When Jeff Schwartz launched Schwartz Performance in 2005, the Pro Touring movement was in its infancy and muscle car owners yearned for a full-frame chassis that provided superior strength and suspension geometry for vastly improved cornering performance.
Jeff saw an opportunity to build a chassis from the ground up that far exceeded the capabilities of the stock muscle car chassis. He utilized his diverse racing experience and road racing knowledge to create the G-Machine chassis. Competition is the ultimate test bed for developing and refining chassis and suspension systems. As such, Jeff has driven several iterations of G-Machine chassis and won several prestigious Pro Touring events. This allowed him to refine and improve the G-Machine since its inception.
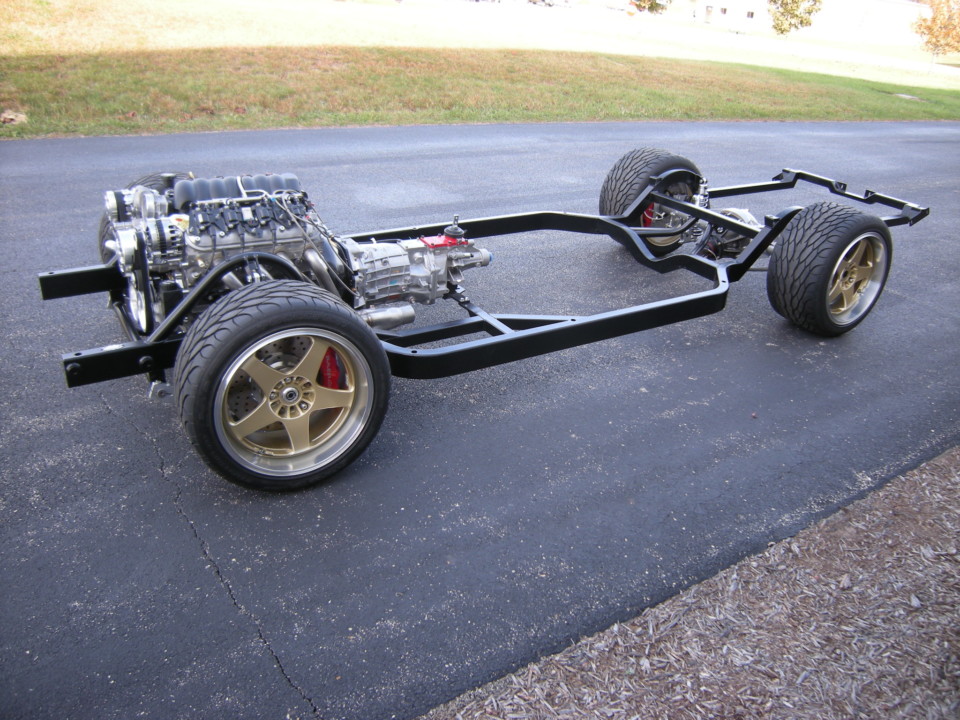
The Schwartz G-Machine chassis-design features include high shock-mount hoops, 2 x 4-inch main framerails, and a triangulated four-link rear suspension.
Over the course of his career, Jeff raced a mind-boggling number of vehicles on two and four wheels including road-race and motocross bikes, various sport-compact cars, GT1 Corvettes, and IMSA Camaros. Jeff posted numerous race wins and he set a new record in Showroom Stock B at Road America – he also posted five SCCA National track records.
Launching a Business
In 2003, Schwartz was laid off from his job as a manager at a manufacturing plant. With his experience in manufacturing, Jeff was well-prepared to step into his own business. He started working with Pathfinder, a Wisconsin-based dirt track chassis builder, on building a muscle car chassis, but eventually chose to do it on his own. In 2005, he opened Schwartz Performance in a small 1,600 square-foot shop in Crystal Lake, Illinois. About a year later, the G-Machine chassis was rolled out.
Schwartz Performance started with the GM A-body platform, but has since expanded its offering to include more than 20 different complete chassis systems for GM, Ford, and Mopar muscle cars. With this success, Schwartz now has 18 employees and occupies a 25,000 square-foot manufacturing and custom car assembly facility in Woodstock, Illinois, on the outskirts of metro Chicago.
Chassis Features
The G-Machine is a complete chassis conversion incorporating modern technology for ride, handling, and control that’s comparable to modern cars. In fact, the frame for most applications is 200-percent stiffer than stock, so the suspension geometry is maintained and the suspension correctly moves through its arc of travel.
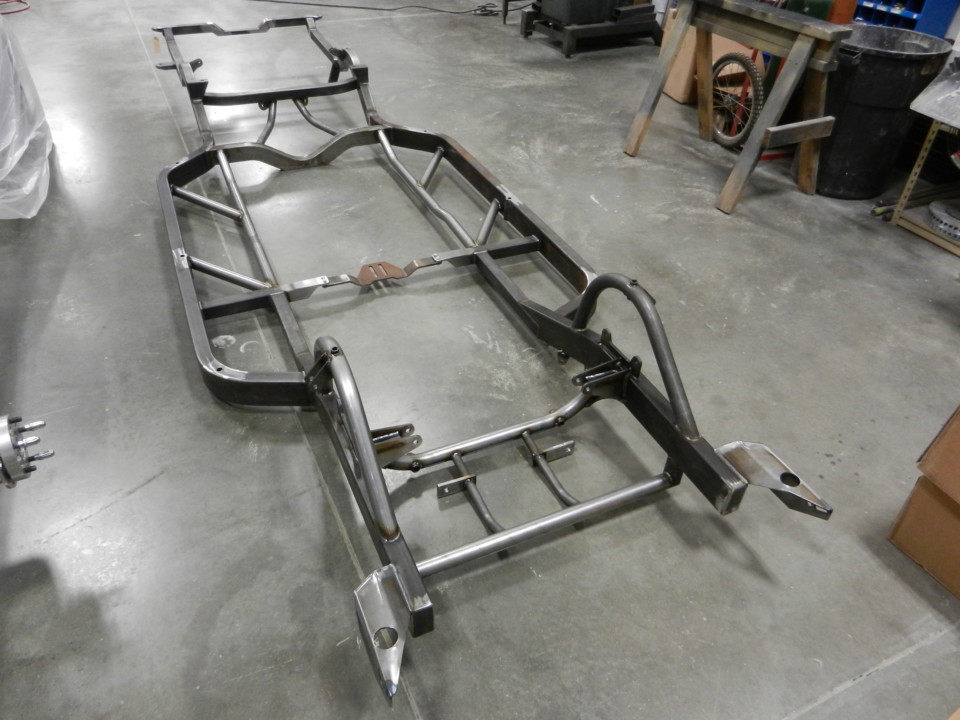
A top-view of a G-Machine chassis shows the engine cradle, transmission crossmember, and the extensive cross-bracing that produces an extremely strong frame.
Similar to most Pro Touring chassis, it has tubular A-arms up front, but the upper frame hoop to anchor the top arm is far taller than most other competing designs. The front arms use needle-bearings for a more precise and smoother operation. Rather than a stock-type sway bar, the G-Machine uses a NASCAR-type splined sway bar that better transfers loads during cornering.
There’s a high level of customization available for the chassis as well. Customers can choose between RideTech coilover shocks or ShockWaves products.. For the brakes, you can choose between the high-performance-base Wilwood or upgraded Baer brake kits. Power rack-and-pinion steering and a triangulated four-link rear suspension are two other prominent features. Top quality Teflon-coated spherical tie-rod ends are installed on all suspension pivot points. These provide exceptional strength, maintain alignment, and resist binding.
One of the most significant benefits is the G-machine chassis bolts directly to the body, creating a far stronger structure than the typical unibody chassis. Chassis flex is minimized and suspension performance is greatly improved. The chassis tubes are mandrel bent and according to Schwartz Performance Sales and Tech Manager Dale Schwartz, “The pieces fit nicely and produce smooth transitions, and the mandrel bent tubing doesn’t have crushed areas. We are not relying on someone to weld all four sides of the tube, so we’re not concerned with weld penetration – it’s very strong.”
“If you are running an LS with a Tremec and you have stock panels on it and steel bumpers, it’s probably around 51-percent front weight bias. You can’t really get that out of a stock frame unless you move the engine way back.”-Dale Schwartz
The G-Machine chassis is composed of exceptionally strong steel frame-rails that in many cases are lighter than the stock chassis. For the GM A-Body, 2 x 4-inch main frame-rails are used with 2 x 3-inch rails for the rear section. Most of the G-Machine chassis for unibody cars have 2 x 4-inch main rails with 2 x 2-inch rear kick ups. The G-Machine chassis for the Chevelle and other GM A-Bodies yields significant benefits.
Dale stated, “With an A-Body car, we save about 125 pounds from the stock assembly. If you’ve seen an A-Body front cradle, they are beefy in all the wrong ways. When you install our chassis, you add some weight to the back of the car because our rear section is a lot stronger. And our front suspension is a lot smaller and lighter weight; that helps with the weight balance as well.”
He continued, “If you are running an LS with a Tremec and you have stock panels on it and steel bumpers, it’s probably around 51-percent front weight bias. You can’t really get that out of a stock frame unless you move the engine way back.”
G-Machine Suspension
Schwartz Performance has continually developed and refined the G-Machine’s dual A-arm front suspension to improve its geometry. The Schwartz family and customers compete in autocross, road-race, and pro touring competitions, which provides a steady stream of information to identify aspects that need improvement. “It had gone through several different cycles [versions], said Dale Schwartz. “From 2006 to 2009, there were a few different variations of the front suspension that we went through, and finally got to the suspension geometry we have now.”
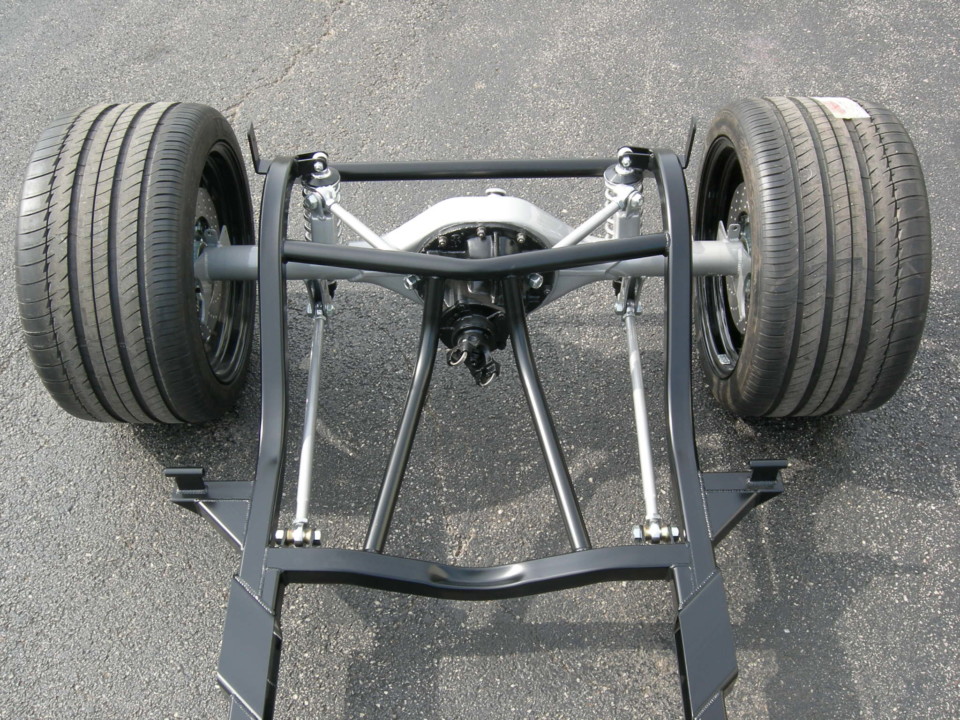
At the rear of the G-Machine chassis, you will find beefy 2×3-inch frame-rails, triangulated four-link rear suspension, and spherical rod ends.
The Schwartz G-Machine chassis features several distinct design features to optimize handling and prevent bottoming-out the shock or wheel against the fender. The front suspension’s shock hoop allows the use of longer shocks for better handling and consistent suspension performance. “Our ride height is a bit taller than others, so it’s not slammed like some of our competitors,” Dale explained. “Others have to use a stiffer spring to prevent the car from bottoming out against the shock, tire, and fender. We don’t have that issue.
“We have a longer coilover, so you don’t have to worry about bottoming the shock,” he continues. “Herb Adams (Chassis Engineering) said, ‘use soft springs and stiff sway bars,’ and that’s the same premise we operate on, because a sway bar will keep you planted in the corner and the soft spring rate will give you better suspension travel, ride quality, and overall ride experience.”
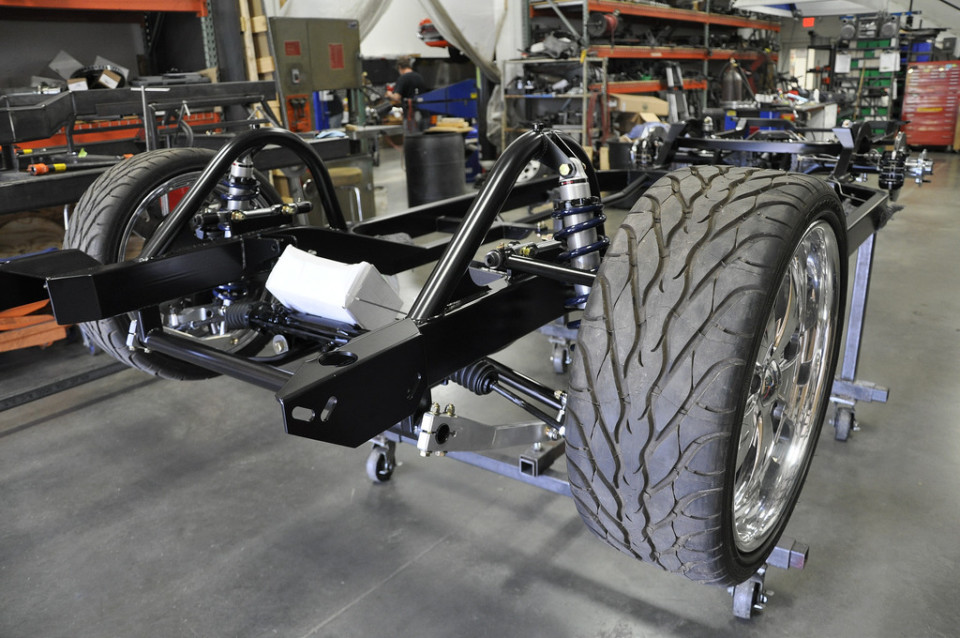
The G-Machine chassis features rack-and-pinion steering, splined sway bars, top-quality QA1 shocks, and spherical rod ends.
When muscle cars rolled off the assembly line about 50 years ago, they were equipped with a standard steering box with a ring gear. This antiquated technology deflects and has a lot of freeplay in the linkage that produces imprecise and vague steering response. Like other Pro Touring chassis, the G-Machine features a rack-and-pinion steering system.
Dale explains, “With the factory you could have a power box, and standard ring gear – it’s not going to be as precise as a rack-and-pinion, and you’re not going to be able to steer the car as quickly as a rack-and-pinion steering system. It’s an important safety aspect because you are going to have a lot quicker steering and lot more control over everything that’s happening.”
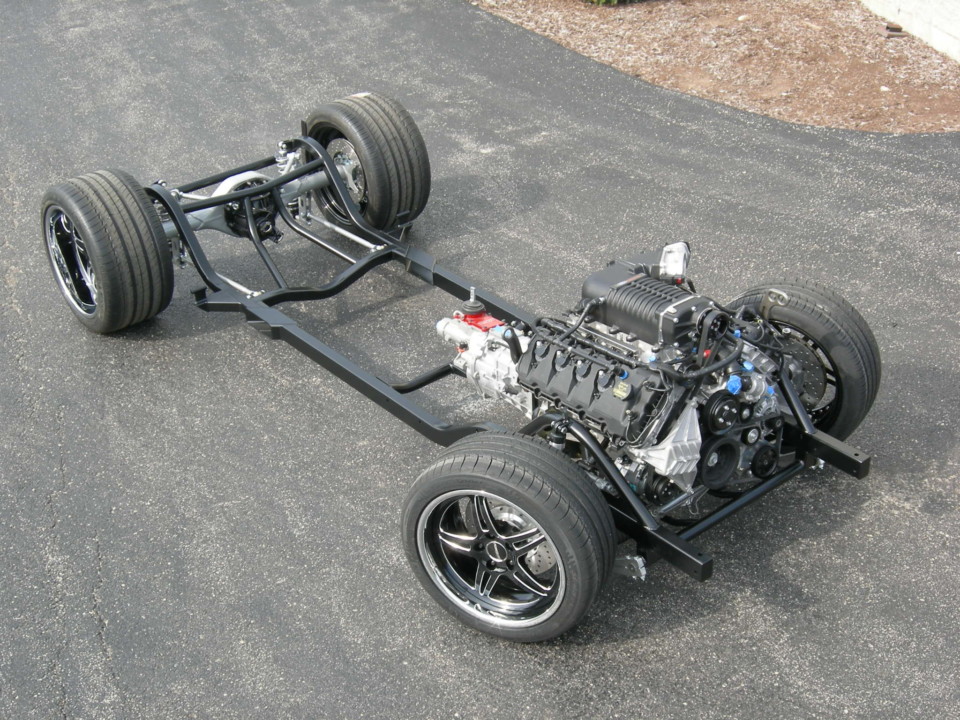
The G-Machine chassis accommodates the Ford modular engine – a popular choice for Mustang Pro Touring project cars.
Rear Axle and Brakes
Schwartz installs the Moser 9-inch full-floating, rear-axle assembly on the G-machine chassis, which produces several benefits. One, this stout limited-slip axle can transmit 1,000 hp or more. It also enhances brake performance because the axle shafts don’t slide around inside the axle tubes and press the brake pistons back into the calipers.
“A common rear axle moves around slightly, and when cornering hard, it pushes your pads and piston back into the caliper,” Dale said. “Then you go to hit your brakes and you have to pump your brake pedal a couple of times to push the caliper pistons back out. A full-floater [axle assembly] uses a tapered roller bearing and center axle nut. You can actually tighten preload into the bearing so you don’t have deflection. If you’re building a badass Pro Touring car, you need to put a full floater into it.”
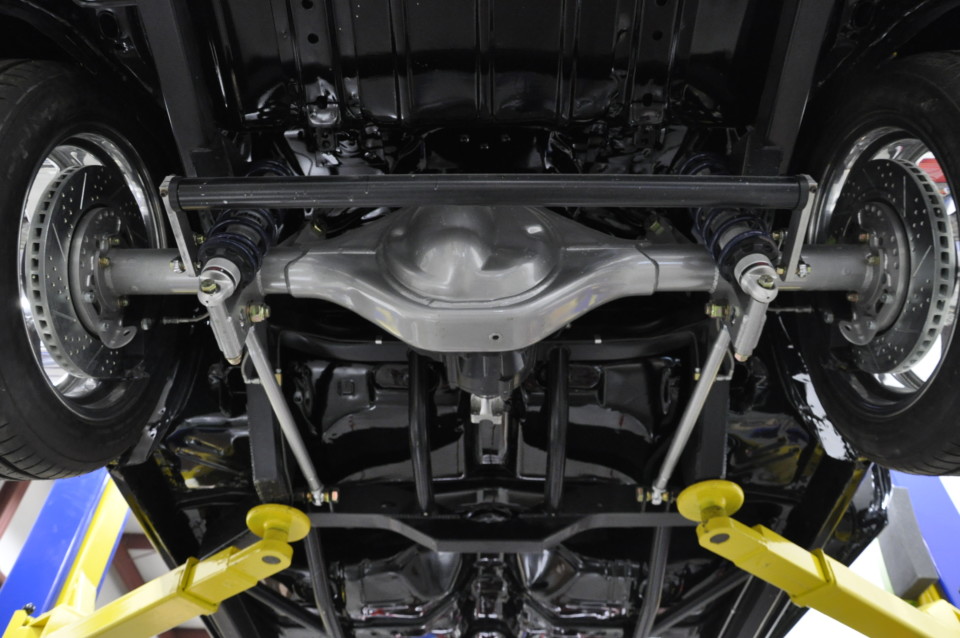
The stout rear suspension features high-performance coilovers, Moser 9-inch rear axle assembly and a massive sway bar for exceptional traction and durability.
You don’t want to cut corners when it comes to brakes. Schwartz offers several brake options, so the braking capabilities are suited to match the car’s performance. “The first option with the brake system is the 13-inch, six-piston Wilwood front, and a 12-inch four-piston rear,” he said. “I’ve seen some other companies using a Mustang II front suspension, and they will offer a 10.5-inch front rotor with a single-piston GM caliper. I don’t want that on my 500-horsepower muscle car.” Schwartz also offers a premium Baer Brake kit that contains 14-inch rotors with six-piston calipers for both front and rear.
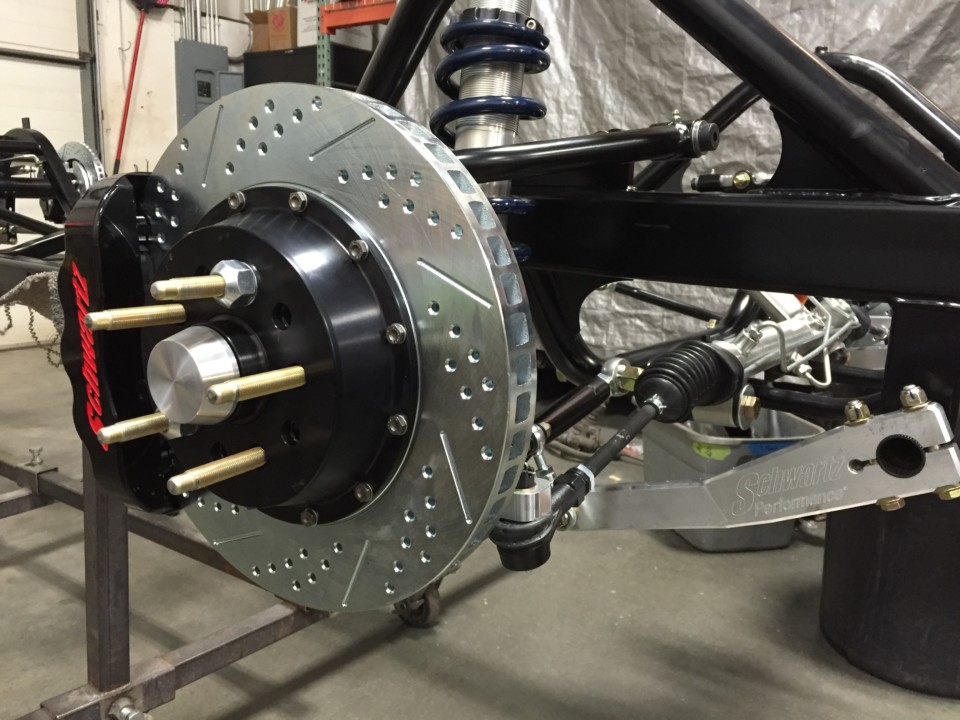
Schwartz Performance installs premium equipment on its G-Machine chassis, such as the splined sway bar, power rack-and-pinion steering and the six-piston cross-drilled and vented front brakes.
The company has recently released the G-Machine for several different truck models, including the Chevy Advanced Design and Series 2 pickups.
Dedication to Customer Service
Dale explains the company’s approach to developing and introducing a new G-Machine chassis. “We basically go off of demand. If somebody calls us up and he really wants us to build a 60s Chevy truck, we start the process when we are going to make one with that customer’s truck. We can get a solid car, just jig it, do some R&D, and eventually make it available [as a G-Machine chassis]. It’s hard for us to say no to a customer.”
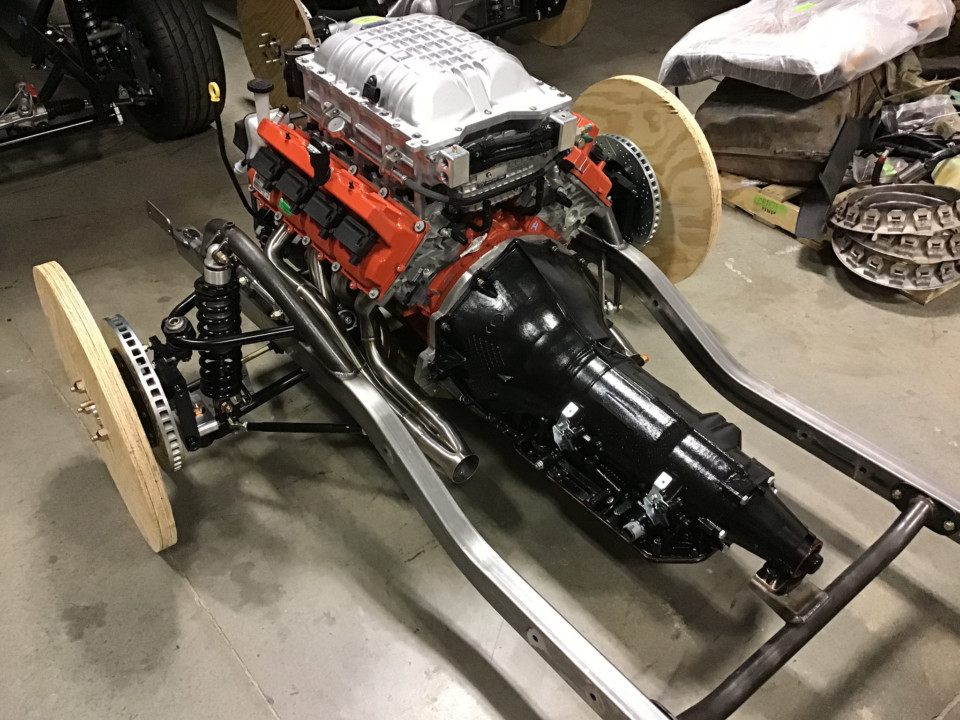
The G-Machine chassis supports some of the most powerful V-8 engines on the market, including this Mopar Hellcat powerplant.
Schwartz Performance has developed a close rapport with its customers and built many special one-off projects, such as a Chevy S-10 project for a customer in Russia, or a right-hand drive Plymouth Cuda. According to Dale, a large part of the business is custom car building.
“People love our one-stop-shop approach, because we can build their cars and we can basically do everything they need. We’ve done Dynacorn body and chassis packages numerous times. We offer numerous wheel and tire packages. We offer competitive prices on the products, so it makes sense for customers to buy it from us.”
Schwartz Performance has firmly established itself in the Pro-Touring and high-performance muscle car communities. The hallmark of a good business is repeat customers. “We have customers who have bought a half-a-dozen chassis from us because they love the way they ride and drive,” he said. “If we didn’t have that, and we just sold one chassis, and no one came back, that would tell you something. But we have a lot of repeat customers on the car build side as well.”
If you’d like to find out more about Schwartz Performance and their numerous offerings, check out their website, here.