We talk a lot about camshafts here on EngineLabs, because, well, they are the heart of an engine. However, we usually talk about the camshafts specs — lift, duration, lobe separation — and the science associated with crafting those specs. However, there is another, extremely important cam spec that often gets left in the background — camshaft material.
There are a number of considerations when it comes to selecting a camshaft material. The primary consideration is valvetrain configuration and then intended use. There are a number of materials COMP Cams manufactures their cam cores from, which fall into four main groups. To explain those materials, COMP made a tech video with Outside Sales Group Director, Mark Campbell.
Cast-Iron Cam Cores
As the name implies, a cast-iron core is just that. It appears to be an unfinished cam, cast in the rough shape of the camshaft. “[Cast-iron camshsafts] start off as an unground lobe camshaft blank. The blank is very rough on the lobes. The lobes are cast to a certain range of lift and duration, but the camshaft is unfinished. However the journals [on a cast cam blank] are pretty much finished,” Campbell explains.
“These are usually the blanks we’ll use for a flat-tappet camshaft, either solid- or hydraulic-style lifters. There is the odd situation where we’ll do a flat-tappet cam in tool steel, but that’s a whole different discussion. The distributor gear is hobbed on, but can sometimes be pressed on. They all use a cast iron distributor-drive gear, and you can pretty much use any gear that comes on your stock or aftermarket distributor.”
Camshafts from COMP ground from a cast iron core typically have a part number ending in “-2” through “-5”.
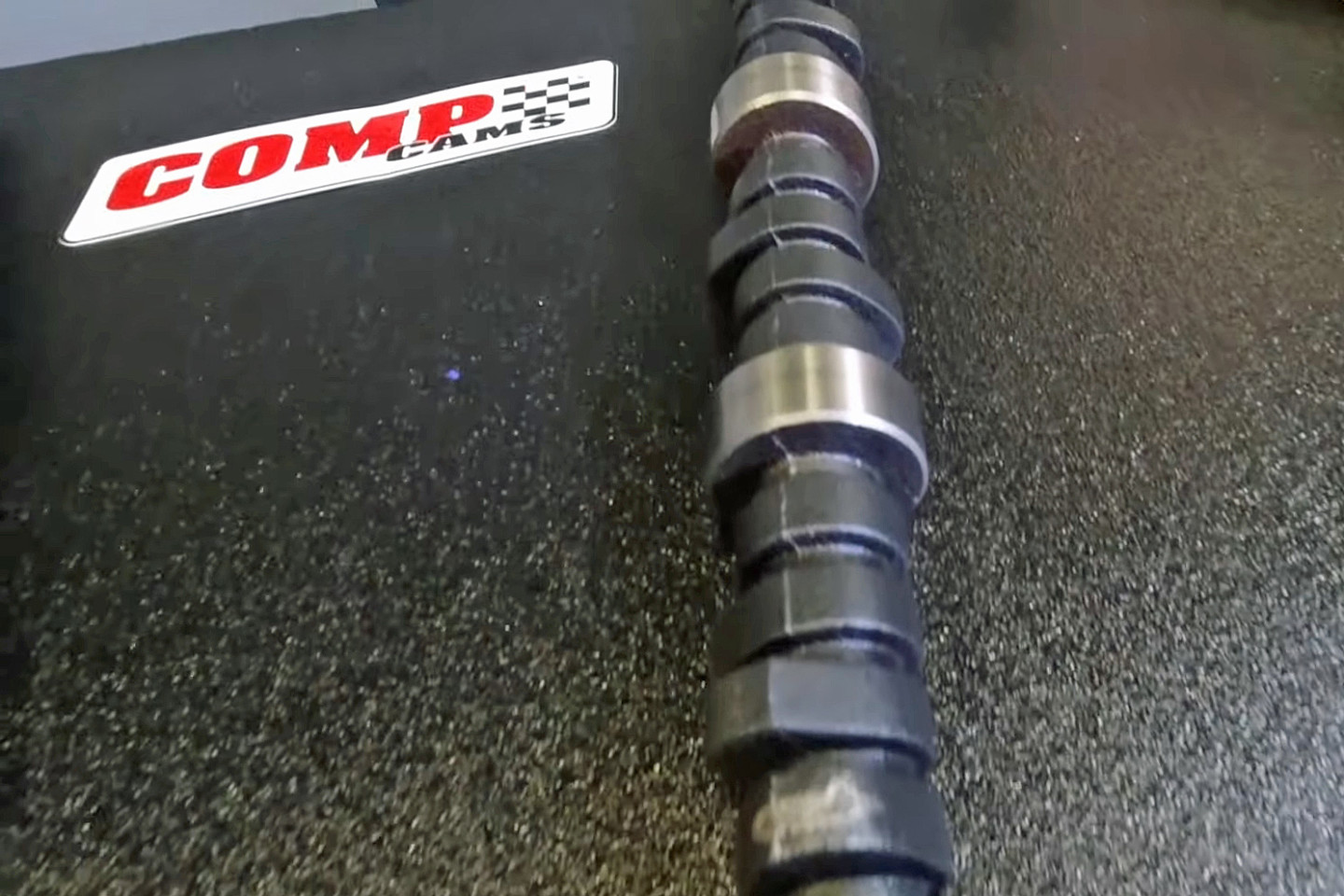
Here is a cast-iron cam core. You can see that the journals have been mostly finished, but there is still a visible casting line on the lobes. As you can see, the lobes on this core are very close to final dimensions, due to the shallow heat-treat depth of cast-iron.
Austempered Iron Cores
Austempered iron camshafts, also known as Austempered Ductile Iron (ADI), are similar to cast-iron, in that they are iron, and they are cast, but that’s where the similarities end. “Austempered iron is not the same as the cast-iron used on a flat-tappet cam,” says Campbell “ These are typically used in hydraulic-roller or mild solid-roller street-style camshafts. [Austempered iron] gears are compatible with traditional distributor gears, but we do recommend an upgrade to a melonized style of gear, but it’s not absolutely necessary.”
Like the cast-iron cam core, the Austempered iron blank has a roughed out lobe shape and layout, with journals very closed to the finished size. “We have literally hundreds of different styles of these cores. Once we know what kind of camshaft we’re grinding we’ll pick the proper core that has the right lobe configuration and then grind the camshaft,” explains Campbell.
COMP’s Austempered iron cam cores have bosses for mechanical fuel pumps, since they are also used in retrofit kits for engines without EFI, and will typically have a part number ending in “-8”.
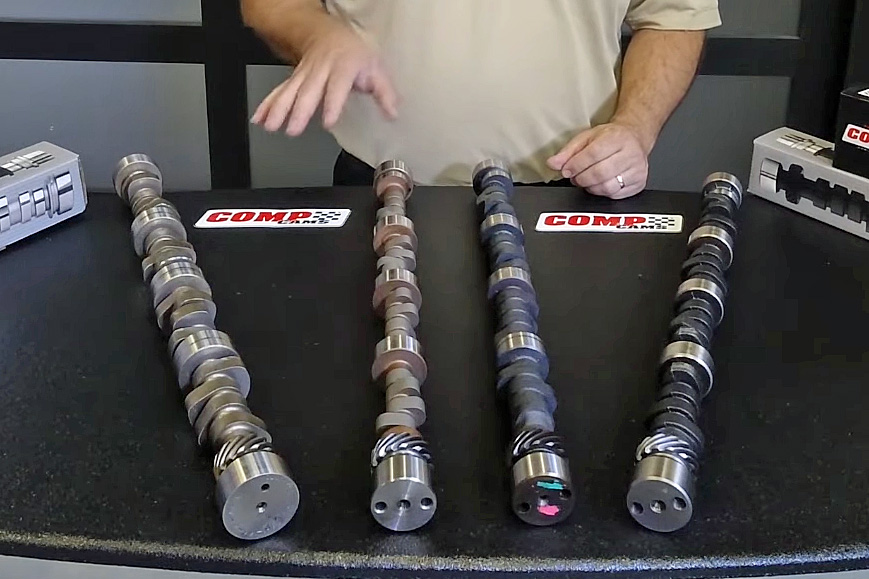
One consideration with different camshaft materials is distributor-gear compatibility. Most camshafts have hears made from the same material as the camshaft, but occasionally, pressed-on gears of a more street-friendly material will be used.
Billet Steel Cores
The next step up is a big one, and that is going from a cast core to a billet one. The term “billet” can be confusing since billet cam cores are made from a number of materials, primarily 5150 or 5160 steels. “Our billet steel cams can also be made from 8620, 8660, or even 9310 steel, which is popular in Top Fuel camshaft applications,” says Campbell. “Most billet camshafts will have a steel gear on it that is not compatible with a cast-iron style distributor gear. We do have some billet cam cores with a whole section pressed on so that a cast gear can be used on the street.”
Unlike what most people think when the word “billet” comes up, billet steel cam cores don’t sit on the shelves with a 360-degree cam lobe waiting to be turned into anything in the world. “The lobes are roughed-in to a certain size,” Campbell reveals. “There are a lot of different versions of these cam blanks, with different firing orders and all kinds of different journal sizes, and things like that. There are a lot of variants of billet cam cores.”
Anything made from a billet core will typically carry a part number ending in “-9” or higher.
Tool Steel Cores
Also a type of billet steel cam core, tool-steel cores are different enough from any of the other billet alloys, that they deserve their own section. “Tool-steel can be used in all kinds of applications, but is typically reserved for all-out racing applications. We have several different tool-steels here at COMP, and a tool steel camshaft tends to be a much more expensive piece,” Campbell says.
One thing about tool steel cores, which is visually obvious in the video, is how much larger the tool-steel blank lobes are. That is because when the blanks are heat-treated, the tool-steel heat treatment penetrates much deeper than other alloys. “The heat treat on a tool-steel camshaft is different from any other camshaft. The depth of hardness is very, very deep, so we can cut a tremendous amount off of that lobe without having to worry about cutting through the heat treat,” says Campbell
That flexibility is welcome, as when you are into super-custom, high-end racing camshafts, having versatility in core selection makes life easier. “We generally leave the tool steel blanks much larger than final size, because there are so many journal size variations. Because we can cut so much off of a tool steel lobe, the blank is much more versatile than the rest of them. Most billet cams we do are 50, 55, or 60mm or even bigger. We do some 70-plus-mm camshafts, and those are all typically in tool steel,” Campbell explains.
Also of note is that with a tool-steel camshaft, you will need an upgraded distributor gear. Tool-steel cams from COMP will generally have a part-number ending in “-17”.

Here you can see that a tool-steel cam core has much larger uncut lobes. This is due to the much deeper heat-treatment achievable on tool-steel. That means each core has a much wider range of specs than say, a cast cam core.
Heat Treatment
As Campbell alluded to, the material the camshaft core is made from, dictates its heat-treatment process. That process ultimately dictates the range of specs a given blank can be finished to. “The heat treat depth on each individual material varies quite a bit and that’s something we have to consider when selecting which core to use for a cam. Like an 8620 blank vs. a 5160 blank; you can cut a bunch more material off of the 5160 than the 8620 because of the heat treat depth,” Campbell explains.
“We have literally thousands of different cores on the shelf. While one blank might work for 220 to 230 degrees of duration at .500 inch of lift, if you wanted to go to 240-250 at .600 lift, you’d need a new core, because that particular heat treat depth only allows you to go so far.”
Ultimately, your application and valvetrain configuration will dictate the proper material for your camshaft. Then, your particular camshaft specs will dictate which cam core blank will be used to ultimately create your final bumpstick. And if you think you can dream up a camshaft that COMP can’t grind, that’s a tall order, considering the thousands of blanks sitting on the shelves in the grinding department.