Finishing an engine swap on a vehicle might be the last stop for some projects, but if you plan on adding a turbo system, it’s just the first act of the show. Your project vehicle might not have an off-the-shelf turbo system option, so that means you’ll have to put on the old thinking cap and build one.
Engine swaps are a great way to turn a rather pedestrian-feeling car into a real ripper, adding a turbo system just takes things to a new level. Our Project Swedish Meatball Volvo 940 wagon not only got an LS swap, but we decided to add a Summit Racing 76mm turbo for good measure. Since a 1994 940 Volvo didn’t come with a V8 or turbo system, some custom parts needed to be made. Rick Trunket from Big 3 Racing took the lead on fabricating the turbo system. We sat down with him Trunket to learn just want goes into building a turbo system for a vehicle that’s been engine swapped.
Space can disappear in a hurry when you're engine swapping a project car. If you plan on adding a turbo kit, you need to have the engine in place so you can start to come up with a plan.
You Need To Have A Plan
Before you cut any tube or fire up the welder, you need to study your subject and come up with a plan for the turbo kit. Depending on your build, there could be HVAC systems, cooling system components, or other critical vehicle systems that need to be accounted for. You also need to think about what kind of exhaust you want to run, because that’s going to impact where the turbo is placed.
“When I start planning a turbo kit, I think of doing the best I possibly can within the space that I’ve been given, meaning someone has to work on this car at some point. You need to think about how the spark plugs can be changed, how the valve covers will be removed, and where there are parts that can’t be exposed to a lot of heat. You have to think beyond the fabrication and really consider the maintenance side of things,” Trunket says.
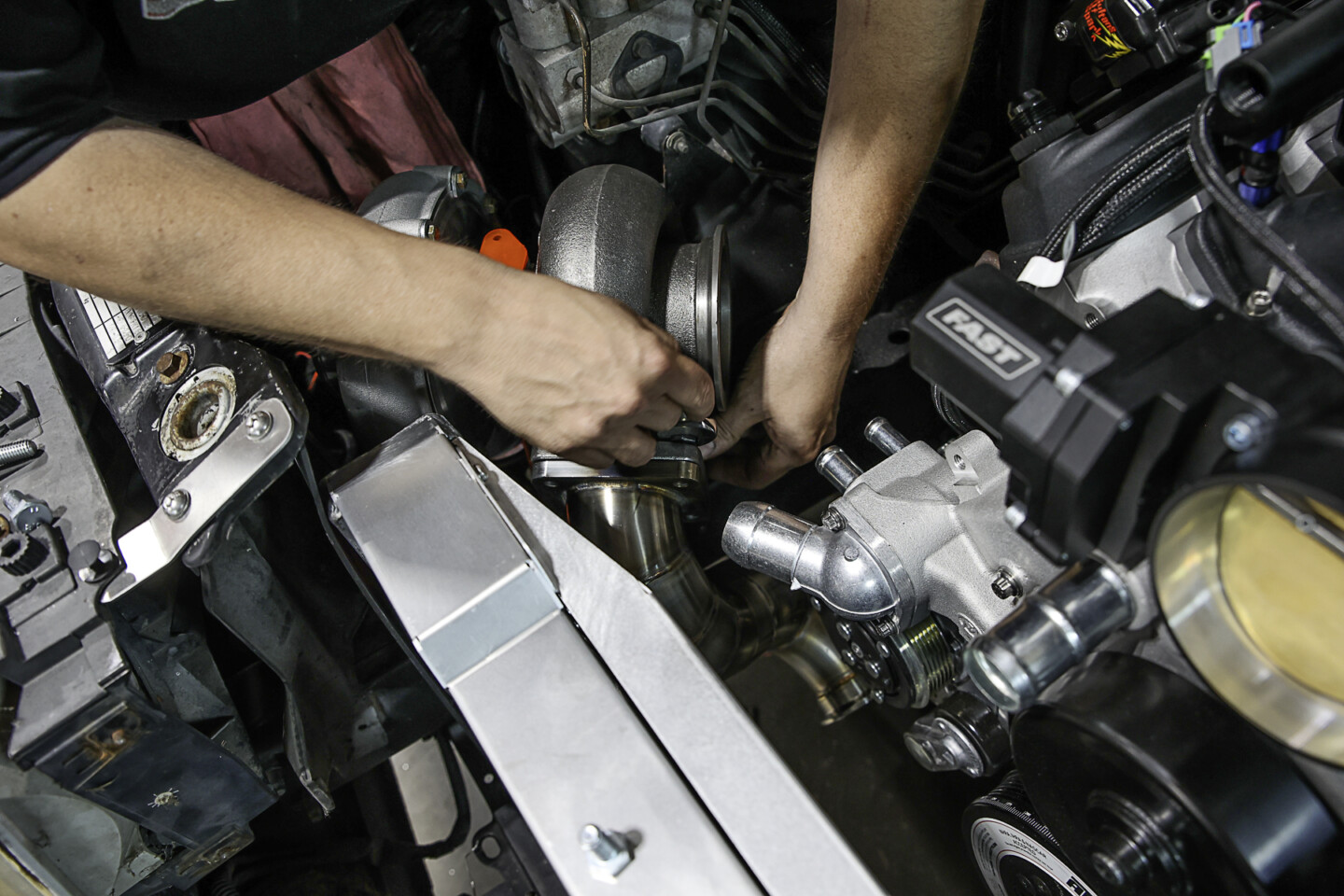
You need to put the turbo in a spot where it won’t cook anything important. You’ll also need to factor in where the hot side, cold side, and exhaust will need to run.
You don’t want to underestimate how much heat a turbo system can generate, especially if the car is going to be street-driven a lot. Keeping the turbo and other hot side parts away from the brake master cylinder is important because you don’t want to boil your brake fluid. You’ll also want to avoid putting any hot side parts near sensors or other electronics if possible, because those parts really don’t like heat.
A big part of your plan should be turbo placement. The turbo is the star of the show, therefore it needs the best seat in the engine bay so it can do its job. That can be a challenge due to where everything else is situated. You need to account for where the charge pipe is going to be and where the exhaust will need to exit.
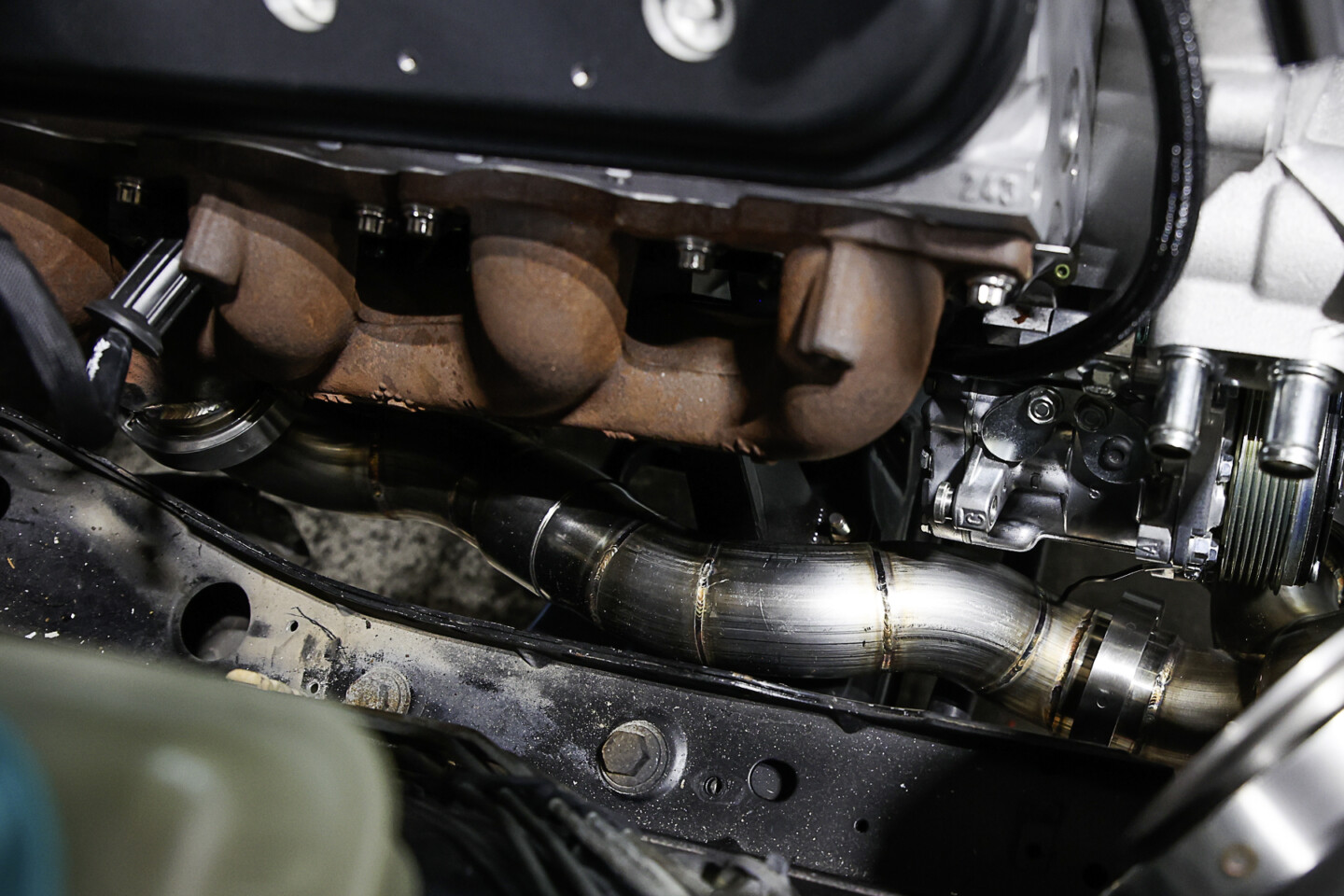
Your hot side piping doesn’t need to be huge, it just needs to match how much air your engine and turbo can move.
“All of your pre-turbo tube doesn’t have to be huge, it could be relatively small and still work just fine because that is not the restriction. A good example is the kit I built for my small block Mopar engine in my Duster that makes 2,300 horsepower. I used an inch and three-quarter header tube going to a 2.5-inch collector and a 2.5-inch tube for the turbo. The turbo spools great and isn’t lazy. So, using larger tubing doesn’t really do anything but take longer to fill up, and it might even cause the turbo to spool slower,” Trunket says.
The size of the pipe for your hot side will really come down to your specific application. You’ll want to speak with the turbo manufacturer and your engine builder to get an idea of what size pipe will work the best. Just like with cylinder heads, bigger isn’t always better for the hot side and it needs to match what your engine and turbo can do.
Turbo Systems For Engine Swap Applications
A project car that’s undergone an engine swap could make your turbo system a little more complex than a typical build. Let’s use Project Swedish Meatball as an example again. Since the Volvo never came with a V8, the entire packaging of the engine bay is now different. The engine is bigger, the accessories are in a different place, and the wiring will all have to be moved. That means Trunket had to create the whole turbo system from scratch.
“I like to have the engine in the car and as much of the car together as possible. You want to build the turbo kit around what’s there and can’t be moved, you don’t want to build the car around the turbo kit. If you don’t have everything on the engine and other items in place, you’re opening yourself up to problems after the kit is finished and everything is assembled. So, it’s really important to have, we’ll call all the immovable stuff kind of in place to make sure you, you’ve got eyes on that and it’s accounted for.,” Trunket says.
The more parts you can have in place, the easier it will be to fabricate a functional turbo system that won't cause maintenance issues.
When the planning is done and it’s time to start cutting tubes and melting metal, you need to take a hands-on approach to deciding where everything will go. That means you’ll be doing a lot of crawling around the engine bay, test fitting, changing configurations, and constantly working the problem to get the right fit for your kit.
“I will visualize how I think something should go and then start shoving pipe in places to see if it will fit how I thought it should. My little rule of thumb is if I can get my hand and finger in between it and the object I’m close to, that’s, that’s good enough. I’ll stick different bends and lengths of tubing into the spot I’m working in when I’m building a kit. I do this to see how things will fit and what needs to be changed as I’m working on fabricating the turbo system. Doing this gives me a better idea of how things will fit and eliminates the need to just guess, weld, and redo something,” Trunket states.
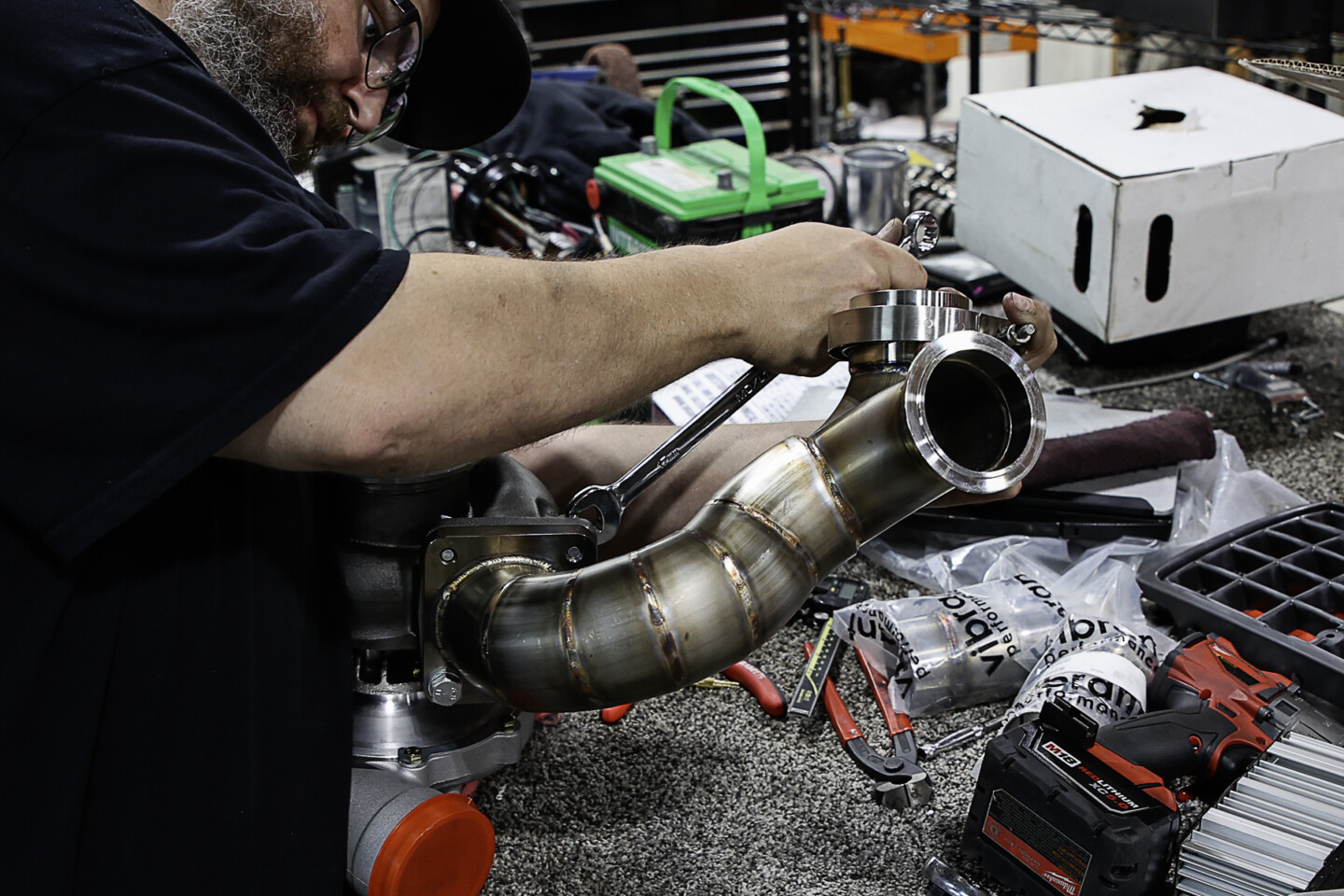
Test fitting parts and making changes as needed is the most important think you can do when fabricating a turbo system.
One point that Trunket wanted to drive home is not to be lazy when you’re building a turbo kit for an engine-swapped project. If you start doing things to just save time or avoid an issue to save time, you’re going to create other problems you won’t discover until later.
“You might have to make something two pieces instead of one to get it to fit correctly. Will it take more time, yes, but it’s going to save you time in the long run. You might have to make a custom steering shaft, or notch a frame rail to get the turbo kit to fit right and avoid making the car a maintenance nightmare. It’s just way easier to make those changes at the beginning of the build, rather than discover they’re causing an issue after the rest of the kit is done,” Trunket explains.
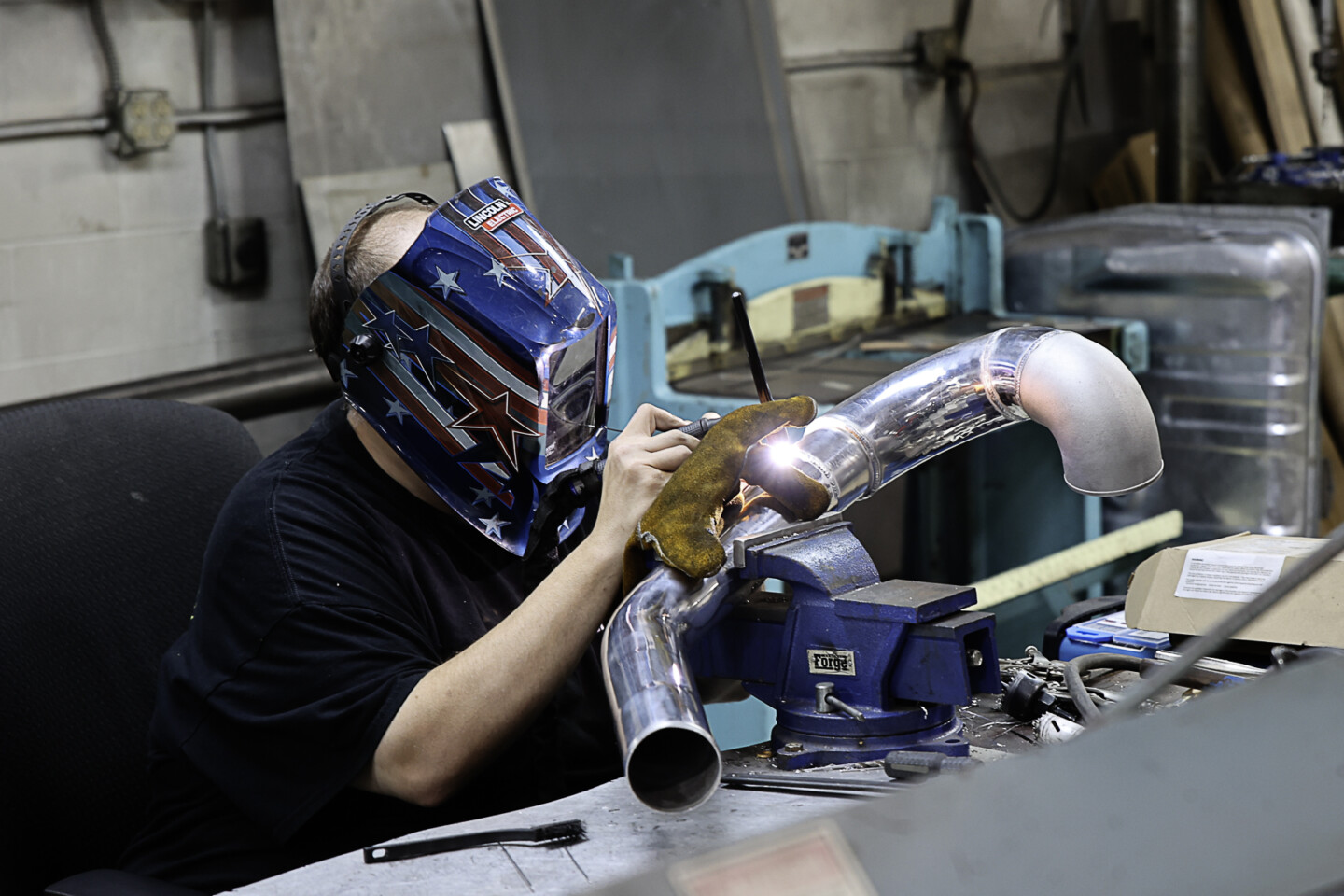
You want to have some wiggle room to make changes as the fabrication process continues. Once you’re happy with how something fits, then it’s time to finish welding parts together.
How you weld everything together is important during the final phase of the fabrication process. You still want to have the ability to make changes on the fly and move parts around to get the best fit possible.
“ I might tack three or four pieces, weld it, go fit it, tack it more three or more four pieces and go and then on my final weld. I’ll weld everything together except for maybe just a vband flange or the end piece of the clamp. I’ll get everything assembled that I can and do my final welding of parts on the car if possible. This helps ensure the parts are going to fit properly in their final positions,” Trunket says.
Where there’s an angle grinder and welder, there’s a way to add boost to any vehicle. You just need to make sure you spend enough time coming up with a plan for your turbo kit before you start the process. When you take your time and build a well-thought-out kit, the final result is a turbo system that functions great and doesn’t make the vehicle a nightmare to work on.