Art Morrison Enterprises (AME) chassis begins with American-made steel, and AME manufactures everything on site in Fife. The chassis begin as raw steel-tubing, and Art and his team make it into something beautiful and functional. Quality control is in the Morrison blood, and that in-part comes from Art’s father. He was a home builder, and instead of buying lumber to frame houses, Art’s dad personally cut down the trees and milled his own framing lumber. The Morrison bloodline is built on the idea of doing it yourself, and doing it right.
We wanted to know a little more about the business, so we went for a tour of the facility, and spent some time with Craig Morrison, Art’s son, who is now Operations Manager at Art Morrison Enterprises. Craig gave us some insight to the AME’s inner workings, and how they continue to advance as technology improves. Craig has been working in the business since he was 11-years-old. That’s when he started sweeping floors during the summer. He continued working summers between middle school, high school, and college, and finally in 2000, he started working there full-time.
The Art Morrison manufacturing area is clean and cool. When they are on the clock, however, this place is packed with skilled craftsmen and the sound of machinery working to make the magic happen.
“It’s really cool to work here with Art. We are father and son, but we are also best friends,” Craig explained. “We’ve got a relationship that a lot of fathers and sons don’t have.”
The Beginning
Art Morrison graduated high school in 1965. He was drafted in 1966, and went to Vietnam. He came home in 1968, and started college, only to find that it wasn’t for him. He dropped out after two weeks and started Art Morrison Enterprises in his garage.
“The first things he was making were hardcore drag-race items,” Craig explained. “Items like ladder-bar kits, four-link kits, and stuff like that. He was also building turn-key drag cars, and that’s what the business really was in the late ‘70s and early ‘80s.” It wasn’t until the mid 1980s that AME started getting into the mail-order business. In 1989, AME quit building complete cars and focused on the aftermarket parts business.
We found this independent rear suspension system and rear subframe in the shipping area at Art Morrison's headquarters where it was nearly ready to go out to the customer.
“The full-chassis stuff started in the late ‘80s for drag race-type builds,” Craig continued, “It was in the early to mid-‘90s that we started doing the Pro Street stuff. During the late ‘90s, we started to move from the really hardcore Pro Street stuff to the more mild Pro Street builds and hot rods.” Although Art Morrison started business with a heavy focus on race parts, over the years, they’ve evolved into a more hot rod and street rod-oriented business. Their chassis are used in various applications, from those looking to obtain high speeds to those looking for optimal ride-quality and control.
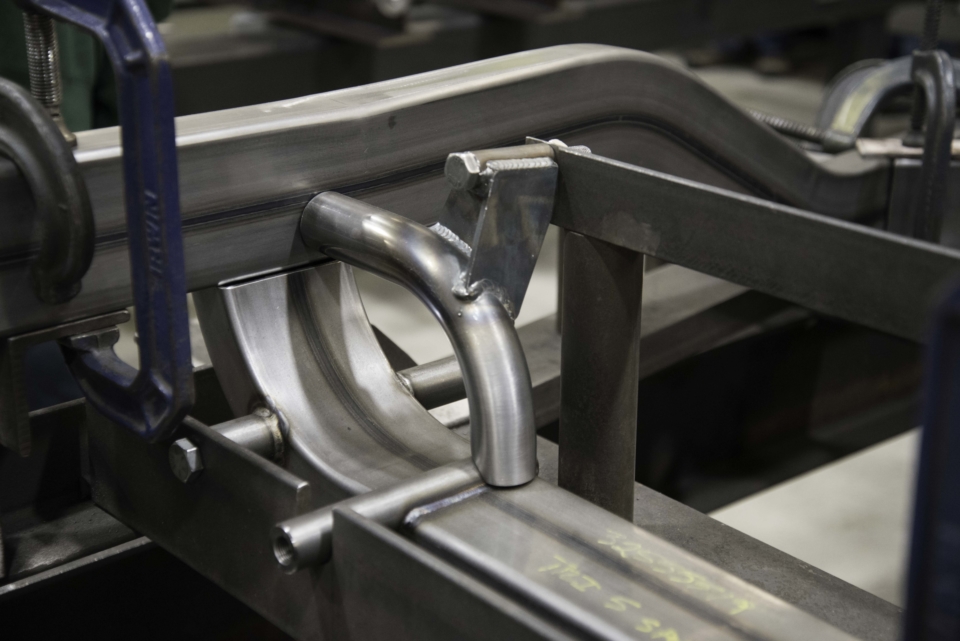
Morrison-built jigs are designed to ensure the new frame fits as good – if not better – than the original.
What initially set Art Morrison apart from others, was the quality standards to which they adhered, and the fact that the company cornered a market. “It was our ability to build a chassis that nobody else would, and the quality of our chassis that set us apart, Craig said. “What really brought us to the top was when we started the GT Sport series for the Tri-Five Chevys. We really focused on, not only a good fit, but the performance and handling of the suspension as well.”
These are two GT Sport chassis boxed up and ready to go to their new homes!
Art Morrison Today
The products made by AME set the standard for the industry. The folks here do great work, and that’s reflected in both the overall quality of the product, and the minute details that are sharply maintained. “We have a guy that does what we call chipping the frame,” Craig told us. “He goes over every inch of weld and knocks off every piece of cold spatter. When he does this, it does two things: One, it makes the weld look as good as possible, and Two, it keeps our quality control as good as possible, because someone is inspecting every square inch of weld.”
Quality welds are just a small part of the package.
Everything on an Art Morrison chassis is done by hand by one of their craftsmen. Even the tools and jigs they use for building the frames are made in-house. The frame components come in as 20-foot sticks, and start at the first step in the build process: cutting and bending. “We’ll cut it to the length we need and then bend it on the mandrel benders,” Craig explained. “From the mandrel benders, it will go to the other building where it gets loaded into the jig tables to get welded up.”
“Once the chassis is “chipped,” it comes to the shipping department,” Craig continued. “There, it is assembled, and the wheelbase and the track width are verified. We can then rough-in the suspension geometry.”
This frame is on a special table built at Art Morrison that can simulate the forces exerted on the front suspension while a car is driving. This is so they can play with the camber, caster, toe, and everything that goes into front suspension geometry!
Harnessing New Technology, Always Evolving
Some of the more amazing things we saw and learned about on our tour, were the research and development process, and some of the incredible tools they have at their disposal. AME is truly at the cutting edge of technology when it comes to designing new products.
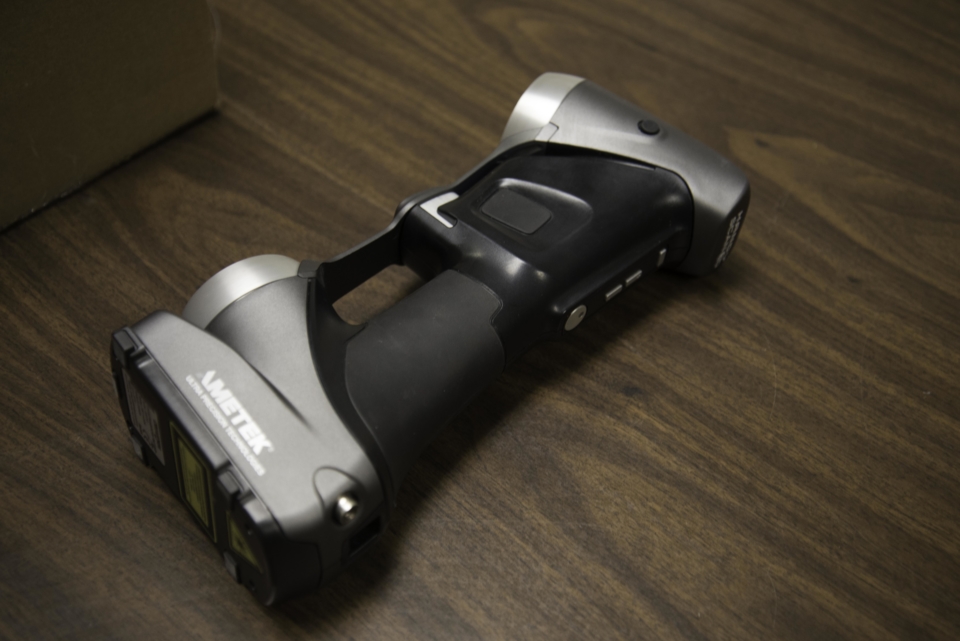
This little, handheld scanner costs a fortune, but has saved Art Morrison Enterprises an immeasurable number of man hours, and has greatly improved product quality.
Tools like a 3D scanner and FARO Arm Coordinate Measuring Machine, which is able to accurately – and in real time – scan and measure the dimensions of a car, frame, or whatever needs scanning. “The scanner is basically used to measure finished parts and make sure they are within a given tolerance. It can also be used to reverse-engineer things,” Craig detailed. “Previous to the reverse-engineering devices, we would use plumb bobs and note pads. It would take about 100 hours to measure a chassis. Now, we can scan a chassis and have 100-percent accuracy within three hours.”
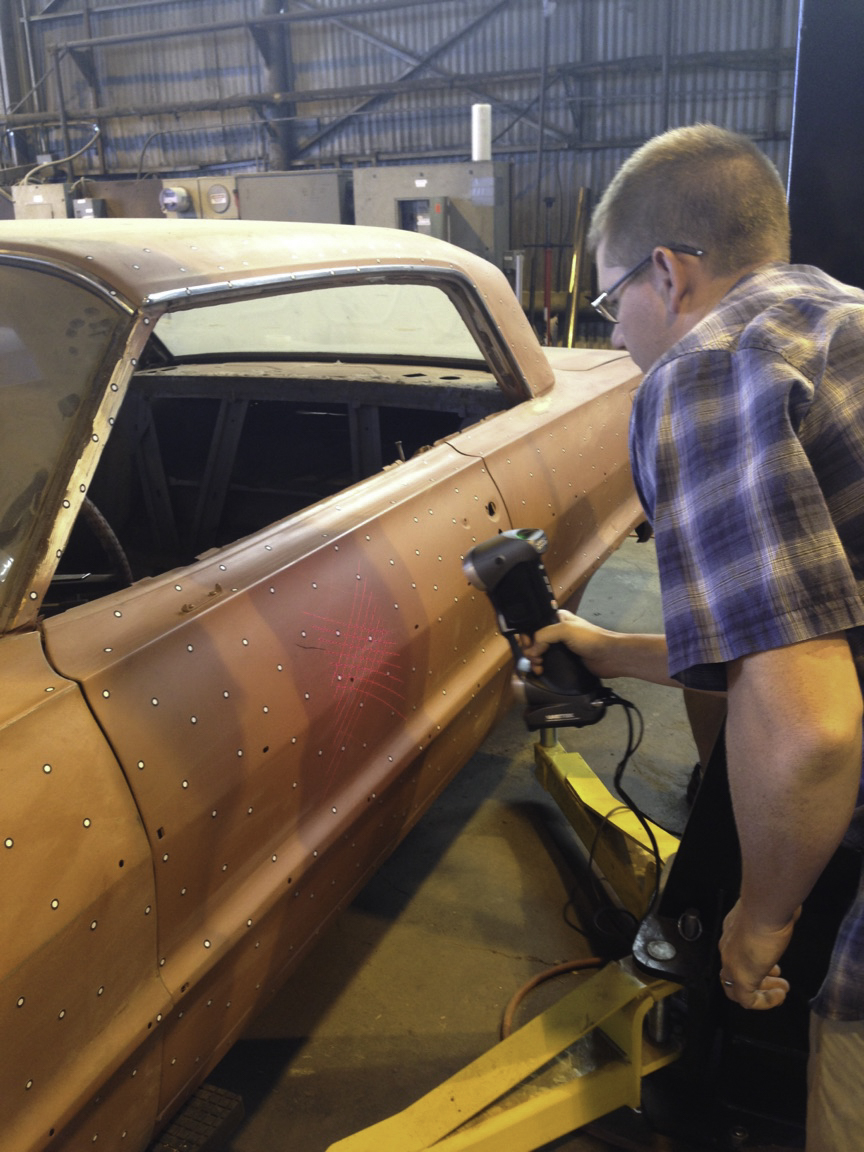
It works as simply as this. Hold the scanner, “paint” across the car, and the image will scan to the computer in real time.
The measuring device easily scans and maps the surface of whatever they are working on. It can capture the contours of a frame or the floor of a car. Now, instead of reverse engineering the frame, they can engineer a frame that will fit perfectly to the floor of a given car, allowing them to design a better-fitting frame. “I was able to take the tool to California in my carry on luggage, scan a car on site, then come home the next day,” Craig told us. “I could have flown back that afternoon if I wanted.”
This is what it looks like on the computer as the data is gathered.
The scanner generates images in real time, so you can watch the virtual design being illustrated on the computer. It does create unbelievably huge file sizes – we’re talking upwards of 20-gigabytes. The computer they use to process these files is so powerful, it has to be liquid cooled.
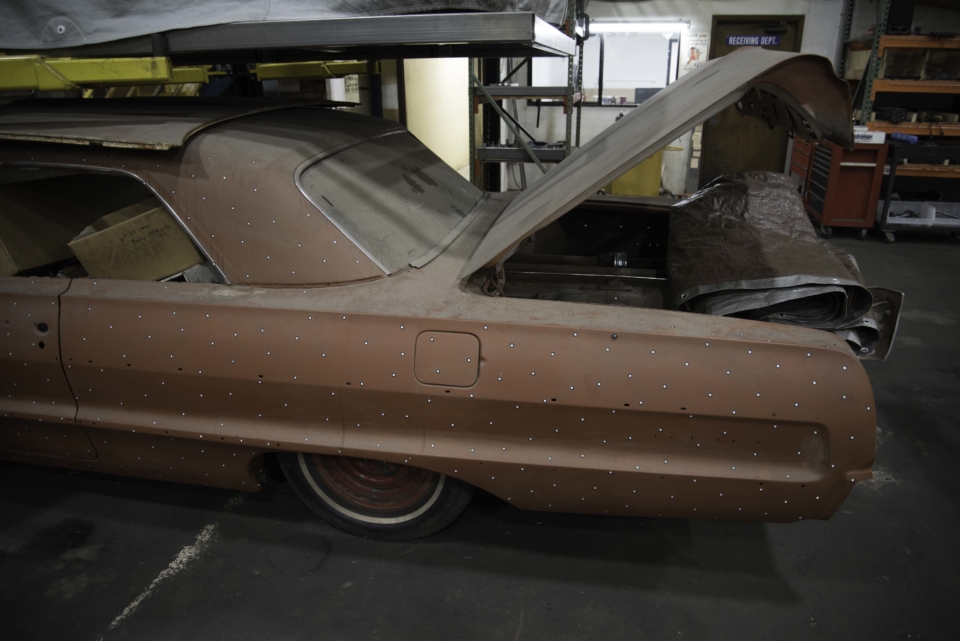
As you are “painting” over an area, the scanner recognizes the dots and creates a complete scan of the surface.
“It was a huge investment,” Craig explained. “Every time we do a scan, the scanner is getting us information that we had no ability to get before. For instance, we never had the ability to measure the wasted space between the floor and the chassis. We don’t even need the original frame anymore. All we need is the car body, and we can design a frame that is the best fit to the floor pan.”
3D Printing And Rapid Prototyping
The other way that Art Morrison is harnessing modern technology is through the use of 3D printing for rapid prototyping and fitment testing. SEMA has negotiated what is called a Tech-Transfer Program with some companies in the automotive industry, GM being one of them. These companies will share their digital renderings with companies like Art Morrison, so the aftermarket company does not need to reverse-engineer parts.
Through that program, Art Morrison was able to 3D-print parts like an LT-engine mount and a new rearend housing. They were able to do mock up with those parts without having to go through the process of reverse engineering them. “With the tech transfer agreement, we got the new engine block design from GM, and were able to print the portion of the engine block that we work with and use it for fitment purposes,” Craig said.
This new 3D printing also allows AME to get digital files of parts from other aftermarket companies so they can ensure a product is going to work in an AME chassis. This can even be done before the company that is making the part has even completed their first prototype! For example, Art Morrison was looking to use a stub axle that another company was in the process of developing. But, at the time, the company was three-months away from having a marketable part. “We signed a Non-Disclosure Agreement and they sent us the file,” Craig said. “We printed it, and were able to test fit in a live differential to confirm that it would work for us.”
What’s In The Future For AME?
As of right now, Art Morrison Enterprises has an impressive catalog of chassis and suspension systems available to their customers. Beyond the cataloged products they offer, Art Morrison can also do almost anything on a custom-order basis. Basically, there is no limit to what they can design and build right now. The folks at Art Morrison are driven, smart, and have their finger on the pulse of the market, so we really wanted to know what their plans were for the future.
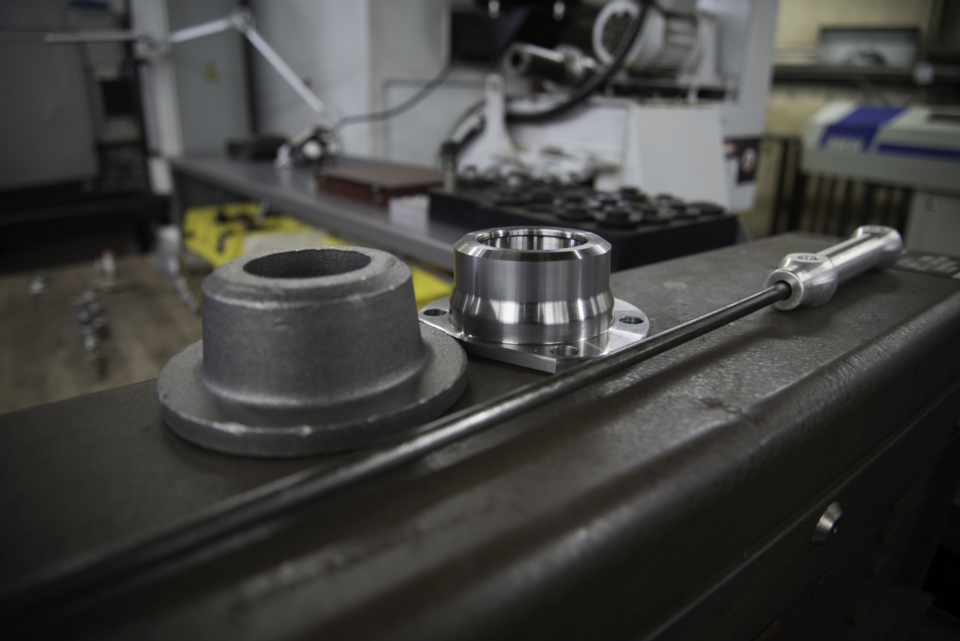
Their CNC machine can turn a rough, cast item into a finished product in minutes. That is a huge improvement over the old way.
“Without giving away too much, there are definitely more bolt-in chassis coming,” Craig said. “We are in a constant state of evolution, and we’re going to continue to refine and improve our suspension designs and utilize better shock and braking technology.”
In the arsenal of Art Morrison-built tools, this rearend "jig" is really cool. It can spin at all angles, and even has a little disc brake set up with a Shimano caliper.
We have a deep respect for what Art Morrison and his team have done for the automotive aftermarket industry. They’ve given many enthusiasts the opportunity to build their projects from the ground up, and they are always pushing to make things better. Art Morrison is still heavily involved in the business, and he loves what he does. “As far as a business, we are contacted early in a build process, when the enthusiast is still having a ball and a great time with their project,” Art explained. “It’s the poor guy that’s doing the upholstery work or the wiring that I feel bad for. They come into a project when car owners are over budget and slammed. We’re still at the beginning of the process and having fun.”
Make sure you check out the gallery to see all of the pictures that we took on our shop tour. There is a lot of really, really cool stuff here at the Art Morrison Enterprises headquarters in Fife!