Racers have long known that valve-seat angles steeper than the traditional 45-degree cut will improve airflow characteristics into the cylinder and boost power. The natural response from street enthusiasts is to adapt this same strategy, so Internet forums and bench-racing debates often focus on whether a 50- or 52- or even 55-degree angle is best for their engine. After all, it’s just a minor change that’s hardly noticeable to the naked eye. It’s not the same as other racing tricks, like moving to a 13:1 compression ratio—which could lead to detonation—or running .800-inch valve lift—which could challenge the engine’s idle and low-speed drivability.
What’s the deal with a few degrees of valve-seat angle, especially when everyone knows that it works?
Need a valve job? Most street and many racing applications can go with a standard 3-angle valve job. Thanks to Borowski Race Enterprises for much of the photography that illustrates this story.
“Unless you’re in the realm of changing valves frequently, these angles will not work for you,” warns Zeke Urrutia of Ferrea Racing Components, a manufacturer of performance valves. “Flow is one thing. Reliability is another.”
Obviously you want to respect the port design when selecting a seat angles. – Zeke Urrutia, Ferrea
While some high-performance street-engine owners may claim success with a 50-degree or steeper valve angle, there’s probably a good chance they haven’t compared leak-down numbers recently or run the engine that hard.
Not good for the street
“The steeper valve angle will wedge the valve a lot harder,” explains David Reher of Reher-Morrison Racing Engines. “Depending on the cam, it can beat up valve seats and cause metal transfer. You’re not going to run a 60-degree seat on the street, but you can in a race engine. Even then you have to get into some pretty trick stuff, like coatings and alloy seats. The same rules don’t apply for everything.”
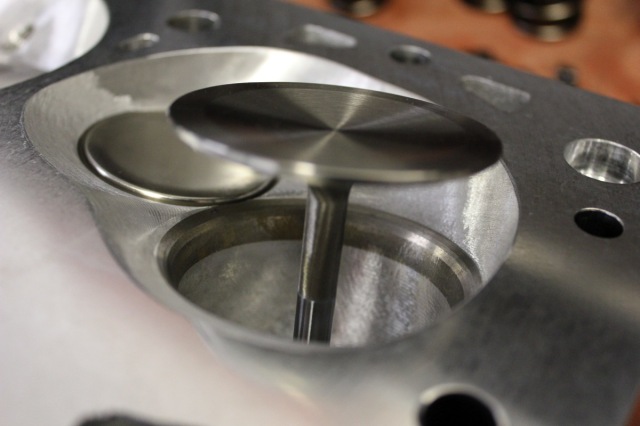
The cam profile and rocker choice play heavily into selecting a valve-seat angle. Higher lifts can take advantage of steeper angles while low-lifts are better off with a shallow angle.
“Using a 55-degree angle isn’t good for the street,” echoes Shawn Hooper, cylinder head instructor at the School for Automotive Machinists. “It’s so steep that it causes a wedge effect and will weld the valve to the seat.”
Durability issues aside, a steeper valve-seat angle may not be a wise choice for the street because the full potential often isn’t realized with a street cam.
“Every valve job depends on the application,” says Greg Ertman, cylinder head specialist at Borowski Race Enterprises. “If you run a high-lift cam, then you’ll want a 55-degree or steeper angle. With a low-lift cam, you run a shallow angle.”
CFD and other computer simulation tools are helping shape modern valves.
Yes, the valve job. One talking point often lost in the debate is that the valve-seat angle is just one contribution to complete the valve job. Remember, the air-fuel charge is directed not only past the valve but also through the valve-seat area below the bowl. And that’s where numerous angle choices come into play along with even more theories about how and where to grind metal.
“Every head and every application wants a different setup,” says Curtis Boggs, owner of Race Flow Development. “We’re creating a venturi. Each application wants a different shape, and the valve angle has a huge effect on that shape. It all depends on the flow curve you’re trying to create. What’s the lift range? Does it have to accelerate from a low rpm, like a dirt late-model? Or a drag-race engine with a 5-speed where you don’t care what happens below 8,000 rpm?”
The SuperFlow SF-750 flowbench is very useful when determining the proper valve job for a particular application. The company's FlowCom computer and software package does all of the math, unlike past systems where the flow data was computed by hand. Testing the varying seat profiles can be a time-consuming job, but is worth the investment if achieving every last horsepower is your ultimate goal. It's also the only way short of putting the engine onto a dynamometer to quantify the valve job, and is a tool like any other in your engine-building arsenal.
45-degree is still useful
“It’s application specific,” adds Boggs. “I just did a Super Stock head with 45-degree seats, and I haven’t used 45-degrees in years. It just happened to be the right seat angle for that application.”
Flowbench Advisory
Greg Ertman of Borowski Racing Engines says flowbench numbers can be misleading when making changes to the valve job.
“You may put a radius on the intake and it shows good flow, but you have to keep in mind reversion. You should flow the head in both directions; that is, flow the intake both like an intake and exhaust, then flow the exhaust both like an exhaust and intake.
“Let’s say the intake flows 400 cfm at .800-inch lift, then reverse the air and flow it like an exhaust and it gets 320 cfm. Then you make a change and only get 390 cfm flowing like an intake. Most people would say, ‘Oh, that’s bad.’ But it also flows only 280 like an exhaust, and that’s good.
“You want the intake to flow as good as it can as an intake and as crappy as it can as an exhaust. Because, during overlap you want it to be as hard as possible to go back up into the cylinder head. Whatever goes back up the intake just contaminates the fuel for the next cycle.”
Just what is the valve job supposed to accomplish? First, it has to provide a seal between the valve and seat to ensure there is no loss of pressure in the cylinder. The valves and seats must therefore be properly sized and concentric in addition to sharing complimentary seat widths and angles. The sealing action has become a little easier with today’s higher spring rates, but any number of irregularities such as carbon deposits or a loose valve guide can affect sealing.
Next, there has to be enough contact area on the seat to help transfer heat from the combustion chamber to the coolant passages. Consider the total surface area of a cylinder and combustion chamber, and the valves make up a significant portion, so its share of heat dissipation is critical to a performance engine. That’s why valve seats on the exhaust valve are usually wider than the exhaust.
Chasing horsepower
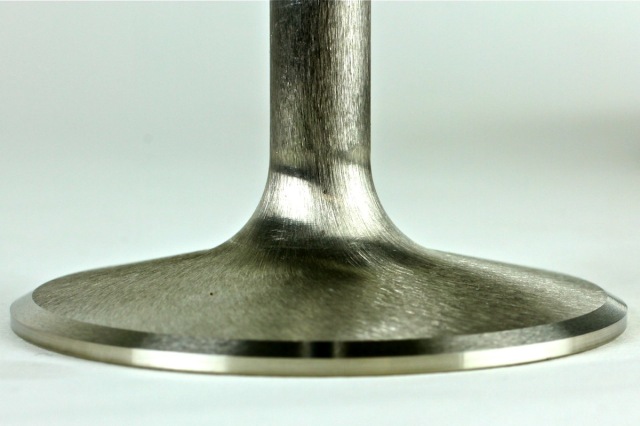
Very few valves outside the diesel market have 30-degree seats, but one notable exception is the Boss 429 valve, right. This Manley Boss valve measures 2.280-inch with a 30-degree seat measuring .100-inch wide. There’s also a .060-inch margin.
Finally, the valve job must optimize airflow in and out of the cylinder. That’s where testing and CFD simulation programs have led to different seat angles, especially in very high valve-lift applications like Pro Stock. Which begs the question: If Pro Stock is running close to 1.2-inch valve lift, how can a few degrees of seat angle make a difference?
“These guys are chasing every ounce of horsepower,” stresses Manley.
“It’s only a few degrees but it thins out that area of the margin and makes it sharper and captures that intake flow much faster,” adds Urrutia.
“We’re so limited on the actual valve size,” explains Hooper. “If we can get something to make the port think it has a bigger valve, then we have a benefit. Also, we’ve been making the intake bigger and exhaust smaller, so we really need to work with the exhaust side. Going to 55-degrees helped open up the venturi without killing the port.”
“The seat angle is not always the magic,” reminds Boggs. “The magic is in the angles above and below it and how that shapes the venturi. People tend to fixate on the seat angle. It’s only one piece of a multi-angle puzzle. The whole thing is about creating the shape of the venturi.”
What’s the choking point?
If you think about how the valve openings are really the choking point in the overall airflow path chart, it’s easy to see how much impact the valve job can have on engine performance. Opening up the throat by just a few hundredths of an inch is much more effective than peeling one or two tenths off the intake port at the opening. But the engine builder will always be limited by the valve size, which is limited by bore size and other factors.

Here’s a cutaway of a Toyota NASCAR engine, although no secrets will be revealed. However, you can get a sense of the airflow down to the valve and how the valve job could enhance the dynamics if properly cut.
“What’s most critical is the size of the throat, the smallest area below the seat,” says Reher. “That also is correlated to valve lift. A lower-lift cam needs a smaller throat so the air turns better. At higher lift you end up with a bigger throat. There’s not one thing you can do to a cylinder head that doesn’t affect something else.”
A popular trend in many high-end engines is five angles on the cylinder head seat and three angles on the valve—four if you count the margin. Most experts agree that these additional angles on the head are necessary to optimize airflow into the cylinder; therefore, the intake side should never be blended around the seat.
“Obviously you want to respect the port design when selecting a seat angles,” says Urrutia. “Often the first angle the air grabs is the trick to the trade.”
Here's a comparison of seats on two heads found in the Borowski shop. On the left is a 50-degree seat with four angles below and one on top. Cylinder head specialist Greg Ertman says the width and angle of the bottom cuts were a combination needed to achieve the desired final diameter before blending into the bowl. On the right is a vintage double-hump SBC with a 45-degree seat. Ertman was limited with the grinding for fear of hitting a water jacket.
“You want a sharp transition. You do not want a radius,” warns Ertman. “The only application for a radius would be on the exhaust. For the intake, sharp angles help keep the fuel atomized. Alcohol engines really need sharp angles because of the big fuel droplets, especially naturally aspirated.”
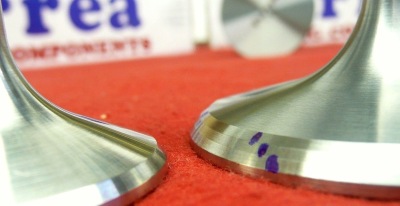
Here’s a set of Ferrea valves ready for install. The 1.600-inch stainless-stell exhaust on the left is a simple single 55-degree seat angle with a thick margin. The 2.250-inch titanium intake has a three-angle profile, including the 55-degree seat.
“There’s no intake that we’re going to blend all the way to the seat,” adds Hooper. “It just won’t work.”
There are some applications where some intake blending may offer an advantage, such as NASCAR where engines are designed to run extremely hot (so the teams can tape up the grille to improve aerodynamics), and the heat helps keep the fuel atomized. But for most race engines, a multi-angle valve job is quite effective. However, no formula exists for engine builder to shape the best possible valve job for a given application.
Don’t look for a magic formula
“There is no magic number,” confirms Boggs. “Everyone wants to simplify it, but it’s not that simple.”
“You’re going to have to determine those numbers with testing and flow work,” says Reher. “There’s not a set number.”
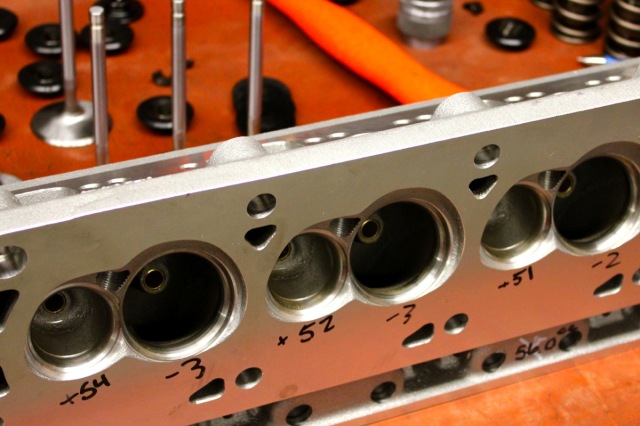
Valve jobs are also key to ensuring that valve-stem protrusion is even across the cylinder head. The numbers on this head at Borowski Racing are Greg Ertman’s code for determining how much to sink the valve.
There are some tips and suggestions that come as close to a general consensus regarding the degree of transition between angles flowing from the port to the seat.
“The intake really doesn’t like a lot of little angles. A transition of less than 10 degrees doesn’t work great,” says Hooper. “I wouldn’t want a 45 then a 50 next to it. You want a good distance, at least 10 to 15 degrees spread between them.”
“I want at least three angles below the seat, sometimes four,” says Ertman. “For most applications I try to make those angles 12 degrees more than the previous angle. The width is whatever is required to get the bowl area the size I want based on the valve size. The last angle is whatever it takes to blend in.”
For the single angle on the chamber side or the top cut, there again is no consensus.
Precision machining is required to achieve quality multi-angle valve jobs. From left, students at the School Of Automotive Machinists work with a Sunnen valve guide and seat machine. A Newen CNC valve-seat machine at Borowski is shown in center and in action to the right. It can cut numerous angles at once to ensure exact dimensions and angles.
“With higher lifts and better designed chambers, 35 is as low as we go for the top cut. Most of our cutters have a minimum of a 37-degree top cut,” suggests Hooper, who works mostly with 55-degree seats on race engines. “It allows us to open the venturi while maintaining the proper transition from the port to the chamber.”
“For the top angle I always want to eight to 10 degrees less than the seat angle,” says Ertman.
Coating for durability
There is some consensus on the width of the valve seat for the majority of applications. The intake side is generally around .040- to .050-inch wide with higher heat applications stretching to .060-inch. Of course, Pro Stock pushes the envelope all the time and runs in the .025- to .030-inch range. On the exhaust side the seat is upwards of .080- to .100-inch to transfer the heat to the seat material, which is another variable that must be considered.
“Proper intimacy between the valve material and the seat material is key,” says Manley. “Not only to provide adequate thermal conductivity but also with regards to comparable hardness so one doesn’t eat up the other.”
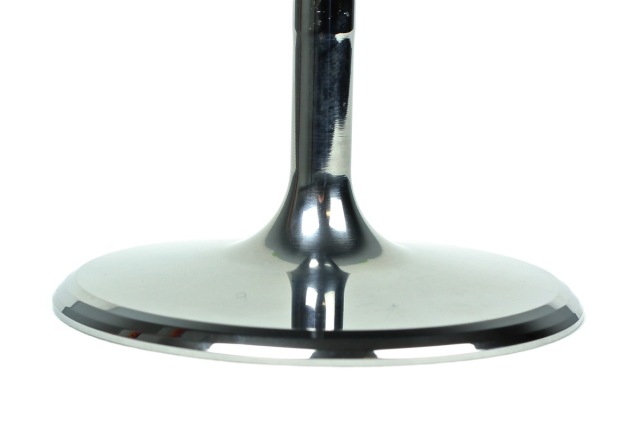
Here’s about as close to a current Pro Stock coated titanium valve as you’ll see outside the engine. It has a 55-degree seat and a thin .040-inch margin, but the angles cut for the multiple backcuts are not being released.
Here's the Pro Stock valve in comparison to a 55-degree titanium exhaust valve on the left, and another titanium valve with a 45-degree seat. The exhaust valve measures 1.600-inch and has a seat width of .090-inch to help transfer heat to the seat. It also has a 42-degree backcut and a .075-inch margin. Note the corner radius on the margin to help with flow and reduce chances of a hot spot. The 2.200-inch intake valve on the right has a .050-inch width for the 45-degree seat. There's also a 33-degree backcut that measures .080-inch and a .080-inch margin.
When using titanium valves with steep angles, some type of copper alloy valve seat is preferred. Beryllium copper is popular, but some engine builders avoid it on the exhaust side due to beryllium’s carcinogenic warnings. Other materials such as nickel and silicone are being added to copper to provide the necessary properties for heat transfer and durability. The valves must also be treated to a diamond-like coating (DLC) or chromium nitride coating (CrN) to reduce the chances of metal transfer or micro welding.
“Even for a drag race engine that only runs for a few seconds, we put coatings on titanium valves,” says Hooper, “because with aggressive cams they’re opening and closing so violently.”
The back angles on the valve and the radius that blends into the stem are additional variables that contribute to airflow performance. Again, there are numerous theories as to the number of back angles and their transitions as well as the choice between tulip- or nailhead-style valve designs.
“There’s a common thought that the tulip exhaust valve helps everything,” says Reher. “It doesn’t if the throat’s too small. Then it’s better with a nailhead.”
How steep can you go?
On the chamber side, engine builders also work with different thickness of valve margins as well as options to angle-cut or radius the margin. One consensus on valve design is that the exhaust margin needs to be thicker than the intake.
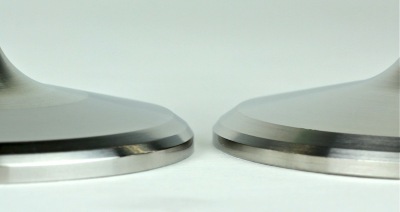
Here are two titanium intake valves that look nearly identical but there are subtle differences that would be beneficial to specific applications. On the right is a 52-degree, .050-inch-wide seat with a 35-degree backcut and a .080-inch margin. On the right is a 50-degree, .050-inch-wide seat with a 35-degree backcut and a .070-inch margin. Both the backcuts are .080-inch wide.
“Usually it’s .010- to .020-inch wider on the exhaust margin,” says Hooper. “You might go .040-inch on the intake and .060- to .080-inch on the exhaust.”
“Top Fuel runs nothing but 55-degree with real thick margins on the exhaust side,” says Urrutia. “You want to corner-radius those margins so it doesn’t prone itself to hot spots.”
“You have to be very careful not only with the margin thickness but the relationship of the back angle to the dish angle, if you choose to dish the valve,” warns Manley.
“The back angle depends on the valve lift and the shape of the valve,” adds Reher. “Some can run one angle very effectively and some will be better with two. You’re making a transition on the valve to the seat just like you’re making a transition in the valve bowl to the seat. And those transitions vary according to the cam and lift curve.”

This cylinder head will go on a blown alcohol engine. The copper beryllium seat is machined with a 50-degree seat and 40-degree top angle. Just below the seat is a very narrow 60-degree cut that Ertman says helps a 50-degree flow like a 55-degree. The next three angles are wider than usual to help minimize the large fuel droplets associated with alcohol.
Clearly, synergy between the valve seat area and the head of the valve is crucial to optimum airflow and engine performance. Most of the development and improvements come from trial and error and flowbench tests with computational fluid dynamics (CFD) simulation offering additional insight into all the angles that must be considered. But just how steep can racers go to pick up a couple horsepower before there’s a point of diminishing return?
“Some heads go up to a 65-degree valve seat,” says Boggs. “But it gets pretty ugly on keeping material.”