Automotive engineers spend thousands of hours on every new vehicle developing each component. Those components are then tested for reliability, performance, and durability in a number of ways. As enthusiasts we find ourselves replacing or upgrading many OEM parts on a regular basis, and often includes the suspension.
For vehicles that are garaged, rubbed with a diaper, and only taken out into the world under ideal conditions, longevity probably doesn’t come to mind often when considering which suspension parts to purchase. For those who own a car that lives in the real world however, the upgrade parts you install for the suspension need to be as reliable and durable as the OEM parts if not better.

After five years in the windy city, this Pontiac G8 returned to BMR headquarters to have its suspension components evaluated for wear and durability.
While the car was in ‘The Windy City,’ the suspension received no servicing or attention. Bushings were not lubricated, nothing was disassembled. Cleaning only occurred with what the rain could wash off, or the occasional trip through an automated car wash.
Last summer, after 60,000 miles of driving and five winters in Chicago, the car was brought back to BMR’s headquarters in Florida. Every suspension component was removed and inspected for wear, corrosion, and fatigue. The following is what BMR technicians found.
Rear Toe Rods And Trailing Arms
We talked with BMR’s Pete Epple about what the company found during the inspection process. “With all of BMR’s hard parts, the first thing we inspected was the quality of the powdercoat. After five Chicago winters these arms have seen lots of road salt and moisture, which will cause rust and corrosion to the metal if it is not protected. As you can see in the pictures, most of the parts still have a fair amount of salt, grease, and grime on them, but the powder-coating is perfectly intact and there is no rust or corrosion, with the exception of the grease fittings.”
Dirty but not destroyed, the rear suspension components on the Pontiac G8 held up to five years of poorly maintained roads and harsh Chicago winters.
The next step was disassembling the bushings and sleeves from the control arms and inspecting those parts. Epple says, “When they were pulled apart we looked for any cracks or splits in the bushings, cold flow, uneven wear, and wear and corrosion on the sleeves. The ID and OD of the bushings and OD of the sleeves were measured and compared to new versions of the same bushings and sleeves. While there was some wear in the bushings, they performed extremely well given that they were never greased after the initial installation, and had a fair amount of contamination.”
While the powder-coated parts looked fairly good, and the bushings were worn only within acceptable parameters, there was some corrosion damage on the bushing sleeves. “As contaminants found their way into the bushings, eventually the coating on the sleeves was worn away, leaving the exposed steel. As moisture and salt worked their way in, surface rust began to form on the sleeves, increasing the amount of debris in the bushings,” Epple says.
The good news is, this issue is easily avoidable, as greasing the bushings on a regular basis will flush out dirt and debris. – Pete Epple, BMR Suspension
As far as the inside of the front bushings are concerned, Epple says that there was some uneven wear within the bushing, but nothing that was concerning. He also says that while the bushings were greased during the past five years the spiral flute design of the bushings allowed them to retain some grease, even after 50,000 miles of driving. “Fresh lubrication would have cut down on the wear to both the bushing and the sleeve, but neither were close to being in a state of failure, and could still be used without any issues.”
Bushings and sleeves were checked for OD and ID wear. New parts are pictured left for comparison to the used parts pictured right.
Front Lower Control Arm Bushings and Radius Rod Bushings
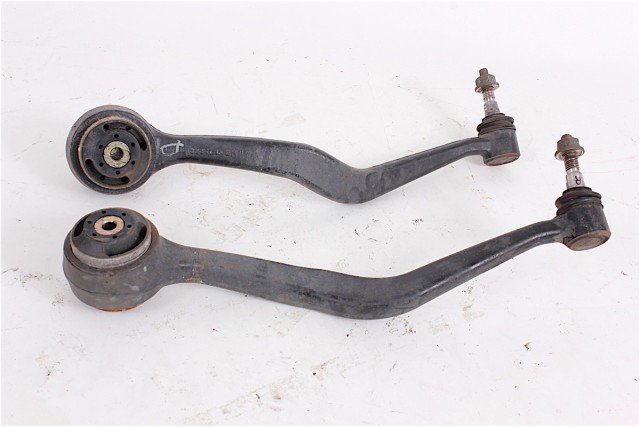
BMR pressed new bushings into the OEM font suspension components, which is what the company offers for Pontiac G8 front suspension.
For the front suspension upgrades on the G8, BMR installed new bushings to the OEM parts. These new bushings are made from Elastomer and pressed into the forged factory arms. “Elastomer is a more resilient material as it allows for great articulation, but is strong enough to handle very high compression loads. This makes it great for bushing that need to do both well,” Epple says.
The center sleeves held up very well to the harsh environment. The zinc coating is very much intact, and you can see the slight buildup of road salt on the outer lip of the sleeve, but it has not caused any corrosion. If the bushings were disassembled, cleaned, and re-greased, there would be no reason not to reuse them.
“The lower control arm bushings are a bonded design and the bushing, inner sleeve, and outer sleeve all press into the arm. One big benefit to this design is it keeps contaminated from getting into the bushings. While the bushings had some dirt on them and a tiny bit of surface rust on the outer sleeve, the bushing material was in great shape and showed no real signs of wear.
“The radius rod bushings are a split bushing design with a center sleeve. When we pulled the arms out the same surface rust we found on the lower control arm was present. We were surprised to find contamination in the bushings between the bushings and inner sleeves. This was a combination of dirt and grime from the road. The factory arms are designed without grease fitting. This negates the ability to pump fresh grease into the bushing to clear the debris and contaminants out. It is possible to drill and tap the arm and add grease fittings, but for the test we went with unmodified factory arms,“ says Epple.
With the exception of surface rust on the sleeves, and some rust transfer from the OEM arms, the bushings held up well. Bottom right photo: BMR has since updated its design for the Pontiac G8 with this new 95 durometer polyurethane bushing.
Epple says that with the exception of the contamination and some bulging caused by it, the front lower control arm bushings showed no signs of excessive wear. As for the radius arm bushings, “The center sleeves held up very well to the harsh environment. The zinc coating is very much intact, and you can see the slight buildup of road salt on the outer lip of the sleeve, but it has not caused any corrosion. If the bushings were disassembled, cleaned, and re-greased, there would be no reason not to reuse them.”
BMR has since updated the design of these front suspension. “These are internally fluted, 95 durometer polyurethane bushings with a zinc-coated inner sleeve that will stand up to the highest compression loads, while still articulating enough for great handling,” says Epple.
Sway Bars and End Links
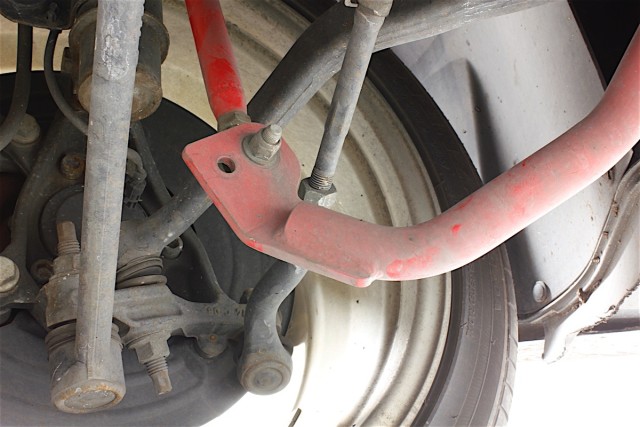
Swaybar and link still in-tact after 60,000 miles. We’ve seen OEM end links that failed at this point.
Sway bars take a lot of abuse. These components transfer extreme forces during turns to control body roll. Cracks in the pavement, bumps, hard cornering, all punish the sway bar and its end links. “This means the strength of the material is crucial. When we removed and inspected the bars we saw no sign of wear and no stress cracking, which can be a sign of a failure prior to it happening. The powdercoat was in great condition except for a few spots where the bar was rubbing the end links,” says Epple.
One OEM rear sway bar mount suffered a failure at some point during the last five years, but this had apparently gone unnoticed by the owner or anyone else who had worked on the car. “Strangely enough, the bar didn’t hit anything and made no noise. Looking at the remaining piece of the broken mount, it had been like that for some time. Unfortunately, the OEM design of the rear sway bar mounting tabs prevents us from using a larger, stronger mount,” Epple says.
BMR sway bar and end links after 60,000 miles and five years in Chicago. Bottom right: The OEM rear sway bar mount did not hold up so well.
Epple says the sway bar end links fared well also, even though BMR has since replaced this design with a different one. “When we pulled the end links off the car they were all in pretty good shape. All but one of the rod ends were still tight and not making any noise. One rod end on the front bar had begun to loosen up and if you shook the link aggressively it would make noise. There was some minor corrosion on most of the rod end housing from exposure to the salt and moisture, but much less than we were expecting.”
Rear Cradle and Differential Bushings
The rear cradle bushings and the differential bushings.
The rear cradle on the GM Zeta chassis that the G8 was built on is a notorious contributor to wheelhop. The OEM bushings feature large voids that are designed to reduce noise, vibration, and harshness (NVH). The compliance in these bushings that allows for the NVH reduction also allows for deflection and wheelhop. “When we removed the bushing inserts, we found a fair amount of road salt and grime, but no damage or wear on the bushings. We did find some rust transfer from the chassis on the body side of one of the large bushing inserts. This is due to the factory corrosion prevention not standing up to the harsh environment, and we only saw it on one bushing,” says Epple.
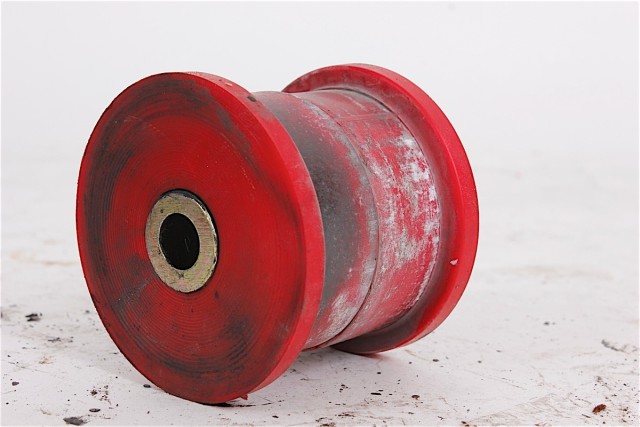
Differential bushing removed from the rear differential after five years and 60,000 miles of Chicago driving.
This was the torture test of all torture tests. The car was located more than 1,000 miles away, and we didn’t see it or touch the suspension for five years, and neither did anyone else.
Epple told us “This was the torture test of all torture tests. The car was located more than 1,000 miles away, and we didn’t see it or touch the suspension for five years, and neither did anyone else.”
We’d say that’s a fair assessment of the test and the results, and given the results we wouldn’t hesitate to run BMR products on any of our daily drivers.