Several months ago, we brought you LS5.0’s bottom-half coming to life. Now, we’re bringing you the top half of the engine project as it comes together. For a quick refresher, Project LS5.0 is our attempt to match, and possibly beat, the Coyote engine from the original LS vs Coyote shootout.
With the short-block assembled and ready to go, the next step for us was to finish assembling the top half of the engine. Just like the short-block’s components, we put a lot of effort into striking a balance between staying within the original $9,999 (2016 dollars) budget and getting the LS engine to perform in the upper RPM band, reliably.
Checking Piston-To-Valve Clearance
The first thing we needed to do was to check piston-to-valve clearance. In a custom application like this, you can’t just look at cam specs and guess as to whether or not the valves will clear the pistons — especially since we have domes on the piston, small as they might be. There are several ways to check the actual clearance; our chosen method is with a degree wheel and checking springs.
In order to check piston-to-valve clearance at specific crankshaft positions, we need to swap the intake and exhaust valvesprings on cylinder one to lightweight checking springs, so that we can move the valves with only finger pressure. This also has the secondary benefit of not introducing any deflection into the valvetrain, since there isn’t a lot of pressure.
You might think that you simply want to check clearance at the top of the piston’s travel, but in reality, That’s not where the valve and piston are the closest. On the intake valve, the piston and valve are the closest as the intake valve chases the piston down the bore on the intake stroke, so we measure at 10 degrees after top dead center on the intake stroke.
On the left, you can see that we measure .120 inch of piston to valve on the intake and on the right you can see we get .190 inch of clearance on the exhaust.
The minimum clearance we’re looking for in a combination like LS5.0 is .080 inch. The dial indicator shows that we have .120 inch of clearance. Since that measurement is without a head gasket in place, we know we can add another .040 inch to that number, and since we’ll likely be retarding cam timing on the dyno, our intake valve clearance will only increase.
On the exhaust side, the closest the valve gets to the piston is as the piston approaches TDC and the the exhaust valve is closing, on the exhaust stroke. So, we check piston-to-valve clearance at 10 degrees before top dead center on the exhaust stroke. We’re looking for a minimum of .100 inch of clearance on the exhaust side, and without a head gasket in place, we are almost double that, at .190 inch of clearance. As far as piston-to-valve is concerned, that might as well be a mile.
Getting Into The LS5.0 Top-End Build
With the clearances good, all the checking equipment was torn down and assembly could begin. The first step was to install the lifters, since in an LS you have absolutely zero access to the lifter bores once the cylinder head is on. For the LS5.0 build, we’re using a set of COMP Cams’ new link-bar Evolution hydraulic-roller lifters (PN: 89571-16).
The Evolution line of lifters use COMP’s improved, thicker outer body, a proven needle-bearing roller wheel and axle, but with a new hydraulic cartridge design that reduces the volume of oil in the lifter to gain the benefits of a reduced travel lifter, but without actually reducing the available travel of the plunger. “Less oil volume is a huge advantage, since there’s less chance of air getting to the hydraulic plunger,” says COMP’s Engine Builder Sales Manager Chris Mays.
Additionally, having more travel allows for a range of preload settings based on use case. “We recommend around a turn, to a turn and a quarter of preload in street applications, and a flat .050 inch off the bottom in more serious race applications,” explains Mays.
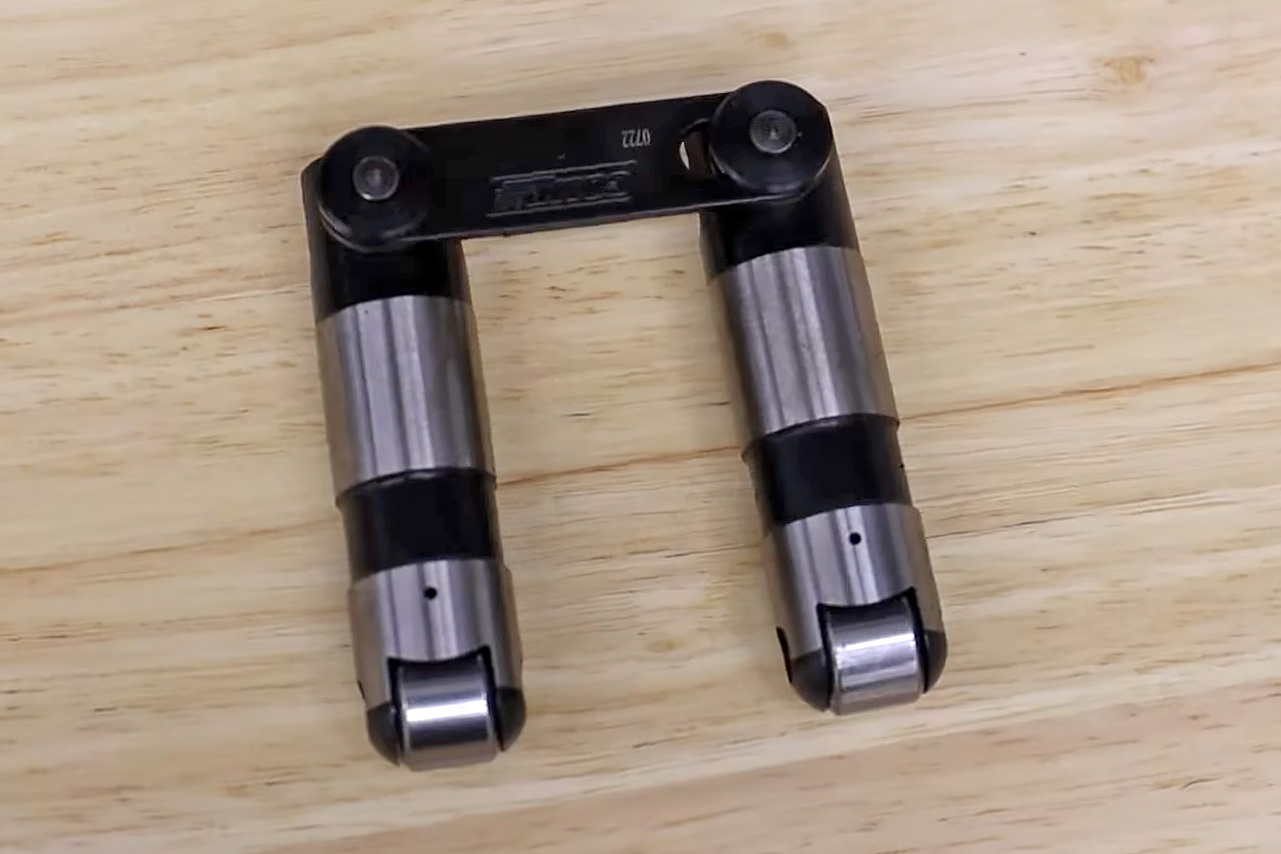
The COMP Evolution hydraulic roller lifters looks like ordinary lifters from the outside. However, the real magic is contained within the hydraulic cartridge inside of the lifter body.
Mays also assures us these have been Spintron tested to 9,000 rpm without issue, and will perform exactly how we want them to in this project. Oh, and the hydraulic cartridge design is removable from the lifter body and serviceable, extending the life of the lifter.
To take advantage of the travel of the lifter, and to be able to easily test lifter preload on the dyno, We opted for a set of COMP’s LS XD-A pushrods (PN: 896805-16). The XD-A is a two-piece design that uses shims to set the length of the pushrod, from 7.320 inches to 7.552 inches. While traditionally indicated for use in solid-roller valvetrains, the easy adjustability on the dyno was a key factor in our choice, especially since they are Spintron- and dyno-proven to over 9,000 rpm, so stiffness will not be an issue, whatsoever.
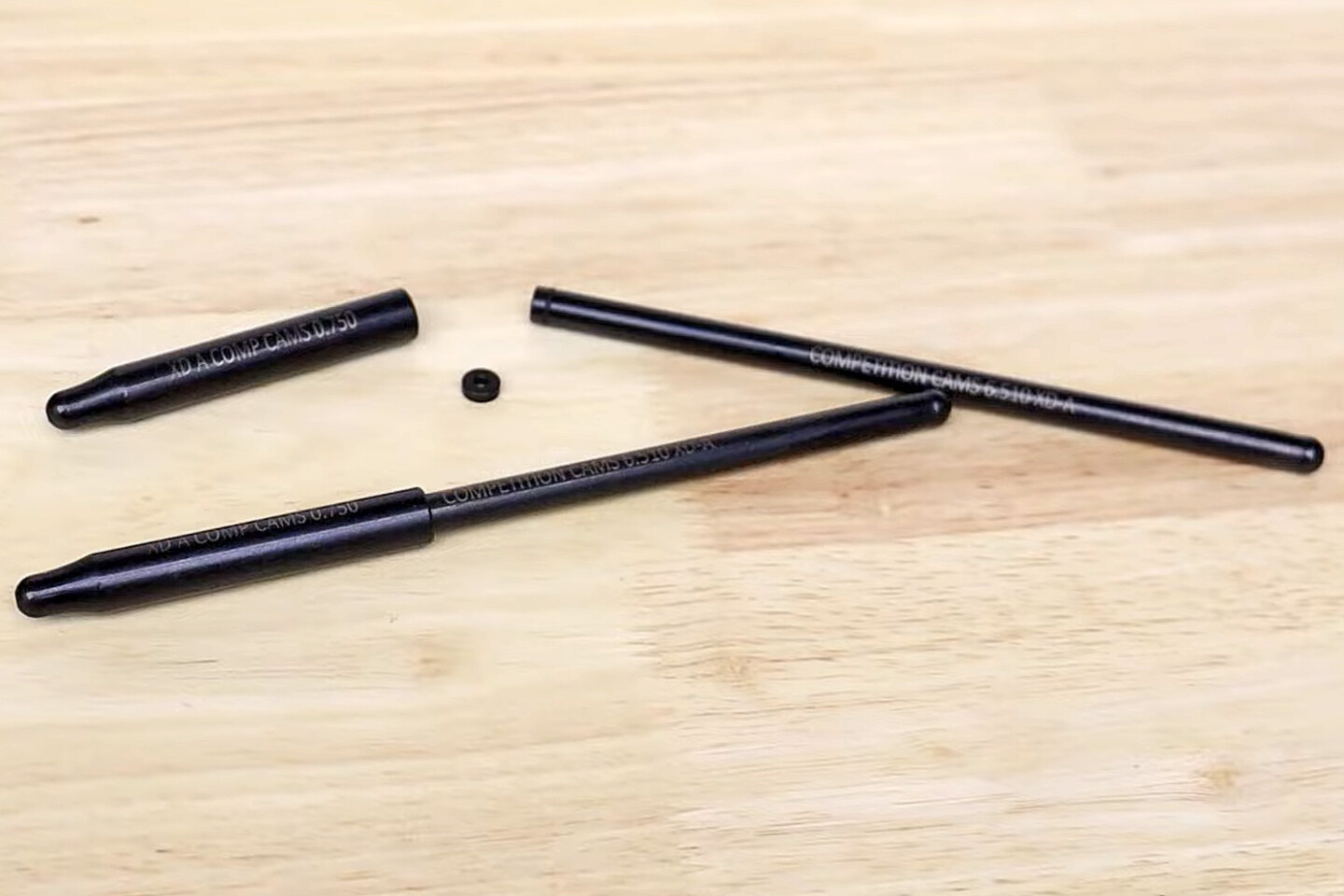
The COMP XD-A two-piece pushrods are shim-adjustable, allowing you to dial in an exact amount of lash in mechanical roller applications, or lifter preload in our case.
The Head Of The Class
As we showed in a previous LS5.0 article, the Lingenfelter cylinder head porting service really transforms the factory heads into performance powerhouses. We threw our stock 799s on the flowbench and saw peak flow of 242 cfm at .600 lift, and after Lingenfelter worked their magic, the new peak intake port flow of 320 cfm represents a 33-percent increase in flow. To achieve that, they open the stock cathedral port to 228cc. The exhaust port is opened up to 84cc, and achieves a new peak flow of 224 cfm from each port.
The chambers are treated to the same CNC treatment, profiling and contouring the factory shape into something better performing. The valve seats are then given a three-angle valve job to fit the upgraded valves. The target for their standard program is a 65cc chamber, but since we are shooting for 11.3:1 compression, we had them deck the head down to a 60cc chamber volume.
Lingenfelter has opened the intake port (left) to 228cc from the factory 210cc. The exhaust port (center) has been opened to 84cc. The chambers (right) have actually been CNC profiled and then shaved down to 60cc, with Manley 2.02-inch intake and 1.575-inch exhaust valves.
We also opted for the stainless-steel valve upgrade option. For this set of heads, Lingenfelter and Manley Performance specified a set of hollow-stem stainless steel valves measuring 2.020 inches in diameter on the intake, and 1.575 inches in diameter on the exhaust. The 8mm-stem valves are swirl-polished under the head and have fully machined faces to increase combustion efficiency. The hollow stems will reduce valvetrain mass without compromising strength, which is critical for the high-RPM goals of LS5.0.
Besides the valve upgrade, we also opted for the valve spring upgrade Lingenfelter offers. The main component of the upgrade are a set of dual valve springs, that measure out to 160 pounds on the seat at their 1.800-inch installed height and 424 pounds at .675 inch of lift. We won’t be taxing them quite that hard with this cam and rocker setup, and they will maintain excellent valvetrain control at high-RPM. Additionally, the upgrade kit comes with seven-degree locks and lightweight titanium retainers.
Clamping And Sealing
Sealing the head to the block is not a place to cut corners on a project like this, so we went with a pair of Cometic multi-layered steel gaskets. As we discussed in this article, in a pure performance application, the tighter you can run your gasket bore clearance, the better, so after consulting with Cometic and Ben Strader, we ended up with a tight .002 inch of gasket clearance on a .040-inch compressed-thickness MLS gasket (PN: C15361-040).
A great head gasket is nothing without the proper clamp load on it. To that end, we opted for ARP 8740 head studs to secure our heads to the block. The Gen IV (2004 and later) kit (PN: 234-4317) utilizes the same length studs for all ten 11mm fasteners. Our kit also utilizes ARP’s stamped, patterned washers designed to grip the surface of the cylinder head. We used ARP Ultra-Torque assembly lube on everything to ensure the perfect clamp load on the heads.
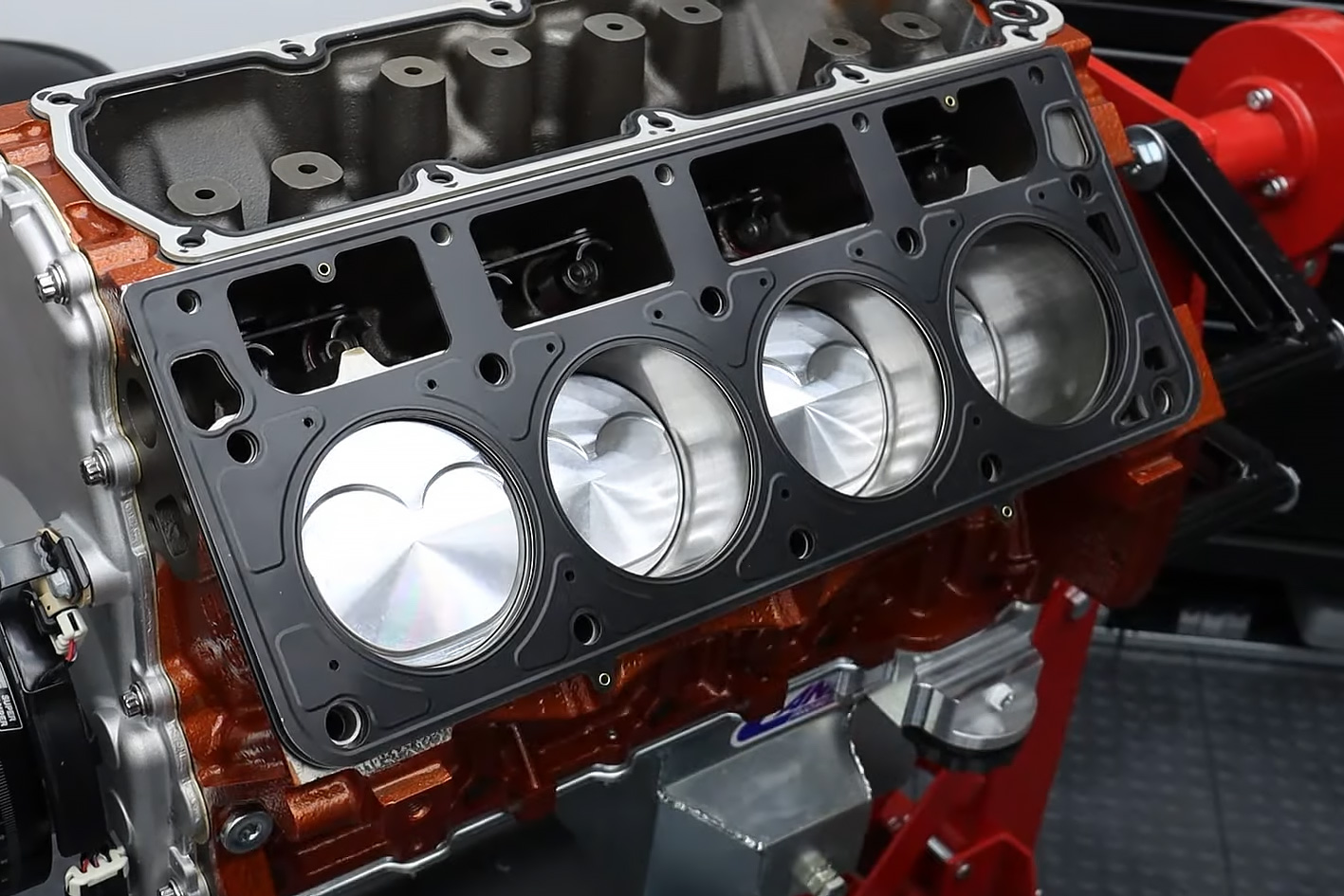
The Cometic MLS head gasket LS5.0 is using has a super tight bore clearance. Normally, you’d want more clearance for an average rebuild, but considerations were taken to be able to safely run the tight clearance.
LS5.0 Gets The Shaft
When it comes to LS rocker arms, it’s been proven time and time again, it’s tough to beat the OEM design. GM really got it right with the LS rocker arms. However, there is absolutely room for improvement. We know that a trunnion upgrade does wonders for the factory LS rocker arm. COMP’s engineers went a step further in designing the Max-Lift BSR Shaft Rocker Kit. By taking the proven LS style rocker arm, adding a bushing-style trunnion bearing, and then tying everything together on a common shaft, you have what has proven to be one of, if not the best dollar-to-performance ratios on a valvetrain component out there.
The Max-Lift BSR shaft rocker arm system (PN: 1981-16) is a direct bolt-on for our 799 heads (LS3 and LS7 styles are also available), and the increased rigidity of the system makes for a platform that reduces deflection, translating our cam lobe’s motion into valve motion more efficiently and accurately. The rocker bodies are finished in a plasma nitride to minimize friction. That not only means a more efficient system, but a more durable one, as well.
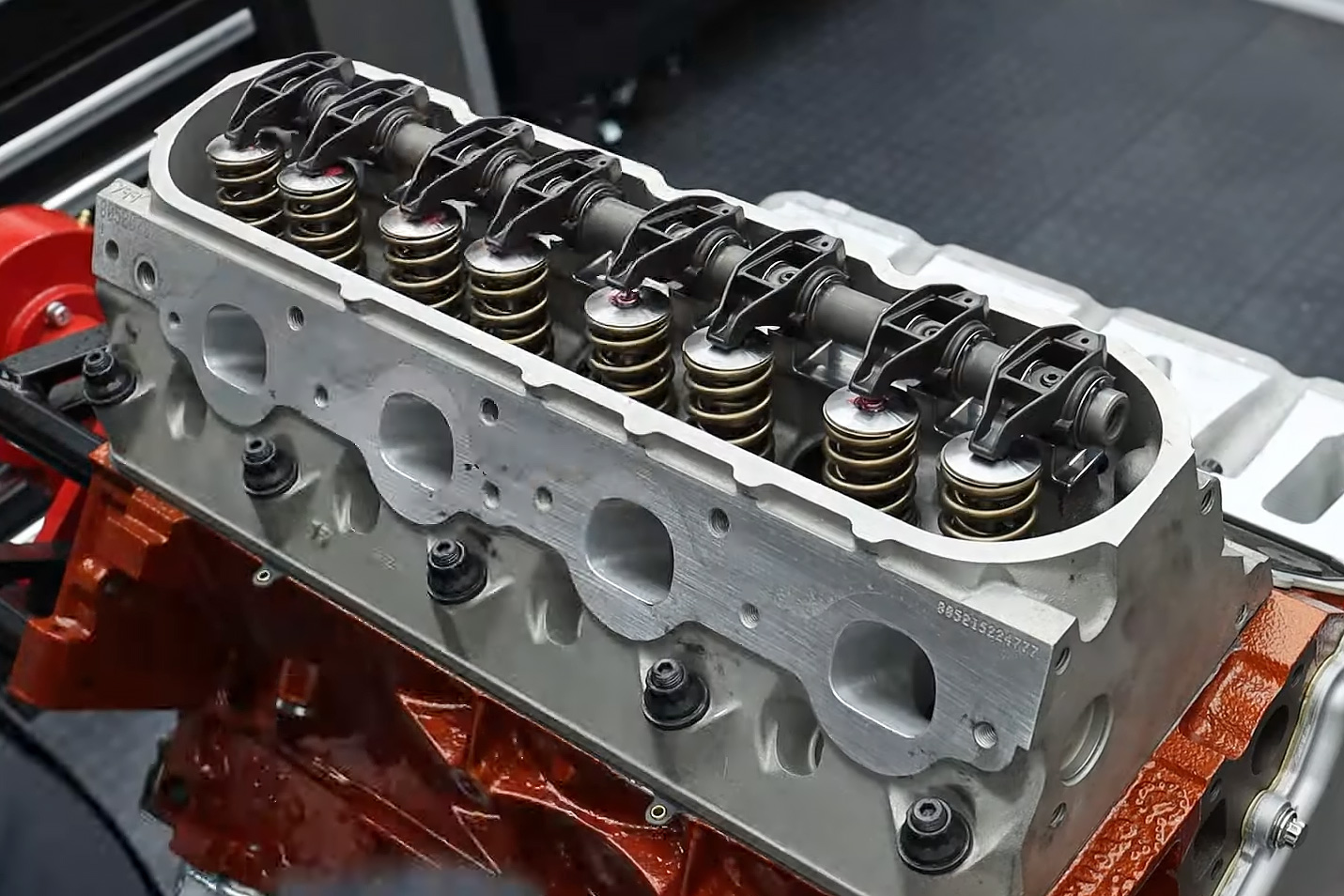
The COMP Max-Lift BSR shaft rocker arms use the proven LS rocker arm design, with a solid trunnion bushing and common shaft to increase valvetrain stability.
While the Max-Lift BSR system is designed to bolt right into the factory rocker stands, we opted to upgrade the factory units. PRW Power makes a set of billet aluminum rocker stands for both LS1 and LS3 style heads (PN: PQX-0273461). They are precision machined from 7075 aluminum and are designed to be flatter and hold tighter tolerances than the factory stands, increasing the overall rigidity of the system. When you’re talking about the kind of RPM we want to see with LS5.0, the little things start to add up.
Adding to the stability of the rocker arm system is an ARP rocker arm stud kit (PN: 234-7207). Replacing the 8mm rocker bolts with a set of 8mm studs and 12-point nuts. The studs torque to a slightly higher value than the factory bolts, and due to the nature of a stud, provides more clamp load. Again, the small things add up above 8,000 rpm.
Topping off the cylinder heads and valvetrain are a very special pair of valve covers for LS5.0. Not only are Performance Design’s carbon fiber valve covers incredibly lightweight, thanks to their carbon construction and titanium mounting hardware, but their fill ports are -12 ORB-threaded, so we can replace the lightweight billet caps with -12 fittings on the dyno. Plus, they are carbon fiber. Who doesn’t love carbon fiber?
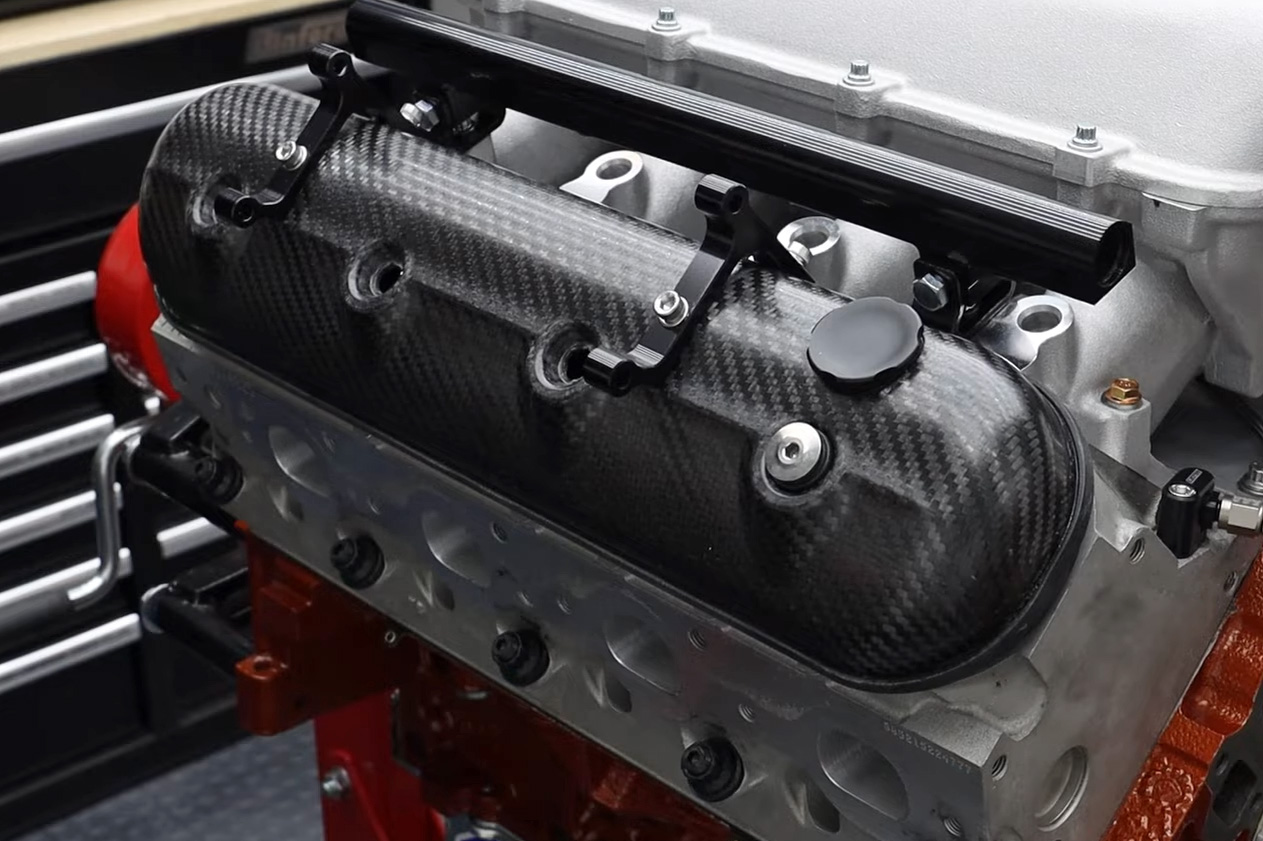
The Performance Design carbon fiber valve cover really fits the whole theme of the build nicely, as well as bringing some much needed functionality to the engine.
Topping It All Off
Feeding a small-displacement, high-RPM engine isn’t the easiest of tasks. The current school of thought behind such an engine is that big plenum volume combined with short runners is the hot ticket. Well, Holley EFI makes exactly that combination in its Lo-Ram EFI manifold for cathedral port heads (PN: 300-620). Designed specifically for a 3,500 to 8,000 rpm operating range, the Lo-Ram features the same forward-facing intake lid as the Mid-Ram and Hi-Ram, meaning that it will accommodate up to a 105mm throttle body. Additionally, since it uses the same bolt pattern as the other intakes, you are able to use any of the optional lids available for the Hi-Ram intake. The intake kit also comes with a set of billet aluminum fuel rails, specific to the Holley intakes. The fuel rail comes with brackets to fit both tall or short fuel injectors.
The 6.5 inch runners and healthy plenum volume (left) will help the engine make power in our desired RPM range. The lid of the Lo-Ram (center) is the same as Holley's Hi-Ram, giving us options in the future. The massive 105mm throttle body (right) will make sure there's as much air as the engine can ingest.
Since the largest throttle body that will fit on the forward-facing lid is 105mm, that’s the throttle body we chose for LS5.0. Specifically, the Holley EFI billet 105mm throttle body with the straight bore (PN: 112-583). The straight bore variant will provide the absolute maximum airflow to the engine, while a host of other features — like a clockable TPS mount, idle bleed adjusters, and an adjustable PCV passage — add to the functionality and drivability of the engine.
With the LS5.0 assembled, the next step on this project is to load it up and make the trek to the dyno. We have a Holley Terminator X to run everything on the dyno as we spin it up to 8,000 rpm and see how the engine compares to the simulations and the Coyote from the original LS vs. Coyote series. And, now, for the question I’m sure you’re all dying to know the answer to — the budget.
$9,999 In 2016; How Does LS5.0 Stack Up?
Let’s recap. The original budget for the engines in the 2016 competition was $9,999. Since we can’t directly compare the prices of components from almost nine years ago to components today, and prices have changed even since the project started, we’ll normalize everything from 2016 dollars to 2024 dollars. According to the U.S. Bureau of Labor Statistics Inflation Calculator, the January 2016 $9,999 budget adjusts to $13,255 today.
The top-end cost of LS5.0 (along with some of the valvetrain components that weren’t included in the first total sheet) comes to $7,159.72. Added to the raw cost (no competition-allowed exclusions) from the short-block, our total for this project, intake to oil pan, is $12,654.55. Adjusting to 2016 dollars, that’s $9,561.82, or about $440 under budget. If we actually play by the same rules as the engines in the original competition, we can knock another $800 off of that total, since machine work was never counted. That means we came in way under-budget, with an adjusted competition price of $8,761.82.
With that extra $1,237.18 of budget, we don’t even have to jump through any logical hoops to justify or exclude the cost of the carbon fiber valve covers from the competition. Now, the only thing left to do is see if LS5.0 can match the Coyote’s 510 horsepower at 7,600 rpm on the dyno.