Way back in 1964, Tom Lieb was looking to fill a void in the neglected Volkswagen aftermarket and started Scat, a specialty VW parts distributor. Not long after the company began developing and manufacturing its own engine internals and expanded to cover more markets under the name Scat Crankshafts, where the team’s keen eye for quality and the finer details created explosive growth and positive recognition in the industry.
This growth allowed Scat’s team to further refine their craft, where after nearly half a century of hard work and family operated success, some of the best equipment had been amassed – including over 20 CNC machines; three, four, and five-axis mills; 12 rod honing machines; 12 crankshaft grinding machines; and 8 polishers to name a few. Requiring such a large arsenal of machines pretty much forced the acquisition of Scat Enterprises‘ current home, a 42,000 square foot manufacturing and distribution facility in Redondo Beach, California.
Many gearheads know of Scat Crankshafts’ expansive line of off-the-shelf cast, forged or billet cranks for Chrysler (including Jeep), Ford and GM racecars and streetcars. Few are aware that Scat’s team is also capable of developing custom crankshafts for anyone and virtually any application. To learn more about how Scat approaches the design of custom crankshafts, we reached out to Tom Lieb and he was more than happy to walk us through his company’s process.
“From a manufacturing standpoint, when a crankshaft order comes into our shop there’s a very specific sequence of events that our team follows,” said Lieb. “You can change up the order slightly but eventually for the crank to get to X-machine it has to make its way through Y-machine first and before it can go there it needs to pass through someone else, it really doesn’t matter what the crank is for specifically. Obviously, the bigger the crankshaft the more time it will spend at each machine, but at the end of the day they all pass through the same hands at some point, they all need oil holes, they all need rod journals and they all need flanges.”
“The design side of things is another story entirely,” Lieb continued. “We have to go through the design and engineering process before we get to manufacturing, and there are definitely some cases where a custom order comes in and a crank needs some special details outside of the normal routine. We can’t turn on any of the machines in the shop without first having technical drawings and CNC programs written.”
As you would expect, the first step of the design process is the customer reaching out to Scat. “Once the customer supplies our team with their specific crankshaft requirements, it can go one of two ways,” Lieb explained. “It’s either a crank we’ve never made before and we have to start from square one, or it is something we have worked with before but requires modifications.”
Back To The Drawing Board
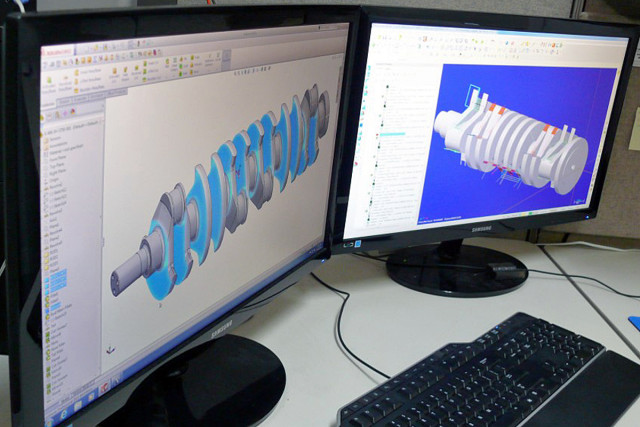
One of the first steps taken after the initial drawing has been signed off on is for Scat’s engineers to create a 3D solid model.
“Let’s just say we are asked to build a crankshaft for a 350 small-block Chevy. We’ve made a countless variety of 350 cranks, so it would have what we call a packet that includes all of the manufacturing information for our existing options,” said Lieb. “If a customer contacts us requesting a 350 crankshaft with a particular stroke and rod journal size, we would start with that packet to see if it already exists in our system.”
“Now, the packet starts out with a technical drawing,” Lieb elaborated. “Then our engineers move on to a 3D solid model, which displays detailed dimensions of the entire crank; then it moves on to a list detailing the order of operations in the shop and a series of programs for the CNC machines. So if this customer wants a variation of the crank we haven’t already done, our engineers have to first figure out what specifically will be different about this custom crank in comparison to what we’ve already done and make the necessary changes on paper.”
The operator of every machine in Scat’s facility that the crank is ran through during the manufacturing process is given what is called a layer drawing, that instructs the machinist on exactly what to do. “The machinist is given a CNC program that was made by one of our programmers; a list of required tools, the machine number that they will be working on, and a detailed blueprint of exactly what they are going to be working on,” said Lieb. “Because our quality control is so high, none of the decision making is left on the shop floor where someone might accidentally add a value instead of subtracting because they aren’t in the right environment to make those decisions or it wasn’t double checked. A machine won’t be turned on in the shop without completed paperwork.”
“We always know exactly where a crankshaft is in the manufacturing process,” stated Lieb. “Around the shop we have a series of computer terminals. A machinist will log into one of these terminals with their employee number, and then enters the work order number for the future crankshaft they have been assigned. The time and date is then logged, along with the machine number they are working on and the operation number. So the terminal might say ‘on Friday at 9:17 am – John Doe started working on operation number four, on machine number three, for crankshaft XYZ.'”
“Once that specific operation number is completed, the machinist will log out of the terminal for that task and I receive a report at the end of each day detailing what each machinist did that day and where exactly every crankshaft is in the manufacturing process,” explained Lieb. “It’s basically a daily report giving me a screenshot of exactly what is happening on the shop floor. That way if a customer calls for an update on their order we can give them a detailed timeline telling them exactly what has been completed, what still needs to be done, who has handled it, and where it currently is in the shop. It’s another layer of quality control for us.”
“Scat Crankshafts operates under the auspices of the quality control procedures set forth by big names like Ford, Chrysler, GM and Honda. Where traceability and accountability are of utmost importance,” stated Lieb. “If there is ever a problem, we know what the problem is, what step it is in the process and exactly how many pieces are affected. We won’t manufacture a crankshaft for a local racer any differently than we do for the big name manufacturers, every order is treated with the same level of control.”
“We have over 4,000 different off-the-shelf crankshaft design variations in our system today, but as of late about half of the jobs on the shop floor are something we’ve never worked with before or are a variation of a crank that we haven’t done,” said Lieb. “The perfect example happened just the other day. We got an email from one of our frequent customers that we build motorcycle cranks for – we are working on several cranks for him right now in the shop and the email said ‘I hope it’s not too late, but we changed the location of the oil hole…’ That added an additional operating layer that required a new completed drawing, a new solid model, a new operation sheet, and new tooling being added to the carriage of the machine; then our programmers need to write a new CNC program for that tool. It can really be quite a challenge at times, but this is what we live for.”
Starting From Scratch
When Scat is approached with a custom design for a crank that they are unfamiliar with the customer will usually first send the company a drawing of exactly what they want, then Scat’s engineers will review the drawing to make sure that all of the dimensions are realistic.
“Not too long ago we actually received a new crank drawing from one of the big three [Ford, GM, Chrysler], and when one of our engineers was reviewing it he found that their drawing was requesting a bolt pattern on the flywheel flange that was larger than the outside diameter of the crankshaft itself,” Lieb exclaimed. “We can’t magically put bolts in space, so one of those two dimensions is obviously wrong.”
“Once the initial drawing has been approved by our engineers, a solid model is then created based off of the drawing and we then have all of the dimensions needed to create the basic shape of the crankshaft as a 3D model in our computer,” explained Lieb. “From there our engineers will write the CNC programming needed for each machine used in the manufacturing process, which gives us the fine details such as stroke, the shape of the counterweights, oil hole placement and sizes, the bolt pattern on the back, pilot bearing hole diameter, and other detailed specifications.”
“After all of this data is reviewed and approved, it is released to the shop floor where the process is identical to any other crankshaft we produce. The 18, 20 or 30 different operations required to make the crankshaft follow the exact same sequence as any other crankshaft we produce. From there our team will then add or subtract steps based on what is required for that specific crank.”
When you have a million dollar antique, like the ones you see at Pebble Beach, and the crankshaft is in two pieces, most of the time you’re not going to find an off-the-shelf replacement and you certainly aren’t going to find any manufacturing diagrams -Tom Lieb, Scat Crankshafts
“When you have a million dollar antique, like the ones you see at Pebble Beach, and the crankshaft is in two pieces, most of the time you’re not going to find an off-the-shelf replacement and you certainly aren’t going to find any manufacturing diagrams,” said Lieb. “So we receive quite a few antique cranks in two pieces where the customer just tells us, ‘I need this exact same crank, but in one piece.’ So what we do is take those broken pieces and collect information about the dimensions so we can figure out what it is actually supposed to look like.”
“Once we have a clear idea of what the crankshaft originally looked like, we revisit the failure,” Lieb continues. “Over the course of time ourselves and other talented crankshaft manufacturers and engine builders have discovered better designs and improved manufacturing methods, so we will look at the break and figure out why it failed and draw out any structural or reliability improvements needed to make sure it doesn’t happen again, then the paperwork makes its way to the shop and falls in line with the rest of the cranks being manufactured.”
Conclusion
With over half a century of experience in the industry, Tom Lieb has built Scat into one of the biggest names in the manufacturing of crankshafts, connecting rods and full rotating assemblies for OE manufacturers and the aftermarket. Their quality control level is on par with that of any large automotive manufacturer and all of the machine work is done right here in the United States.
If you’re looking for high quality off-the-shelf or custom rotating assembly components, be sure to check out Scat Crankshafts website for your domestic V8 build or Scat VW for Volkswagen platforms.