Unrivaled performance potential and an often staggeringly-high price — these are the two attributes most commonly associated with ceramic bearings, and in a lot of ways, both of those points are entirely correct. Regarded as a superior alternative to steel ball bearings, ceramic bearings have been used in everything from mega-dollar Formula 1 engines to skateboard wheels and everything in between. While they do come at a price premium, for those that seek the ultimate in performance, they’re an investment with tangible rewards.
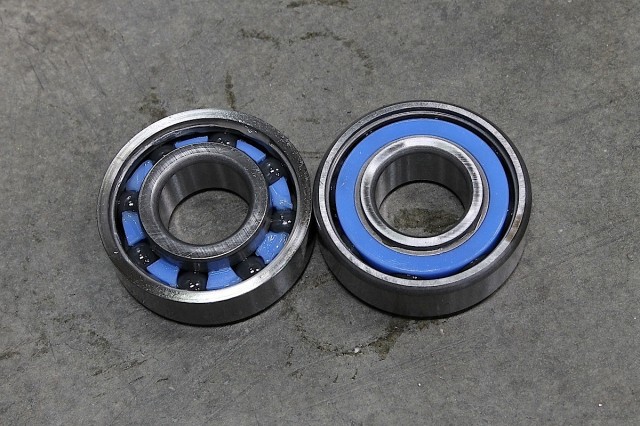
Ceramic bearings are known throughout the industry for their incredible performance – but it’s their heat-resistant properties and their unrivaled strength and durability that make them a tangible upgrade for any piece of rolling machinery.
Among the pioneers of ceramic bearing technology in auto racing has been Arizona-based Performance Bearing and its founder, Jack Wilson. Wilson, a veteran racer in his own right and an engineer and journeyman machinist by trade, has spent years working to cure the ills of friction exemplified by steel bearings. And although his innovations have taken him through virtually every industry one could imagine, racing is still his lifeblood, and today, through the company he founded in 2002, a wide range of ceramic bearing offerings are available for racers of all walks.
While rebuilding our Project BlownZ Camaro in the off season, we rang up Performance Bearing and swapped some of the steel bearings in key areas of the race car with ceramics in hopes of boosting our overall performance and longevity. But beyond simply installing Wilson’s product in our race car, we wanted to know more about this bearing technology and what it has to offer in terms of performance on the race track. And as it turns out, ceramic bearings have even more pluses than you probably thought they did.
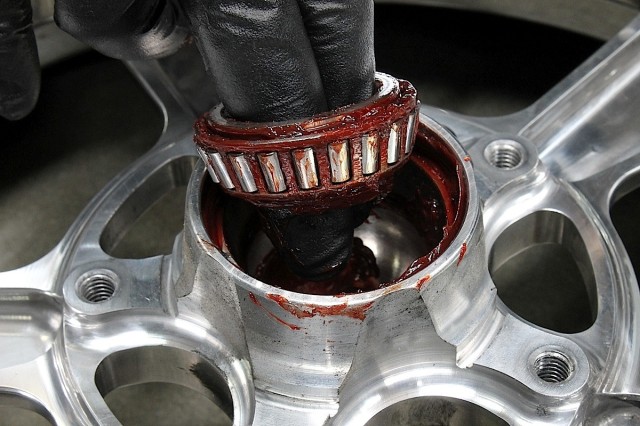
Over the winter, we equipped BlownZ with ceramic bearings in four key areas: the front wheels, the rear axles, the carrier, and the pinion. In the front wheels, we’ll be replacing these fairly standard angular roller-style bearings with hybrid Conrad-style ball bearings.
Ceramic Bearing 101
As it pertains to the automotive industry, the most common form of ceramic bearings are what’s known as a ‘hybrid’ bearing. Such a design incorporates steel races like those used on typical steel ball bearings, but they feature balls made of varying forms of ceramic material. Performance Bearing utilizes 52100 chrome-steel bearing material for their races, and balls made of solid silicon nitride ceramic.
Such a type of ceramic material is, beyond just the offerings from Performance Bearing, rather common in the manufacture of hybrid bearings, as they deliver excellent shock resistance when compared to other forms of ceramics. Silicon nitride ball bearings are also harder, more temperature and corrosion resistant, and lighter than steel (all points we’ll explain in closer detail in a moment), and in an ode to their capability, were used exclusively in the main engines on NASA’s Space Shuttles.
Performance Bearing currently manufactures ceramic hybrids for use in the front wheels, rear axles, transmissions, and differentials of high performance racing vehicles — all key areas of rolling resistance. But as Wilson tells us, ceramics have advantages in any area of a race car — it all just comes down to cost and research and development.
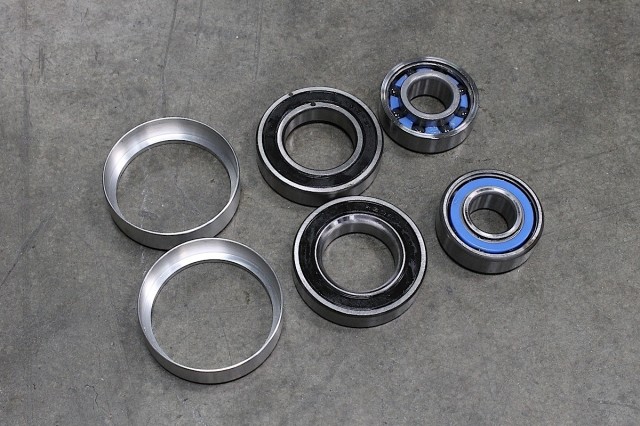
Here’s the ceramic Conrad bearings from Performance Bearing that we’ll be replacing the roller-style bearings with in the front wheels. As you can see, these aren’t angular, but are your more common ball bearing with an inner and outer race, and use a steel “cup” that hold them in place in the wheel. The Conrad-style bearing, named afters its inventor, Robert Conrad, features a “trough” on the inner and outer race that separates the balls.
Ceramic Advantages
With most things in life, there are tradeoffs — advantages and disadvantages that must be weighed. But in the case of ceramic bearings, it’s really more like a landslide in favor of the advantages, and when you get right down to it, the only downside is the up-front cost. But the positives — they’re aplenty.
First, ceramics are much lighter than their steel counterparts. As much as 50-75% lighter. According to Wilson, the silicon nitride balls weight 60% less than equally-sized steel ball bearings, meaning there’s even less weight spinning inside the races. Secondly, and perhaps most impressively in our eyes, ceramics are incredibly strong.
“In a ball form, ceramics is ultimately stronger than steel. If we made it long like a piece of spaghetti, it would in fact be just as fragile as a piece of uncooked spaghetti. But as a ball, it’s strong enough that if we were to lay out a rag and put a ball in the middle of it, we could beat it into concrete with a sledgehammer and nothing will happen to it. They’re unbelievably strong — it’s just phenomenal.”
…as a ball, it’s strong enough that if we were to lay out a rag and put a ball in the middle of it, we could beat it into concrete with a sledgehammer and nothing will happen to it. – Jack Wilson
Another point in favor of ceramics is their resistant to heat. According to Wilson, steel balls tend to begin displaying integrity issues around 400 degree Celsius, while ceramics can easily operate at 2,000 degrees or more.
But the one attribute that ceramic bearings are most known for is their greatly reduced friction versus steel bearings made of any form of steel. How much better are they, you ask? Wilson puts it at about 1/10 of the overall friction. That means your wheels and other components can roll and roll all day.
All of this adds up to a form of bearing that not only performs better, but also lasts much, much longer. Some estimates in our research put it at five to ten times longer, although the actual useful life can depend on who you’re asking or what you’re doing with the bearings.
Why Do Ceramics Have Less Friction?
What Is Silicon Nitride?
Silicon nitride is a chemical compound that combines silicon and nitrogen into a solid with a very high melting-point that’s not chemical inert (meaning it’s not chemically reactive). Silicon nitride (or Si3N4) is used in both full ceramic and ceramic hybrid bearings for applications with high loads, high speeds, and extreme temperatures, and is also considered useful in applications where corrosion, electric, or magnetic fields disallow the use of metals. The material was first utilized as a performance-style bearing in 1972, but didn’t go into mass-scale production until 1990.
To start, ceramic balls do not corrode, nor do they cold weld — which is the process whereby forms of metals can wear through the adhesion of sliding surfaces (this process is also known as “galling”). In cold welding, or galling, the constant friction between the steel balls and the steel races results in a distinct gouging or scratching of the materials, which effectively transfers said materials from one surface and leaves it stuck to the other. What you end up with are uneven and rough surfaces that effect performance. This in itself is an advantage of ceramics, but because they don’t corrode or cold weld, they also don’t require viscous oil or grease for operation that would further effect their level of friction.
Incorporating all of the advantages we discussed above into one, we arrive at what makes ceramics perform the way they do. Because of their lower density, their thermal expansion properties, and the reduced friction they undergo, they sap away less rolling energy in total. In the case of our Project BlownZ Camaro, the difference in rolling resistance has been significant, and can be felt just in pushing the race car though the staging lanes or around the shop, where it will roll with impressive freedom — so one can just imagine how this plays out on the race track when under power.

We also used installed ceramic hybrids in the rear carrier and the pinion, as well as the axles (of which the bearings are shown here). The carrier and pinion both use what’s known as an angular contact bearing, and this is due in part to the need for additional axial thrust on the bearing itself during operation. Unlike the Conrad-style bearing, this type of bearing doesn’t have a trough, but rather, has a ‘shelf’ on one side the balls ride on that, because of its design, lends itself to greater axial load.
Ceramics In Engines
You may also be wondering why ceramics aren’t more prevalent in engines — although they are used extensively in Formula One, where cost is no object — and Wilson says he gets calls on this very subject every day.
Truth is, he says, “There’s really no place at the current time for ceramics internally in a motor with this particular type of application.”
Wilson has worked on a number of projects in the past, particularly with camshafts and crankshafts. In doing so, he’s developed needle and ball bearings for cranks, and has flirted with the idea of cams that have an outer race and ceramic balls, but no inner race. In the case of crankshafts, more of a needle bearing-type design with multiple rows of balls would potentially be used, he says, to help distribute the added load.
Wilson also experimented with ceramic tips on three-piece pushrods that are used in nitro, Top Alcohol, and Pro Stock engines. Interestingly, Wilson shared that one particular Pro Stock team found a six horsepower gain by using them, but ran into longevity issues due to the design.
Here's the Conrad-style bearing being pressed onto the axle shafts.
“We’ll definitely see more of this one day…it will just take someone with money,” says Wilson. “There are tons of places that ceramics can be used, people just don’t think outside the box to make it work.”
As Wilson goes on to say, “Other than the cost, there really is no downside to ceramic and hybrid ceramics bearings.”
Now, we bet you didn’t have any idea just how advantageous ceramics bearings were prior to reading this, did you? Well, as surprising as it may seem, ceramic bearings are one of the most tangible upgrades one can make, whether it’s your race car or your street car (Wilson tells us tests have proven a several mile-per-gallon increase on passenger cars), there’s a lot of resistance at work that can be remedied through ceramic technology, and as that technology evolves, it will become both more prevalent and more affordable. For now, though, it’s a luxury for but the most performance-driven of racing vehicles.