With the Big Three locked in battle on multiple fronts in the NHRA over the past few years, there has been a lot of very cool innovation coming off of the OEM production lines, all in the name of factory performance. GM’s factory racecars fly under the legendary COPO nameplate, and come with a variety of powerplant options, all of which do the name proud.
With three options in their lineup, Chevrolet Performance is catering to a variety of enthusiasts with its engine selections for 2019. We brought you an article earlier in the year with someone pushing the direct-injected 302 cubic-inch LT1 based engine combination. The naturally aspirated 427-cube LSX offering is a throwback to the original 427 COPO offering, and is available with a vintage dress kit, to make the LSX engine look more like a traditional small-block Chevy.
However, the third option for the 2019 COPO Camaro is the one that is the focus of this article. A supercharged 350 cubic-inch offering, the engine is aimed directly at NHRA Stock Eliminator competition. While a supercharged 350 isn’t new to the modern COPO lineup in and of itself, what is new is the fact that for this model-year, they have gone to a new supercharger unit, which is smaller than in years past, and they appear to be getting more performance from it.
“We have a drag racing coordinator, Roger Allen, who is responsible for all of GM’s drag racing efforts, and we sit down with him along with the marketing team every year and talk about what to offer for COPO,” explains Tom Wysocki, COPO Engine Project Lead for GM. “The Whipple supercharger [used on the previous supercharged 350] is strictly an aftermarket part. The intent of Stock Eliminator is to try and tie it into production as much as we can. The 6.2-liter LT5 Corvette uses an Eaton rotor set, which is what’s used in the Magnus0n supercharger [on the 2019 supercharged 350], so that is a definite tie in to production, and we wanted to have closer ties to what we sell.”
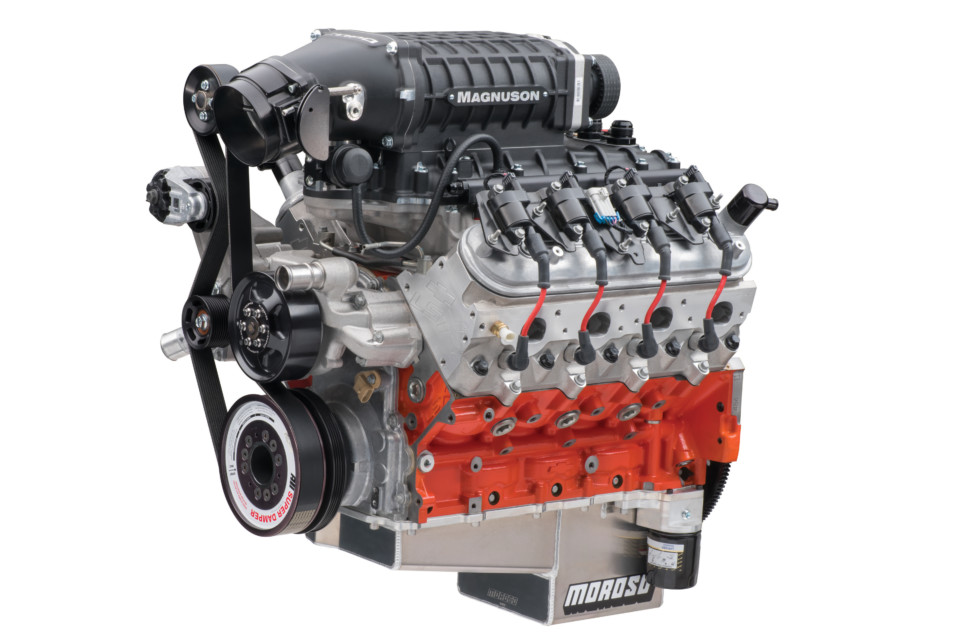
The COPO supercharged 350 powerplant has been redesigned for 2019. The largest change is the switch from a 2.9-liter twin-screw supercharger to a 2.65-liter high-helix roots supercharger.
What Goes Into Building A Factory Powerhouse
While seeing “350” associated with an LSX-based engine isn’t the norm, nothing about this engine would be considered standard, as the COPO design and engineering team puts a significant amount of effort into ensuring that the parts they use – whether built in-house or sourced from the aftermarket – not only provide the most performance possible, but live for a more-than-reasonable amount of time, under hard use.
“We have dynos and look at power, obviously, but there’s more to choosing a part than power,” says Wysocki. “Say for an oil pan; we look at oil pressures, oil temperatures, and then compare it to a baseline pan and figure out if it gains or loses horsepower based on windage and things like that. Then we take our combinations to the track and make sure we can hit our performance targets.”
Once the part(s) in question’s performance has been validated to meet the COPO team’s goals, then the torture tests begin, because the Chevrolet Performance team isn’t interested in moon-shot passes and parts that need to be replaced at short intervals.
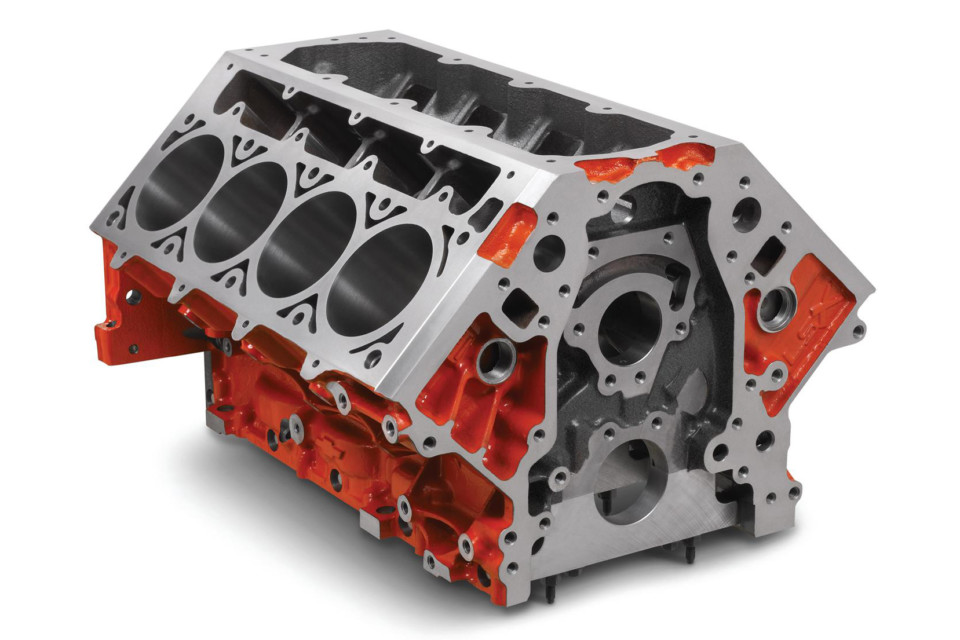
With the desire to race what they sell, and not need to reinvent the wheel, the COPO engineers used an iron LSX Bowtie block as the basis on which to build the beast. Proven, easily sourced, and in their supply pipeline, it was an easy choice.
“For durability we run at least 25 passes at the track, on a car just to get real-world data on its performance,” Wysocki explains. “Then we take that track data, from the burnout to shutdown, and we program that data into the dyno cell back at the factory, and we make 200 runs just like we are at the track — we shift it at 8,200 rpm and everything, just like we are at the dragstrip.”
While you might think that having all the resources of a manufacturer the size of Chevrolet, there might be a lot of trick one-off (or 69-off, as the production numbers may be) parts in the engine. However, that really isn’t the case. “We try to use as many [Chevrolet Performance] parts catalog parts as possible, like the block, and the base LSX head,” Wysocki reveals.
For parts that aren’t in the catalog, however, the COPO team doesn’t try and reinvent the wheel. “A lot of times, we just go straight to our partners and say, ‘We need a part with these specs.’ Like for valvesprings we use PSI. We’ve used them for years and years. We tell them the specs we need, and they make a spring to those specs for us.”
Diving Into the Short-Block
Starting with an off-the-shelf Chevrolet Performance LSX cast-iron engine block with a 9.240-inch deck height, the factory finishes the bore size at a fairly standard 4.125 inches, giving plenty of cylinder-wall thickness with the Siamese bores. A true priority main oiling system makes sure the engine’s lifeblood gets where it’s needed, when it’s needed. In the name of strength, billet steel main caps are utilized to keep the crankshaft in place under the most severe conditions.
“We’ve offered the 327 cubic-inch option with the 2.9L supercharger and the 4.0L supercharger in the past. The 4.0: supercharger made enough power to put it squarely into NHRA Super Stock territory, which meant we had to rely on the 327 with the 2.9L for our top of the line Stock Eliminator effort. We’re allowed by NHRA to have up to a 350 with the 2.9L supercharger, and we wanted to reach the peak of NHRA Stock capabilities,” says Curt Collins, Chevrolet Performance Manager, of the decision to move to a 350 cubic-inch displacement.
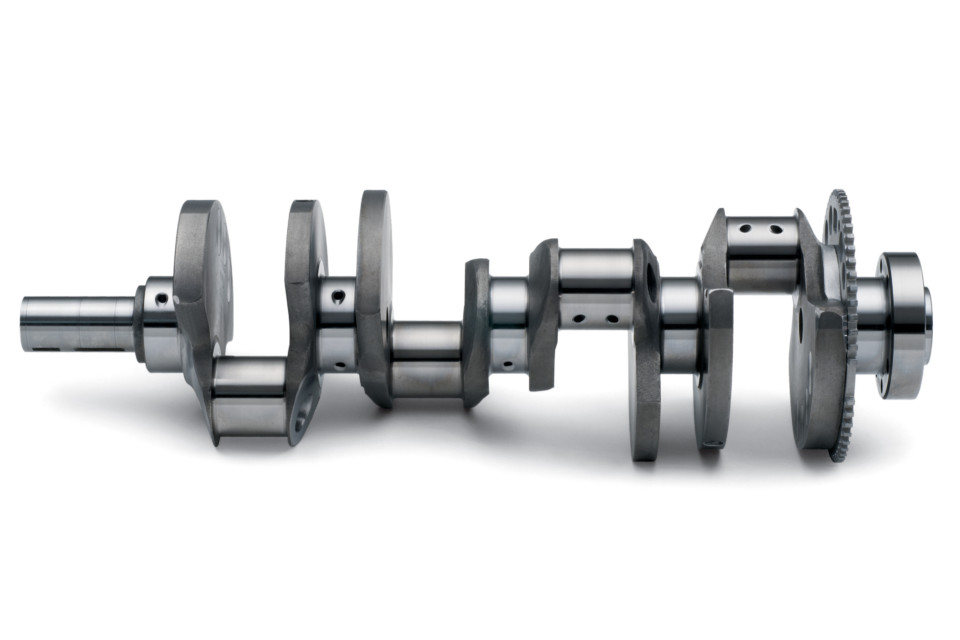
The crankshaft needed to be an uncommon 3.370-inch stroke to achieve the 350 cubic-inch displacement to maximize the NHRA Stock Eliminator rules. The team turned to Callies and had them produce a forged-steel “Dragonslayer” crankshaft with all the required specs for the COPO engines.
To achieve the 350 cubic-inch displacement, a non-standard 3.370-inch stroke is used. To accomplish this, Chevrolet Performance turned to Callies Performance and selected a Dragonslayer crankshaft for the engine. Using a high-purity 4340 steel forging, with standard rod and main journal diameters held to .0003-inch tolerances for roundness, Callies then heat treats the cranks in its proprietary Ultra-Case process, for an extremely durable, six-counterweight crankshaft (no center-counterweights allowed in Stock Eliminator).
“That short stroke is definitely easier on the crank than the 427’s 4.00-inch stroke,” says Wysocki. “We do all our factory validation testing to 8,200 rpm. While the Factory Showdown guys are spinning it much faster than that, they are running an eight counterweight crank where Stock isn’t.”
Attached to the Callies Dragonslayer crank are a set of 6.350-inch Callies Ultra H-Beam connecting rods. An extremely feature-rich connecting rod, the Ultra H-Beam rods were designed from the outset for competition use. Starting off as a pure Timken steel alloy, the forging incorporates a number of details, like pin hoop stiffening bands forged into the outside of the small end of the rod, to improve the .927-inch pin-bore’s concentricity at high-RPM. Using a purpose-built “Ultra” rod bolt, the rod’s ultimate strength is further increased.
Actually handling the combustion of the air and fuel are a set of MAHLE slugs. Starting as a 2618 aluminum forging, the dome is profiled to achieve a static compression ratio of 10.9:1, while the skirts are coated in MAHLE’s Grafal anti-friction coating. A MAHLE .043-inch ductile-iron, radius-faced top ring features a plasma-moly face coating. Below that is a .043-inch plain cast-iron tapered second ring. A low-tension oil ring with chrome plated rails finishes off the ring package in the COPO engine.
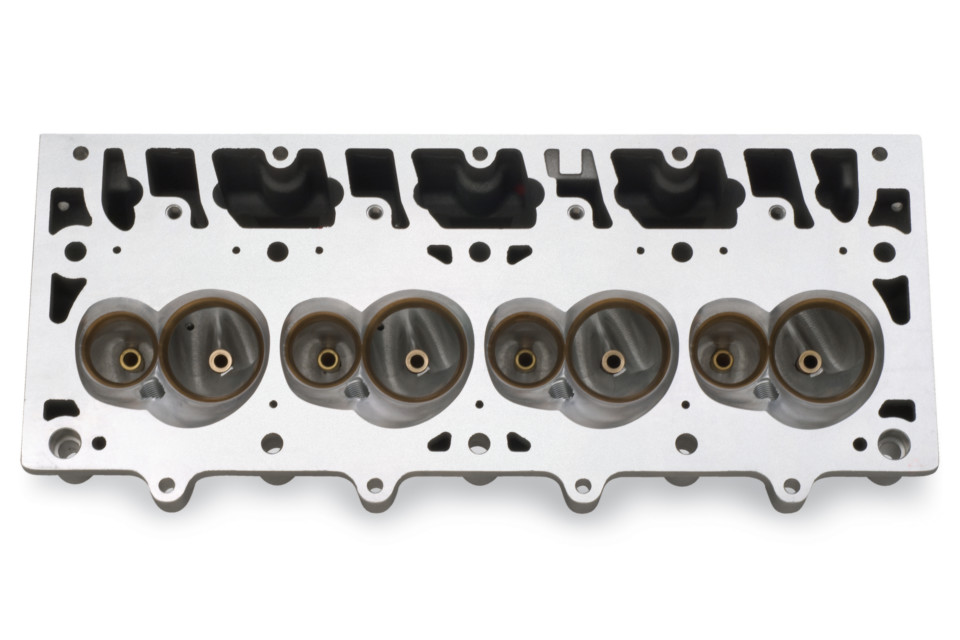
The LS7-based cylinder head features a 70cc combustion chamber volume, and houses a set of Del West titanium 2.205-inch intake valves, and sodium-filled 1.615-inch exhaust valves.
“Our pistons are a custom design from MAHLE. Basically, we tell them what we want for compression distance and ring height and things like that,” says Wysocki. “There are NHRA specs we have to meet as well for things like size of the ring grooves, how far down the top ring has to be from the top of the piston, and so on, that they comply with.”
A Moroso fabricated aluminum oil pan holds seven quarts of oil to keep the wet-sump oiling system fed, while an SFI-approved 10-rib ATI Super Damper keeps all the engine’s harmonics in check. Unlike the other COPO engines in the lineup, the supercharged 350 shuns an electric water pump, with engineers instead opting for a modified LS3 mechanical pump.
The Top of the Beast
Moving up top, the cylinder heads are what you might expect to see, in that they are LS7-based LSX castings, which have been given the full Chevrolet Performance CNC treatment, opening the intake port up to 289cc and the exhaust port to 105cc. The 70cc combustion chamber houses Del West titanium 2.205-inch intake valves, and lightweight sodium-filled 1.615-inch exhaust valves. Sealing the heads to the block are a set of Cometic multi-layer steel gaskets with a raised sealing bead.
Acting as the brain of the engine is a billet-steel Comp Cams hydraulic roller camshaft. It features .641-inch of lift at both the intake and exhaust valves, with 242 degrees of lift at .050-inch on the intake side, and 257 degrees on the exhaust. Riding the cam lobes are a set of Johnson hydraulic roller lifters, with a 3/8-inch Trend Performance chromoly pushrod riding on each lifter.
The heads, available out of the Chevrolet Performance parts catalog, have been fully CNC-ported, opening up the intake ports to 289cc and the exhaust to 105cc, while being optimized for a supercharged application.
1.8:1 ratio LS7 rocker arms with roller-bearing trunnions translate the pushrod’s motion to the valve. PSI Spring Max Life beehive valvesprings of an undisclosed rate keep the valves under control, while Chevrolet Performance lightweight steel retainers and locks keep everything together.
Giving the COPO 350 engine its grunt is the new-for-2019 Magnuson 2.65-liter roots supercharger. Gone is the larger 2.9-liter twin-screw unit in favor of the smaller but more efficient huffer based on Eaton’s TVS 2650 rotor pack. “The TVS is more efficient at higher blower speeds, which meas it doesn’t impart as much heat into the charge, leading to lower intake manifold temps. There is performance to be had with that supercharger,” says Wysocki. Controlling the airflow into the blower is Magnuson’s monster billet aluminum 109mm throttle body.
“It was a fun, challenging, interesting project. Magnuson had a designer assigned just to us. We’d call them on Monday and exchange some data. Wednesday, the parts were freighted in, and we’d be on the dyno the next day.” – Tom Wysocki, COPO Racing Project Lead
“The Magnuson blower has a standard Eaton 2650 rotor set. Nothing has been massaged on it or changed,” says Wysocki. “We do drive it from the rear with a jackshaft arrangement, whereas a standard production unit is driven off the front, but the bearings and rotors are right off the production line.”
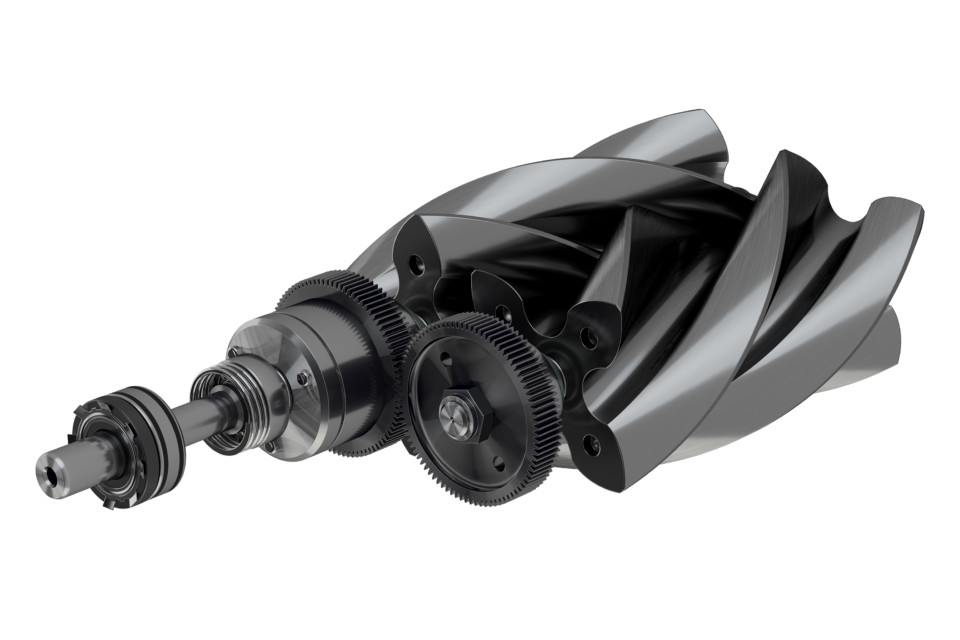
The rotor pack used in the Magnuson supercharger is an off the shelf Eaton TVS 2650 assembly. The high-helix Twin Vortices Series imparts much higher efficiencies than a standard roots rotor design, making for a much higher performing supercharger.
Being off-the-shelf doesn’t mean any less performance is expected from the parts. In fact, the superchargers are all bench-tested before going out the door. “Every COPO supercharger that Magnuson builds, they run on a test stand for eight minutes, at representative speeds and boost levels. So they know when it arrives, it’s right,” explains Wysocki.
Getting all those spent gasses out of the engine efficiently is a high priority, and to do that, the COPO engineers selected a set of 2-inch diameter, 30-inch long primary stainless headers from American Racing Headers.
Feeding the beast is no small task, and to do so, an Aeromotive Eliminator fuel pump is utilized, along with an A1000 fuel pressure regulator that is boost referenced. The 80 lb/hr EV1 fuel injectors are run at a base fuel pressure of 58 psi, with additional pressure added through boost compensation.
These charts from Magnuson show some of the efficiency, rotor speed, and output temperature differences between their TVS 2650-based unit and a 2.9-liter twin-screw supercharger, based on their in-house testing.
All of these well-engineered systems combine to produce an NHRA horsepower rating of only 580 horsepower. Wait, what? Don’t lose your minds. The NHRA power ratings are goofy, and only those deeply entrenched in the NHRA class racing world truly understand the methods to the madness.
You can always pull out your trusty Moroso slide rule (or go to one of the online calculators) and get a rough estimate of how much power it takes to push a 3,200-pound car to 8.60-second elapsed times. We’ll give you a hint – the SWAG says about four digits-worth.
So Much More Than Just a Blower Swap
The development of the 2019 supercharged 350 was far more than just swapping a new blower onto the existing engine and calling it a day, and necessitated quite a bit of reengineering of the whole engine package. “There’s a cog belt with external gears on the back of the supercharger that’s not on a Whipple,” says Wysocki. “The Whipple blower speed is controlled by the front pulley sizes only while the Magnuson can vary the front pulley and also the rear cog drive tooth counts. For example we sell the unit with 32 teeth on the drive side and 34 teeth on the driven which can be switched using the same belt to speed up the blower drive.”
“It was a fun, challenging, interesting project. Magnuson had a designer assigned just to us. Sometimes in the course of a week, we’d have some design changes that we needed to incorporate. We’d call them on Monday, exchange some data, Wednesday, the parts were freighted in, and we’d be on the dyno the next day.”
The entire process of switching superchargers for the 2019 COPO engine was a surprisingly short 10-month ordeal. “We started the supercharger program in earnest with them in Jan 2018. In May of ‘18 we had an engine with their unit on it, in a car, in Rockingham for preliminary testing,” reveals Wysocki.
While the COPO's 2.65-liter Magnuson supercharger uses a lot of standard components, one thing that is specific to the COPO engines, is the jackshaft and cog-belt arrangement, to drive the blower from the rear. With both front pulley sizing as well as interchangeable rear cog gears, there is much more blower-speed adjustment in this setup than previous generations. There was significant engineering and testing put into the new arrangement to get the best possible performance from the setup.
“Then in August we went to US131 with basically all production parts in a car. Then in October, we ran our 200-pass validation of the whole package on the dyno. So if you think about it, that’s 10 months from concept to total production. That’s a very quick, very intense program.”
Now, the Supercharged 350 engine is an available option for the 2019 COPO Camaro, and soon will be available as a crate engine from Chevrolet Performance, under P/N: 19368698. “Currently, all the parts we need are still going to COPO production itself. But the crate version will be available soon,” says Wysocki.
Now you’ve gotten a glimpse into just how much effort it takes from the entire COPO team to “just swap the blower” on a factory-produced racing engine.

As you can see, the COPO supercharged 350 is all business, from the SFI-approved ATI Super Damper, to the 109mm throttle body and reconfigured supercharger drive system. This beast is built for one thing — making reliable power.