If you’ve seen one muffler, you’ve seen them all, right? Well, that’s not necessarily true because while many mufflers may look similar on the outside, what’s on the inside makes a lot of difference to Flowmaster Mufflers. Calling themselves the muffler technology company, Flowmaster has been doing things a little bit differently for thirty years, and they opened their doors to their nearly 165,000 square foot facility to show us how they manufacture their mufflers.
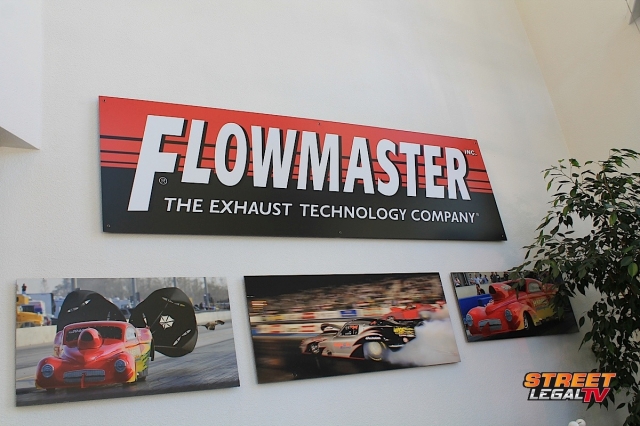
The sign says it all: The Exhaust Technology Company – something Chief Marketing Officer Nate Shelton is very proud of.
We visited them in Sacramento, California, where they are proud to say that every muffler and cat-back system is manufactured right there at their facility. From the design concept to the final product, Flowmaster does it all when it comes to their mufflers and cat-back exhaust systems. Doing things in house means that they can control the final product to make sure it’s done the Flowmaster way.
We don’t get to see inside a muffler unless it’s rusted out or torn apart. On our tour, we not only got to see inside a Flowmaster muffler, but inside Flowmaster itself, and the people behind the welds who start with steel and manufacture the muffler with that signature sound.
Inside a typical muffler you will sometimes see a fibrous material designed to reduce the sound. In the early years, people ran glass pack mufflers on their cars to get the sound they wanted – something with a bit of a rumble that had a bit more noise than a stock muffler. The fiberglass inside a glass pack muffler helps to dampen the sound and make the muffler quieter than a straight-through pipe, yet allows the muffler to sound aggressive.
Many mufflers today use that same basic design, albeit in a larger package; and while the packing material is effective, it isn’t the way that Flowmaster makes their mufflers. Flowmaster uses chambers and laminar flow technology to produce the specific sound they are aiming for, stating that those early sound dampening materials are bound to wear out due to the moisture and gases that pass through a muffler. This is why using chambers can eliminate packing and sound dampening material, and helps mufflers to last longer.
To make 46,000 muffler per month, you also need the space to store them when they're ready to ship!
Humble Beginnings, Racing Into Motorsports
Flowmaster was founded in Santa Rosa, California, and many years ago the mufflers were given a nickname of “suitcase muffler”. Flowmaster founder Ray Flugger was building mufflers to quiet down the sprint cars, and he needed a means to carry them around.
It was a simple solution: Flugger welded ‘handles’ onto his square-shaped mufflers and the “suitcase muffler” was born. That original muffler was one that quieted the exhaust note – without sacrificing power.
While the overall design of the muffler, performance levels, and different sizes may have expanded or changed, the same principle is still used today at Flowmaster. Instead of sound absorbing material, Flowmaster uses Delta Flow technology to reduce sound, create backpressure, and to create that signature Flowmaster sound.
CMO for Flowmaster Mufflers, Nate Shelton, told us, “We like to be called the ‘technology company’ because every muffler we build is designed and engineered to produce a specific sound, and still make power.”
Looking into Shelton’s past, you’ll see decades of experience under his belt in exhaust systems. He is very well known in industry circles, especially having been the only two-time chairman of SEMA.
Delta Flow Technology
The goal for Flowmaster is to make power and decrease the sound level. Delta Flow is why Flowmaster boasts themselves as the muffler technology company. Delta plates are strategically placed inside the muffler to divert the exhaust flow and create high and low pressure areas that help scavenge the exhaust.
But they don’t simply weld a number of plates and call it a day, the design has some significance behind it and each muffler uses multiple plates to help quiet the exhaust for the mild sound for family cars and SUVs, and fewer plates for the moderate and aggressive sounding mufflers. The plates are also varying sizes, which helps create the right high and low pressure areas, and to help the exhaust to flow better through the muffler.
A good look at the inside of Flowmaster's chambered muffler. Each component of every muffler is made on site.
Depending on whether you’re looking for higher performance or quieter rumbles, the size of the muffler and the number of delta plates will affect performance and sound. It’s not difficult to tell when a high performance musclecar is wearing a set of Flowmaster mufflers by the sound of it. There is something unique to it, and there is also something unique to how these mufflers are built.
If you don’t want the kind of rumble a musclecar has for your SUV or daily driver, you can install their moderate sound mufflers, like the Super 50, 50 Series, and 70 Series mufflers, and still maintain performance while attaining a better overall sound. With the exception of Flowmasters new Super HP2 muffler, which utilizes laminar flow technology, the rest of their street performance mufflers use Delta Flow technology.
Top: creating the 'can' for a Flowmaster muffler. Bottom: bending pipes for a cat-back system.
Laminar Flow Technology
The other type of muffler that Flowmaster manufactures uses Laminar flow technology, which relates to fluids or gases that flow parallel to each other at different rates. While Delta Flow technology has the exhaust gases flowing around delta plates to create high and low pressure areas inside the muffler, laminar flow is more streamlined, and allows the exhaust gases to flow through the muffler uninterrupted.
These mufflers, like the Super HP2, are perfect mufflers for street rods or lowered vehicles where real estate is at a premium. They are smaller in diameter, so they will fit next to a frame rail or up under the floor without generating too much heat. Still, Flowmaster does not use any sound absorbing material in their mufflers. The sound is engineered and designed into each muffler to produce the proper tone.
Inside the Super HP2 you will find ceramic heat absorption material to keep the outside of the muffler cooler. This reduction in outside temperatures enables you to mount the muffler up inside a frame rail, closer to the floor pan, which works well for street rods and musclecars. This allows the installer to ‘hide’ the exhaust by tucking the pipes and the muffler up out of view, without sacrificing sound or performance.
Inside The Manufacturing Plant, The Smiles Behind The Welds
At the facility, there are about 145 employees who are responsible for getting the Flowmaster muffler from design to finished product. Each muffler begins life with steel sheets and tubing that are bent or cut to the proper size or shape. Some of the tubing is cut into shorter pieces for the inlet and outlet tubes, and the rest is cut for either the inner chamber of some mufflers, or bent to shape for their cat-back exhaust systems. As we walked through the facility, there were bins full of bent or stamped tubes, and even more bins of completed mufflers waiting to be painted.
Many of our employees started out as parts makers or welders and moved up within the company, and are now machinists or engineers. -John Sharp
But more important than how many mufflers or cat-back systems are made, or how many machines were operating, was the teamwork and genuinely content people we met and talked to at Flowmaster. Many of the workers have been there for a long time; quite a few of them coming up through the ranks within Flowmaster. Production Manager, John Sharp, told us, “Many of our employees started out as parts makers or welders and moved up within the company, and are now machinists or engineers.”
It was no surprise that Sharp has worked for Flowmaster for 27 years. He could talk about some of those people who moved up on a first-hand account. As we spoke with many of the employees and asked them to show us some of the tasks they performed, they were more than happy to show us first hand what they do for Flowmaster, and to share their work experience with us. We asked a few of them about working for such a big company and they all seemed to enjoy the unique opportunities and to be a part of a famous brand known the world over. After all, when you’re at a car show and many cars are running mufflers that you built, it’s gratifying.
Spending time with some of the employees and with Nate Shelton, you can see a lot of that passion that employees have. It was often difficult to keep up with many of the employees because they were constantly moving, putting their focus on what they do within their work area. Whether they were cutting or bending pipes, welding or painting mufflers, it was pretty impressive to see how these mufflers all came together.
Cats and Headers
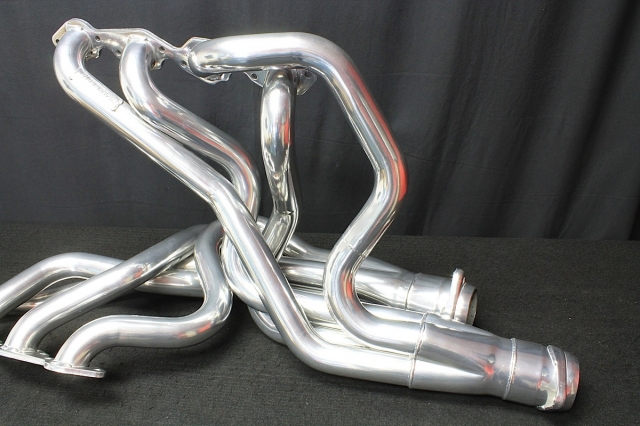
Scavenger Series headers are a newer product for Flowmaster, as well as direct fit and universal fit catalytic converters.
There’s so much going on inside the building, all at the same time, that no matter where you look you feel small. The building is huge and houses some elaborate equipment and machines to bend and weld components. Putting out 46,000 mufflers every month, Flowmaster keeps employees busy. They’ve also added to their performance exhaust components a full line of Scavenger Series Elite Headers, as well as direct and universal fit catalytic converters.
Flowmaster’s headers are available for many of today’s popular vehicles in both long tube and shorty-style, with some of the shorty-style headers being CARB certified and smog legal. Their 49-state catalytic converters are helping to clean up the environment on today’s performance musclecars and classic cars, as well, and these products are made in stainless steel, just like many of their mufflers.
Flowmaster is one of the biggest names in performance exhaust, and it doesn’t look like they’re slowing down. For a full line of products from the header all the way to the exhaust tips, Flowmaster has been improving the sound and the looks of exhaust systems for performance. Be sure to check out their web site to see what they have for your classic or modern musclecar, and be sure to get that signature Flowmaster sound for your favorite vehicle. See the gallery from our visit below.
Some of the people and machines behind the welds at Flowmaster.