For hundreds of years, rock fibers were used for almost every application where a heat-resistant material was needed. These asbestos fibers were a traditional material dating back to pottery making in the stone age. In manufacturing, rock crushed all other friction materials.
Its use was continued until health concerns made the material illegal in many countries for construction, manufacturing, and fireproofing. Opting to seek safer materials for friction clutch-plate manufacturing, Raybestos Powertrain invested in a paper mill with the intent of creating safe and durable friction material processes.
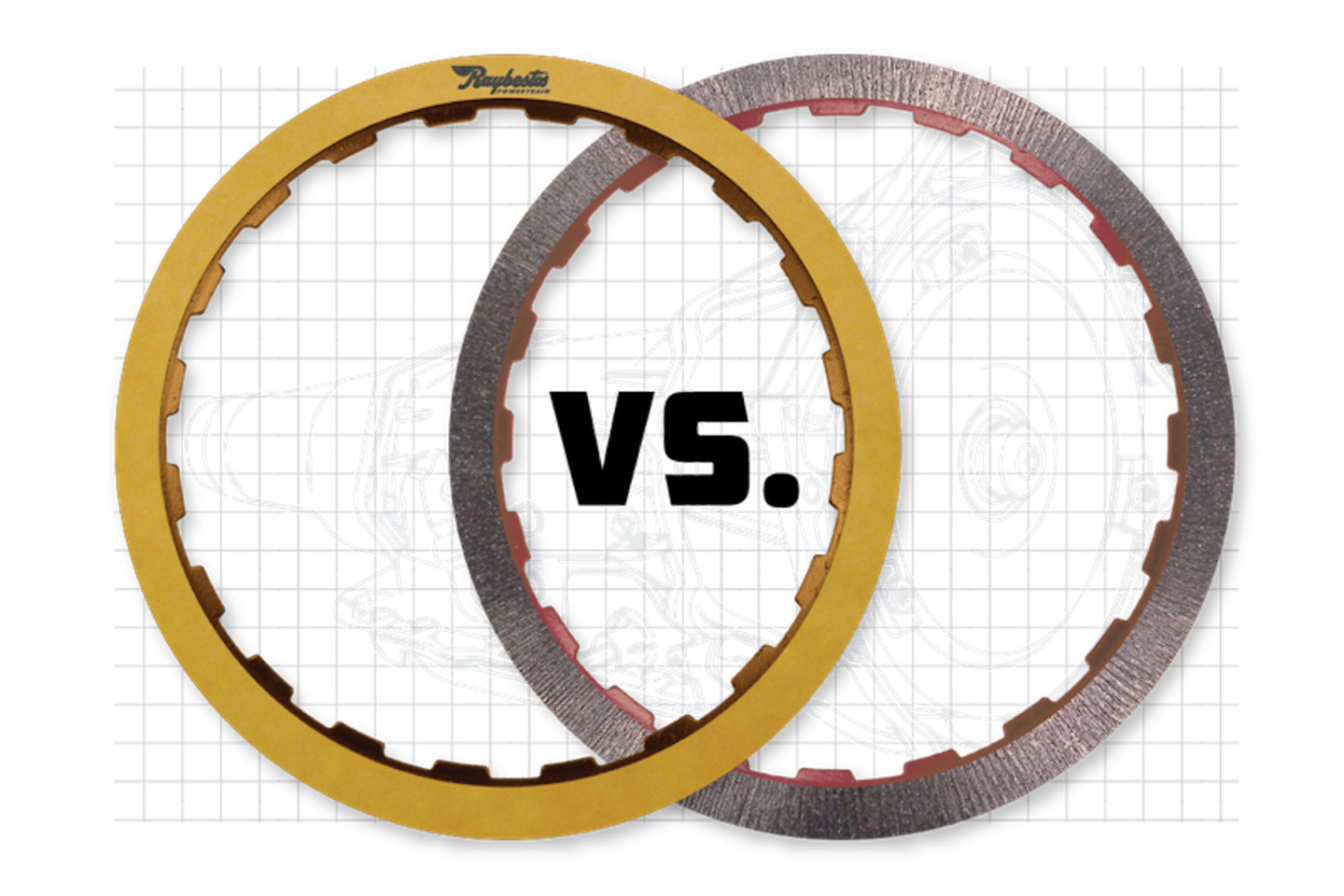
Paper-based materials result in excellent load distribution and favorable friction characteristics make these materials a much better and more durable choice.
In a social, economic, and engineering game of Rochambeau (rock, paper, scissors), Raybestos Powertrain paper had metaphorically beaten rock. The engineering science of shaping the paper has symbolic scissors cutting paper to complete the hand-game analogy. In the real world, Raybestos Powertrain has discovered even greater advantages in using paper as a backing material for friction discs. Obviously, many of these advantages also work in favor of automotive enthusiasts.
A Single Piece Of Paper
When you think of friction plates in an automatic transmission clutch pack, paper is not the first thing that comes to mind. In fact, most automotive enthusiasts don’t realize that paper is even used in manufacturing friction plates. Yet, the entire manufacturing process begins with a single piece of paper. “Most, if not all of our competitors do not manufacture their own friction material paper,” said Nick Truncone.
Nick is the Marketing Manager for Raybestos Powertrain and the driving force behind educating automotive enthusiasts about friction materials. “We have our own massive paper mill operation in-house,” he adds. “This is a huge advantage to us, especially during times of broken supply chains.” Originally, the paper mill was incorporated as a means of quickly meeting customer needs. It has become a huge edge in every aspect of manufacturing Raybestos products. “When the friction material process was changed to use paper, and this paper mill was purchased,” explains Angie Petroski, Director of R&D. “The new formulations that were designed to replace asbestos started to be manufactured in Crawfordsville, Indiana” she adds. “Currently, the paper mill designs, develops, and manufactures paper for automotive OE, heavy-duty equipment, and the automotive aftermarket.”
“It’s also worth noting that we make our own adhesive materials that are used to bond the friction material to steel. Our adhesives and paper are made in the same plant in Crawfordsville,” Nick explained. From engineering to manufacturing friction material and adhesive, the company has complete control over the entire process.
A Major Advantage In The Current Marketplace
The current supply chain breakdowns in every marketplace have been eye-opening. This is especially true in the automotive aftermarket where enthusiasts are left waiting for manufacturers with empty shelves. Manufacturers typically can’t make parts without other products, so the supply has dropped behind the overwhelming demand.
For many companies, this is a problem that probably won’t be going away anytime soon. For other companies, the supply chain issues do not impact their operations. Raybestos is one of those companies. What started out as a safer material alternative turned out to be an adaptability advantage on many different levels.
What Are Friction Plates?
To explain how much of a big deal this process is, we need to explain what friction plates are and how they work. Clutch friction plates work with steel plates in alternating layers inside a clutch pack within automatic transmissions. Generally, the friction plates are splined on the inside and mate with a shaft. The steel plates are usually splined on the outside, where it locks into the clutch housing that is connected to another shaft inside the transmission. A hydraulically actuated piston forces the plates together, locking the clutch unit into a single drive shaft. This is what allows the engine rotation to be transmitted to the drivetrain.
When transmissions are rebuilt, these friction plates are replaced. When enthusiasts replace stock engines with more powerful aftermarket engine platforms, factory clutch packs are often not strong enough and clutch slippage can occur. This can also be a problem when stock engines have power adders. High-performance enthusiasts will often have the clutch plates replaced or buy transmissions with friction plates that can handle more torque.
We’ve taken a very simple approach to explain what a clutch pack does in automatic transmissions, but in real applications, the clutches in an automatic transmission are much more complex. There is often more than one clutch, and each is actuated by hydraulic pressure through valves, springs, and internal passages within the transmission.
Raybestos Technical Center
Located about 50 miles from Indianapolis, and a couple of hundred yards from the Crawfordsville manufacturing plant, is the technical center. “We are also one of the few companies with an independent technical center this size,” Villain stated. Well known in the industry for its innovative designs and formulations of proprietary materials, the tech center operates daily to develop cutting-edge technology and materials for automakers and aftermarket customers. The ultimate goal is to give the automotive public quality performance products that are reliable, whether it is a direct customer or through an OE or aftermarket source.
Angie Petroski’s research and development team works alongside the sales team to identify new product opportunities. Outfitted with a full array of test equipment, including a mini on-site paper mill in the test center, the R&D crew can rapidly develop new products or processes. According to Angie, the facility has no less than 20 dynamometers to assist with testing.
Dealing with temperatures, spring pressures, new OE transmission designs, fluid viscosities, and other issues, Angie’s team is constantly on the prowl for ingenious solutions. At the top of the list of things to deal with is heat. Heat is a known enemy to friction and demands tough material, adhesives to survive in a hostile environment like an automatic transmission. Angie’s team finds the answer to combat those issues.
Every Application Is Different
Heat is not the only factor. Not by a long shot. Many times, the OE customers will come to the team with a full set of criteria for new clutch plates. “Torque capacity, the fluid it will be working in, the fluid available, flow rate, energy capacity over time (longevity), and other design inputs go into formulating a material and the process by which that final product is made,” Angie points out. “These all go into the design of the product for the final application.”
Looking through Raybestos Powertrain’s current catalog of friction materials, we can immediately identify materials for fuel-saving applications, some for performance, and many for multi-purpose applications. Raybestos has friction plates specifically for street/strip use, enhanced performance, and even performance racing. For transmission rebuild shops and home enthusiasts, a full array of OE replacement friction plates are also available. Lest we forget, there is a special GPZ friction material set of plates that improve performance and durability by withstanding high stress, high temperatures, and repeated cycling. These are typically used for towing applications.
Staying On The Cutting Edge
Almost from the beginning, Raybestos Powertrain was on the cutting edge of technology. Opening its doors in 1902, it became a local success in Bridgeport, Connecticut. Less than 17 years later, the company has grown from a small four-man shop to a super company that manufactures a million clutch plate facings a year for the first time in 1919.
When the first Hydramatic transmissions were developed in the 1930s, Raybestos friction clutch plates were critical to its success. Raybestos championed the Second World War effort by producing clutch plates for the B-29’s two-speed planetary supercharger. Not resigned to automotive or even earthly applications, Raybestos Powertrain composites went out of this world to make footprints on the moon as Neil Armstrong walked on the lunar surface with boots made with Raybestos composites.
Not resting on its past accomplishments, the company has continued to develop innovative friction materials with the release of GPX, HT, and TechniTorq friction technologies.
As far as new applications go, the company uses its in-house resources for new product applications as well. The new ten-speed transmissions offer another opportunity for the team to show its ability to respond to industry needs. “We are striving to own the ten-speed from an aftermarket perspective and performance realm,” says Villain. Raybestos was the first company to offer replacement clutch plates for these transmissions. “We launched plates for the Ford 10R80 transmissions and the 10L80 GM transmissions over three years ago. That was the same year they came out in OE applications,” he affirms.
For The Future
Our future plans include more articles that showcase Raybestos’ performance on and off the track. We will also be producing in-depth “how it is made” articles and some with “how-to” articles for do-it-yourselfers. It all starts with a piece of paper. In the meantime, you can find out more about these products by visiting Raybestos Powertrain online at www.raybestospowertrain.com.