Hop into the Wayback Machine with us for just a moment, and let’s visit 2014. February, to be specific. The Seahawks crushed the Broncos 43 to 8 in Super Bowl XLVII, Bitcoin was trading in the mid-$600 range, and we published an article detailing the coilover installation on Project Y2k, our 2000 Corvette project car.
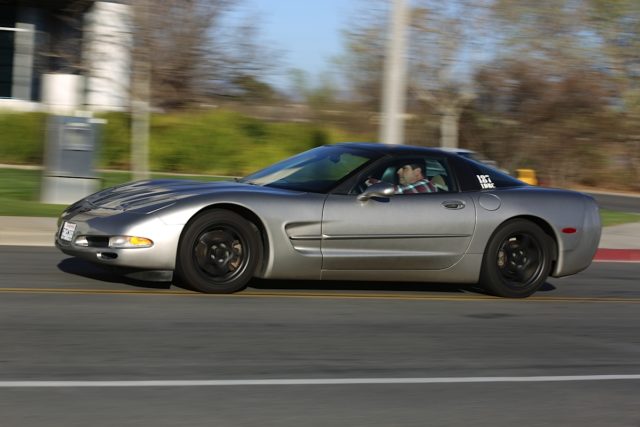
Professional driver on a closed course. Do not attempt. No animals were harmed in the making of this photo. Except the ones we ate that day for lunch.
Fast forward to 2017; The Falcons blow a 25 point lead to lose Super Bowl LI to the Patriots, Bitcoin is in the midst of a runup past $2,000, and our Corvette has accumulated more than 27,000 miles since the new coilovers and sway bars went on. We decided that after three years of daily driving, it was high time to get our suspension components rebuilt.
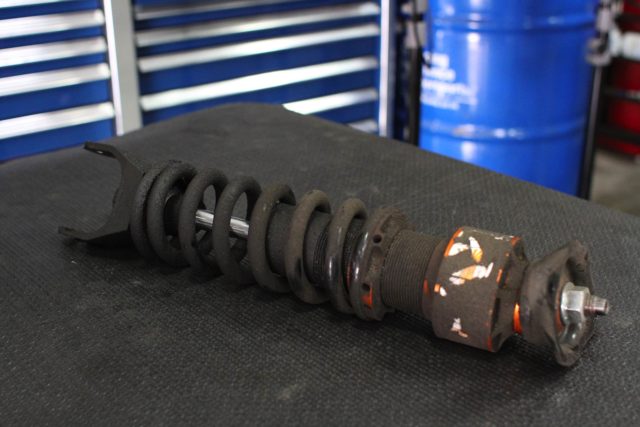
Here’s what a coilover looks like after three years of daily driver use and almost 30,000 miles (the transmission cooler leak didn’t help things either…) Fortunately, a factory rebuild will bring our set back to like-new condition.
Like any mechanical object, coilover dampers are subject to wear over time. Track days and grocery getting take their toll, and eventually they’ll lose the effectiveness they had when they were new. Unlike stock-style shocks or struts, however, decent coilover damper units can be rebuilt, rather than thrown out and replaced. A good set of coilovers is an investment, and periodic maintenance is the key to keeping everything working the way it was designed to.
A New Era
Another thing that’s changed over the last three years is that the technology developed by the original manufacturer of our coilovers, Pfadt Race Engineering, was acquired by Advanced FLOW Engineering, and today forms the core of the aFe CONTROL line of suspension components for BMW, late model Mustang, and Camaro/Corvette applications. They’ve continued to update and improve the designs, and manufacture dampers in a dedicated 11,000 square foot facility in southern California.
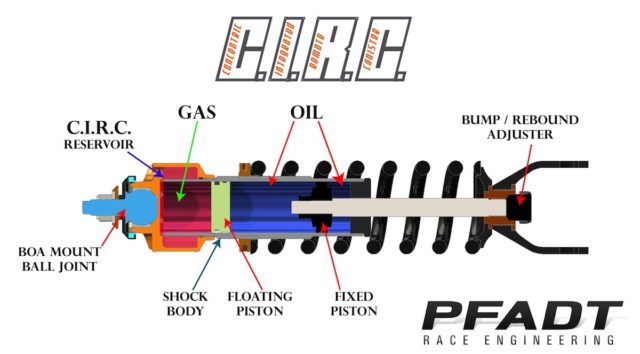
This cutaway illustration shows the internal components of the coilover dampers. Both the floating piston and the fixed piston have seals that are subject to wear over time, as well as the seal that surrounds the shaft.
So what actually suffers from wear in these components? Per aFe’s Ryan Takashima, “What usually wears out on a damper are the seals, and the fluid changes its viscosity.” Inside the body of the damper, there are two main moving parts with seals: the “fixed” piston, which is connected to the damper shaft and moves relative to the body, and the “floating” piston which serves to separate oil from the inert gas used to keep the damper internals under pressure. As the vehicle moves and the dampers extend and compress, these pistons are in constant motion, and over time the seals will wear, which can eventually lead to a leak.
The fluid itself can also “wear out” – just like engine oil, damper oil is constantly being sheared on a microscopic level, and over a long enough period the overall viscosity will start to drop. Because the damper does its job by passing this fluid through orifices calibrated to deliver a certain resistance to flow for a given oil thickness, as that thickness changes, so will the damping rate.
Another factor in the effective lifetime of the fluid is contamination from wear particles. “When the shock is constantly moving, it is micro-polishing the inside surfaces,” Takashima explains, “which then goes into the fluid.” You can think of this like the break-in process for a new engine – as the pistons move in their bores, the rings lap themselves into closer contact with the cylinder walls, and the microscopic material from the rings and bores ends up in the oil. Although this process is much more subtile inside a damper, it still occurs, and over many thousands of miles and countless racetrack laps, the once-pristine damper oil becomes thinner and contaminated with wear particles.
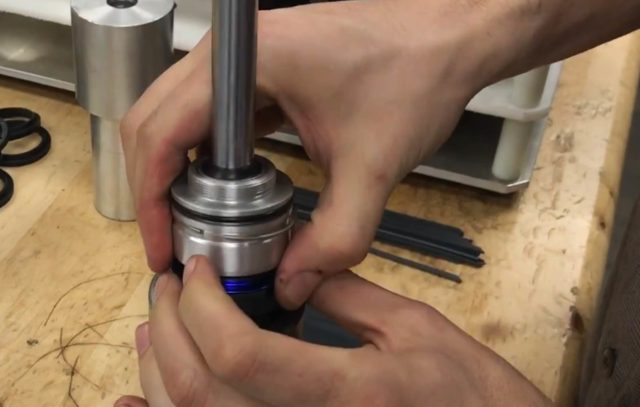
Although it’s obvious that seals will wear, the oil itself is subject to both viscosity breakdown and contamination from microscopic wear particles. A rebuild replaces both the seals and the fluid, restoring the unit to its original function.
Back to the Future
The solution to what ails aging coilover dampers is a rebuild, which basically comes down to, “Opening it up, cleaning it, and replacing the seals and the fluid,” per Takashima. The damper bodies are depressurized, the components are disassembled and cleaned, then inspected for unusual damage beyond the expected wear. The old seals are removed and replaced with new ones, the components are reassembled, and then the shock body is ready to be refilled.
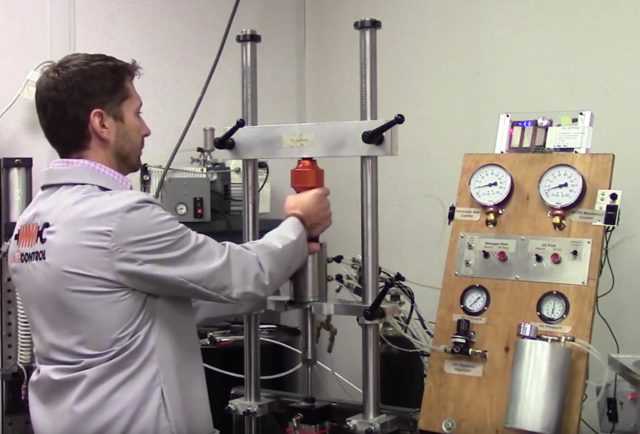
This custom rig is used to fill the rebuilt damper with oil, pressurize it with inert gas, then seal the whole assembly with a snap ring. Each application gets a different quantity of oil and amount of gas pressure – in this case, a C5 front damper is being filled.
This part of the process is where a bit of magic occurs – as we mentioned earlier, in addition to the damper oil, the shock body also is pressurized with inert gas, with the two separated by a floating piston. In order to get everything inside in the right places at the right pressure and then sealed, a special fill station is utilized. This piece of precision machinery is the main reason why rebuilding one of these coilovers isn’t a DIY project.
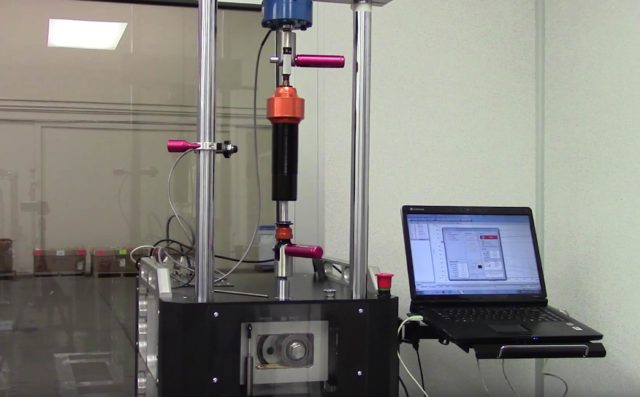
After the rebuild is complete, each damper gets tested twice on the shock dyno – the second test comes after a ‘quarantine’ period to make sure no gas or oil has leaked out. An infrared sensor on the left side of the test stand tracks the shock’s temperature as it is cycled.
Once everything is reassembled and filled, the damper is essentially as good as new, and it’s ready to head back to its home. How often will a coilover need to be serviced? Per Takashima, “For race applications, approximately once a season. For the street, the recommended interval is once every two years.”
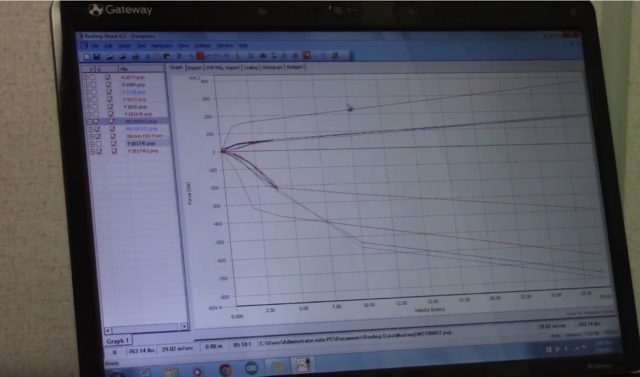
Shocks are tested at rates between one and thirty inches per second of compression and extension in order to make sure both the low and high speed valving is working correctly.
With our Featherlight dampers rebuilt and back on Project Y2k, we’ve restored the outstanding handling and precise adjustability we loved so much when they were first installed. If you’re considering a switch to a coilover suspension, keep in mind that aFe’s are designed to allow the components subject to wear to be replaced when needed. If you’re already coilover-equipped but have noticed your car doesn’t have quite the same spring in its step that it used to, do yourself a favor and get them brought back to life with a rebuild.