It’s certainly not a steadfast rule by any means, but the general thought process is that the more power you’re making and the quicker and faster your vehicle is, the more tire you’re going to need to get the job done. The small-tire movement has, of course, proven that one can do a lot with a little when it comes to the width of a tire, but at some point in the transformation of a vehicle from a street car to a track machine, the need for wheel tubs is going to come into the equation if you’re even halfway serious about racing.
True, the majority of the popular late model, rear wheel drive production performance cars out there can adequately contain a 28-inch tall tire, up to 12 inches in width (give or take a little), such as a 275 or 315 radial, in the stock wheel wells. Though, as you begin to factor in tire growth, or as you make plans to reduce the ride height somewhere in the evolution of the vehicle, the limits of those stock wells quickly become apparent. And that’s when you know it’s time for a true set of aftermarket wheel tubs.
TMRC offers a range of composite tub options in standard and lightweight versions, to fit a range of tire sizes from radials and 10.5-inch slicks on up to the big 36-inch meats used in Pro Modified.
Any quality chassis shop around the country can set your vehicle up with a set of wheel tubs, either fabricated in-house or constructed by aftermarket manufactures like Tim McAmis Performance Parts, who we’ve teamed up with to educate on the in’s and out’s of wheel tubs, including sizing and installation tips, and a explanation on why lightweight carbon fiber tubs are a distinct advantage to the racer. In doing so, we’ll be using our own Project BlownZ Street Outlaw Camaro at the testbed, which has undergone some significant off season changes under the watchful eye of the talented team at PMR Race Cars in Rancho Cucamonga, Calif. In addition to a complete 25.3 chassis build (which well be highlighting in great detail in an upcoming feature article), the PMR team has also installed and heavily documented the wheel tub installation in the car.
Tubbing With TMRC
The team at Tim McAmis Race Cars produces a range of carbon fiber wheel tubs through their own in-house Velocity Composites division, which are destined not only for the cars that they’re commissioned to build from the ground-up at their Missouri facility, but for mail order projects through the Performance Parts branch. As we shared with you during the build-up of Brian Hard’s Pro Nitrous Camaro last year, Velocity Composites is a completely internal operation that allows the TMRC team to produce carbon fiber and fiberglass components in tandem with their race car builds, as well as any number of custom, one-off pieces.

TMRC’s massive 47-inch lightweight tubs inside the Pro Nitrous entry of Brian and Tyler Hard, designed for the big 36-inch slicks.
Much as they do with their complete Pro Modified bodies and other trim components, the wheel tubs begin as a rolled sheet of carbon fiber material that’s cut on an automated CNC cutting table using individual files that have been developed by the engineering staff. The carbon fiber is molded into shape, the epoxy applied, and a vacuum process carried out that removes atmospheric pressure to compress the carbon fibers to create to a tightly compressed, lightweight part. The tubs, like all of their composite parts, are individually laid by hand, resulting in a part that truly has a hands-on degree of quality.
Tim McAmis Performance Parts offers several composite tub options, including a 34-inch version for radial tire and small slick-tire cars (this is the tub we’ve used on BlownZ), a 40-inch model for Outlaw 10.5/10.5W-equipped cars, 44-inch for cars running a 34.5-36-inch tire, and a large 47-inch tub for the big 34.5-36-inch tires that are used in all of the Pro Modified and Top Sportsman chassis builds. The tubs are all made from fire retardant resin, and feature a Cormat Liner to protect the exterior finish.
Weighing In Carbon Tubs
When it comes to carbon fiber wheel tubs, the advantages lie more in the looks, the longterm structural integrity, and the ease of installation, mores than weight, which many would assume as the primary reason that top-level race teams use them. Aluminum tubs are typically lighter than their composite counterparts, and in the case of TMRC’s tubs, that’s partly due to the pretense of a protective liner inside the tub. TMRC’s 34-inch tub weighs an estimated 9 lbs., the 40-inch 8.5 lbs., the 44-inch 9 lbs., the 47-inch 10 lbs., and the lightweight 47-inch 7.5 lbs.
In addition to the size of the tub, there’s also the option of a standard carbon tub that’s comprised of a carbon fiber and fiberglass lay up, and a lightweight carbon that’s pure carbon and weighs roughly half of what the standard tub does, size for size.
Composite Versus Aluminum, One-Piece versus Two
For budget-minded weekend warrior racers, who comprise the majority of the competitors out there, aluminum tubs have and continue to be the go-to choice for their vehicles, due to the lower cost of fabricating or having a local chassis shop like PMR fabricate aluminum. But as Johnston tells us, despite the higher cost, there are some very distinct advantages to the use of carbon fiber that should be considered.
“Aluminum wheel tubs are made of thin aluminum which tends to show imperfections and dents from rocks being shot up into them during a burnout,” says TMRC’s Billy Johnston. “With our carbon tubs, they’re made with a liner on the underside so that it protects the top (the show side) of the carbon and gives it that extra layer of strength. The cost on a set of carbon tubs is definitely going to be higher than a set of aluminum tubs but you can’t compare when it comes to the show quality.”
As well, aluminum and carbon tubs are constructed in a much different manner, which is evident in the installation process. You see, aluminum tubs, as Johnston explained to us, begin as a flat sheet of aluminum that has to be curved into its shape, then cut to fit inside of the wheel wells, and matched with the inner panels panels as a separate piece. The carbon tubs, on the other hand, are formed as a single assembly and shipped out to the customer already contoured for the tire size that’s being used. To that end, because the carbon fiber is very flexible at the outside corners, they can be folded up just enough to cram them inside the quarter panel, at which point they’ll bounce back into shape. This, as you can imagine, makes for a much easier installation process, whether its an experienced chassis shop like PMR doing the work or a DIY project.
In Pro Modified and Top Sportsman-style cars, a one-piece tub is by far the most common, as Johnston shared with us, with the main advantage to a one-piece being the absence of a raised area or seam line where the round tub and the inner panels bond together or meet.
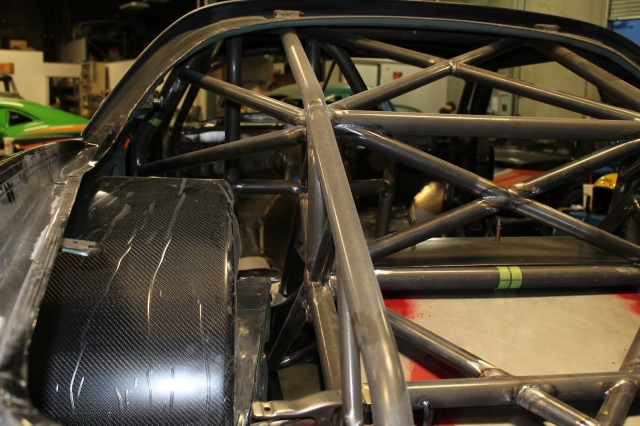
Our 34-inch tubs are the smallest composite tubs that TMRC produces, designed for the 275 and 315 drag radial tires and comparably-sized slicks, and measure 28-ninches wide as-shipped, making them much narrower once you cut them to size.
Determining The Right Fit
As you might have guessed, sizing the proper tub for your vehicle is a matter of what tire you’re going to be utilizing and the top-end growth of said tire. As we pointed out earlier, it’s the growth of the tire at speed that can cause contact concerns with OEM wheel wells, and its something you want to be certain to avoid as you move to aftermarket tubs by giving yourself ample room under the fenders. Information regarding the measured tire height and growth can typically be acquired from tire manufacturers to help you determine the right fit.
As Johnston tells us, “It’s always better to have a little bit more material than you need than not enough. The 34-inch, 40-inch, and 44-inch tubs are 28-inches wide and the 47-inch tubs are 27-inches wide. We always use the rule of thumb that if you think you’re going to go with a bigger tire in the future, you should order the tubs around your maximum application you may end up running so that someone doesn’t have to remount a new set in a year when they want to go bigger and faster.”
It’s always better to have a little bit more material than you need than not enough. We always use the rule of thumb that if you think you’re going to go with a bigger tire in the future. – Billy Johnston
A point to keep mind in this measurement process is that radial tires require a different approach due to the fact that they only grow a very minimal amount, whereas slicks are always going to grow in height with speed. This all comes back to finding out the exact measurements beforehand, but if you think you may run radials and slicks, that will need to be taken into account.
The width of the tire and the rear end are less important in the selection of tub size, as Johnston explains, because they’ve designed the mold for the tubs with ample lateral material so they can be cut down to size to fit between the framerails and the inner side of the quarter panel, making them capable of being custom-fit to virtually any application.
TMRC has a specific installed height for the tubs when they mount them inside of a car built at their shop. Essentially, they ensure that the height of the tire under squat pressure will clear the quarter panel and that the maximum growth of the tire will clear all points inside the tub, meaning the tire doesn’t strike the quarter panel, the inner panel, or any point in the rounded circumference of the tub.
Wheel Tub How-To
The process of installing wheel tubs into the car begins with mocking things up with cardboard, creating a 'mold' from which you can then transfer to the actual tub.
Before any saws are taken to your shiny new wheel tubs to cut them down to size — regardless of any measurements you’ve already taken — the first step in the process of installing the tub is mocking them up, and this is done utilizing some pretty high tech equipment. And by high tech, we mean your standard-issue cardboard.
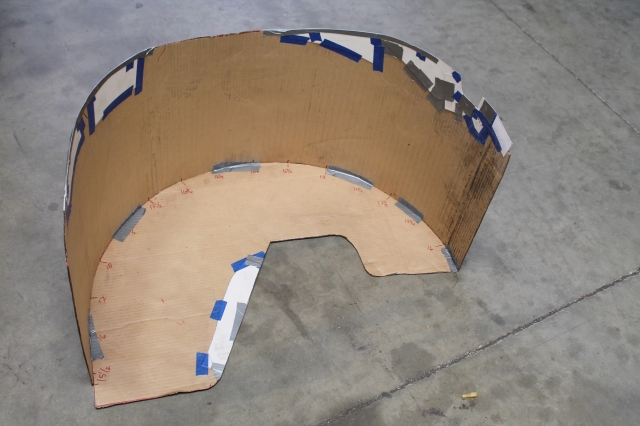
Here’s the finished product after cutting and trimming to match the contour of the framerail, the front and rear mounting points, and the inner sir of the quarter panel.
“The easiest way to install a set of carbon tubs is to fab a mock-up tub out of cardboard, make sure all your mounting locations and gaps are set, and then trace this mock up tub onto the carbon tub. From there, you can trim the rub down and install them,” says Johnston.
“Some people use adhesive or glue to attach the tubs up inside the inner quarter panel, but here at TMRC we go that extra mile and seal the tubs to the quarters with carbon and glass to that there is no way the tubs will shift or come lose and get into the tire on the top end when it grows.,” Johnston continued.
The team at PMR utilizes this very method for mocking up the tubs before doing anything with the actual tubs, by creating what is essentially a full tub out of cardboard, using the exact dimensions of the tub, and cutting it to fit along the framerail and the quarter panel. The team then laid the cardboard cutout over the tub and traced along the edges to give them a cut line.
The mounting points for a wheel tub will differ depending on the layout of your particular chassis, whether it’s a full-tube chassis, or has the stock framerails or a combination of stock framerails and a round-tube parallel rail (as we have in our Camaro), but the tubs are generally hard-mounted on the inner side, and are then mounted as part of the aluminum tin work structure at the fore and aft point of the tub, using rivets, screws, bolts, or some combination of these. In a round-tube car, the tub can be riveted directly to the rear tree of the chassis above the rear end housing, whereas in our case, they’ve been riveted to the stock square-tube framerails — something made possible in our F-body car only because we had the stock framerail removed and straightened, providing a flat surface to place the tubs against.
From our cardboard 'mold' we could then cut into the carbon fiber, which gets us in the ballpark. From here, some minor trimming may be necessary to create a perfect fit in the car.
The McAmis team mounts the rear edge of their tubs to what they call the rear tub filler, a carbon or aluminum panel that spans from the wheel tubs back to the rear bumper, using stainless steel button head screws. The front edge is then mounted to the upper 4-link crossmember pipe using rivets.

This angle shows the placement of the inner ‘panel’ of the tubs in position along the stock framerail. Rivets were used (and are commonly used by most chassis shops) to fasten the tub to the chassis here.
The tubs are secured to the car by riveting them to the aluminum tin work just behind the seat at the front and to the rear 'tub filler' at the rear.
The outer (quarter panel) side of the tub is where some extra time is needed to finish off the installation with a nice, precise degree of quality. Of course, riveting the tub to the inside of the quarter panel itself isn’t a good idea for a number of reasons that should be obvious, but nor do you want to simply let the tub free-float, as even the smallest of gaps would allow burnout smoke to permeate into the cockpit and could create a vibration point.
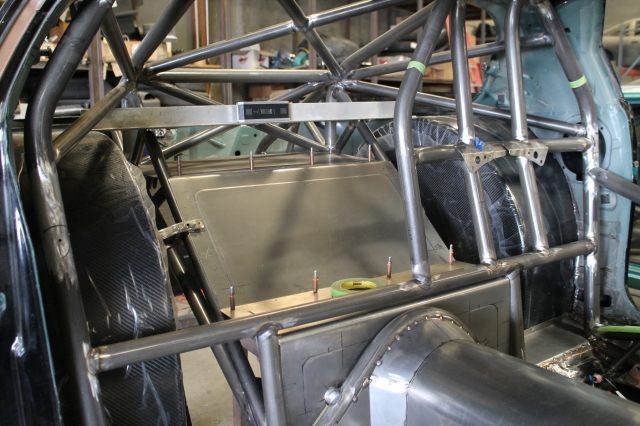
Simply eyeballing the location of the tubs isn’t enough to ensure they’re even from side to side. In addition to taking measurements along the chassis and body, the PMR team also used a level to check the position of the tubs relative to one another.
What chassis shops, including Tim McAmis Race Cars and PMR Race Cars do, is utilize a form of sealant or even carbon fiber lay up to secure the tub to the quarter panel — be they steel or composite — without any air gaps.
“We bond the tubs to the body from the underneath side with a thick layer of carbon and fiberglass to adhere the two together, and from the top side through the deck lid or the rear window it just looks as if the tubs are butted up against the quarters with no gaps and no seam lines,” says Johnston.
Beyond some upgrades in the drivetrain department and perhaps adding a roll cage, moving to aftermarket wheel tubs is near the top of the list for most enthusiasts looking to transform their street drivers into competitive machines, and for those building ground-up race cars, they’re purely a given. As we’ve illustrated here, with the help of Billy Johnston and the gang at Tim McAmis Race Cars, there are some honest advantages to carbon fiber wheel tubs, despite their cost premium — advantages that will pay off during construction and years down the road.
Not only has TMRC delivered an exceptional set of tubs that look great, but the PMR did a masterful job in installing them, with precision fit and finish inside the car.
Here's the nearly finished product, fit and finished up inside the quarter panel. Once hard-mounted to the chassis and tin work at the inner and fore aft positions, the PMR team used a sealant to semi-permanently bond the tubs to the quarter panel.