When you think about pushrod engines, you likely think of older engines from a bygone era. Firstly, the pushrod engine’s main rival — the overhead cam design — is more than 120 years old itself, so calling one “antiquated” and the other “modern” is absolutely incorrect. In fact, there is a ton of research and development that has gone into pushrod technology in the past several decades that makes modern pushrods highly effective valvetrain components, thanks to improvements in a variety of pushrod parameters.
We reached out to Erson Cams to talk to us about some modern theories on pushrod design and to try and clear up any misconceptions or misunderstandings that surround the deceptively simple metal rods. First, we should probably discuss the three main pushrod parameters that identify a pushrod.
The first is diameter. This is the outer diameter of the pushrod at its thickest point. This spec is crucial for physically fitting a pushrod into an engine. The second is length. This is the distance from tip-to-tip, and it plays a crucial role in ensuring that your valvetrain geometry is correct. The third is wall thickness. The thickness of the wall of the pushrod affects the pushrod’s stiffness and overall weight. These three pushrod variables need to be balanced with the engine’s desired RPM, valve spring pressure, cam lift, and cylinder pressure. Consideration of each of those variables will provide the best-performing pushrod possible.
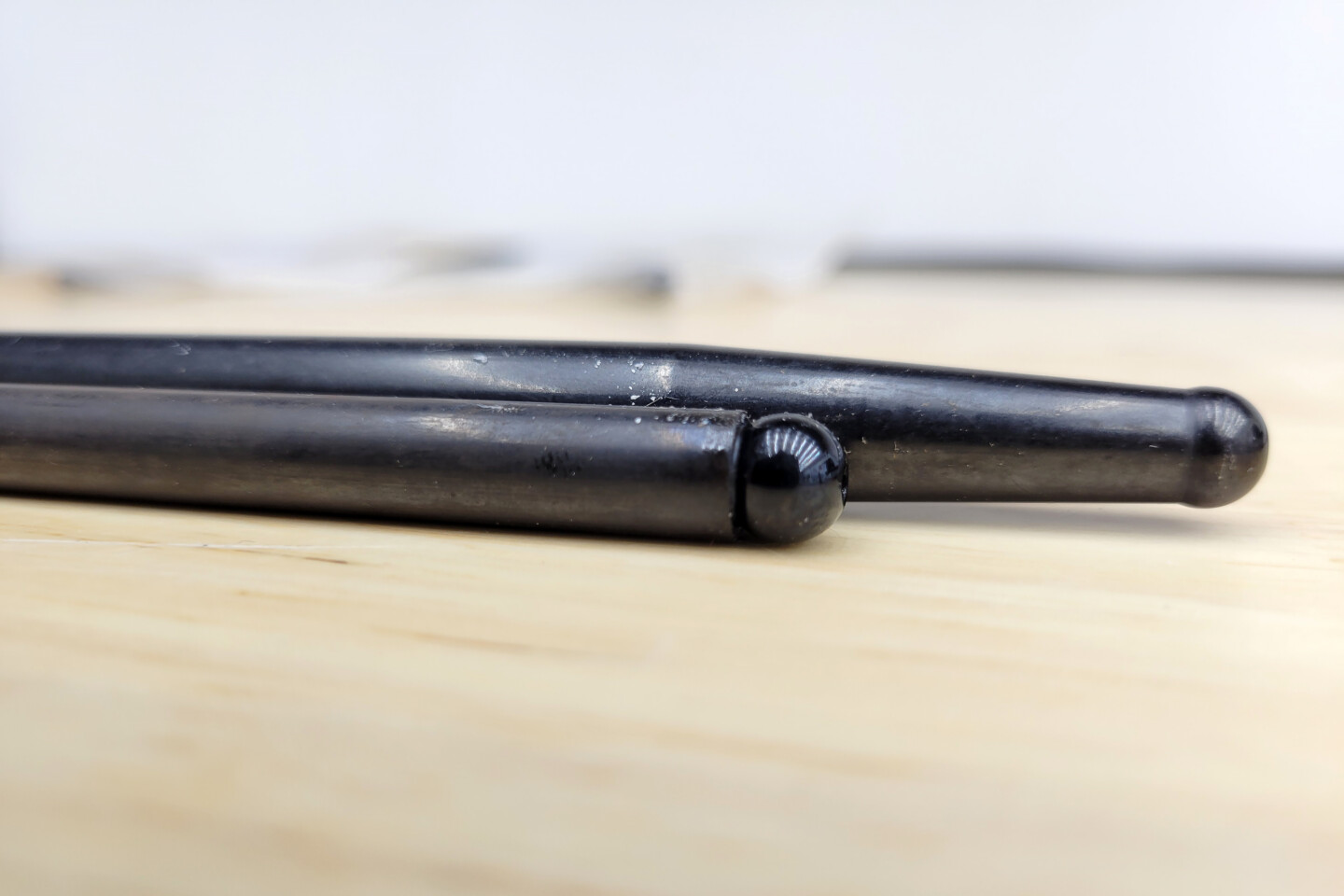
Pushrod design has come a long way since the first iterations of overhead valve engines. While the straight, thin-wall pushrod still very much exists and thrives, advanced designs like variable-taper thick-wall behemoths are also available for high-output engines these days.
Looking At Pushrod Length
Pushrod length is one of the least adjustable pushrod parameters of your engine. There are various factors that determine what your pushrod length needs to be. Block deck height, cam location, cylinder head deck thickness, rocker height, and valve length are but some of the variables that combine to determine the correct length pushrod. So while not highly variable on the end-user side, the length of a pushrod is an important consideration since a pushrod’s length is directly related to its stiffness. Just think about a diving board.
“Stiffness and weight favor shorter pushrods where possible. However, most engine configurations pretty well dictate the relative pushrod length,” says Erson Cams’ Jack McInnis. So, rather than an adjustable parameter, pushrod length will likely dictate — at least in part — the rest of the pushrod requirements. That leads us to the other two variables, outside diameter and wall thickness.
Is A Bigger Pushrod Better?
It only stands to reason that the larger the outside diameter of a pushrod, the stronger it will be, making it a critical pushrod parameter. So, why not just cram giant pushrods into everything and make the engine bulletproof? Well, it’s not that simple. “The biggest pushrod that will fit will give the best results in real-world performance for max effort engines,” explains McInnis. “The outside diameter of a pushrod solely depends on the allowable space in your cylinder head and sometimes the space allowed near the lifter.”
While that seems pretty cut and dry on the allowable outside diameter of the pushrod, we are an industry of horsepower junkies. Since when do we just accept limits without pushing the boundaries? Enter the tapered pushrod. “A tapered pushrod allows you to run a larger, stronger pushrod while retaining its ability to function properly in limited space,” McInnis relates.
A tapered pushrod isn’t a magic cure-all, but it definitely allows for an improvement between sizes. “Wall thickness being equal, a 7/16-inch pushrod with a taper will not be 100-percent as strong as a 7/16-inch straight pushrod would be, but it will be far stronger than a 3/8-inch straight pushrod and can still operate without interference to the rest of the valve train components,” says McInnis.
We’ve come so far that even taper angles can be dialed in to balance clearance and performance characteristics. “There are various taper configurations,” explains McInnis. “Stocking pushrods will generally be configured for an acceptable range of applications. Then, custom units can be designed for more specific requirements.” So far, we’ve determined that application dictates length, and we want to fit the largest pushrod body possible. That leaves out third variable, wall thickness.
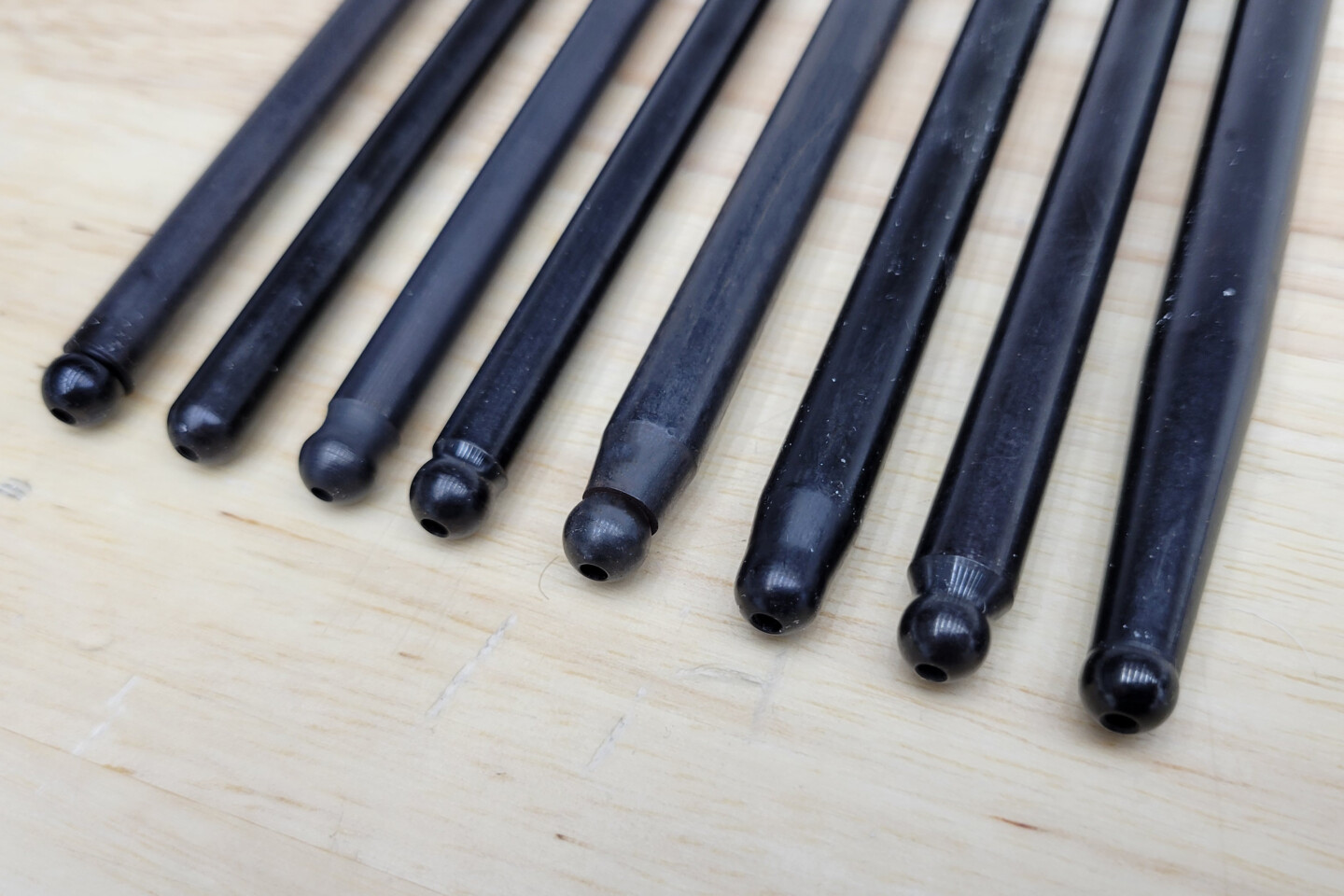
There is technically a difference between clearance and taper. Taper will most likely affect the overall pushrod performance, where a clearance only reaches back from the ball to the largest diameter of that pushrod. On the far right is a 7/16-inch tapered pushrod design, while the third and fourth from the right are simply clearanced 3/8-inch pushrod designs.
Wall Thickness Rules The Roost
A pushrod’s wall thickness is probably the largest variable that can be played with. It can drastically affect a pushrod’s stiffness, strength, and weight. One thing that McInnis pointed out during our conversation, is that a pushrod’s weight plays a far smaller part than we thought it did. “Weight is really not as much of a concern as you might think,” McInnis says. “The difference between a stock 5/16-inch-diameter pushrod in a small-block Chevrolet and a 7/16-inch-to-3/8-inch taper pushrod is only a couple percent of the effective weight.”
“Effective weight” is a crucial term to take note of here. McInnis continues, “This is because the pushrod is on the slow side of the valvetrain. The valve side of the valvetrain is the critical side where any weight savings will make significant improvements.” So while weight isn’t a deal breaker when you actually need the additional stiffness and strength, adding weight for no reason is just as silly as it sounds.
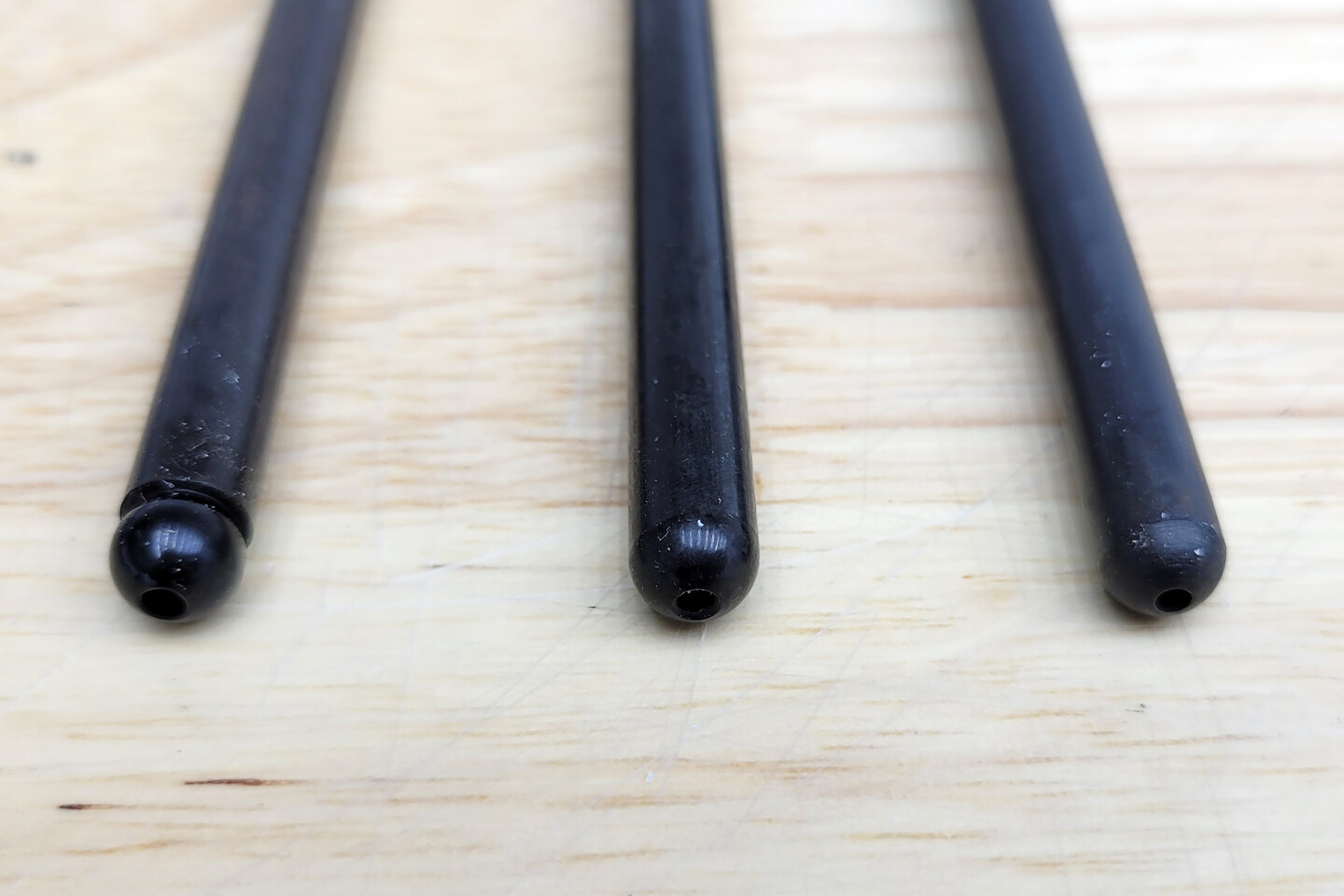
These three 5/16-inch-diameter pushrods might all look the same, but inside, there is a very clear difference between the three, as you’ll see in the image below.
“We typically recommend heavy wall pushrods in all high-spring-pressure applications. Extreme cylinder pressures with power adders (nitrous and boost) call for an even larger pushrod,” explains McInnis. “Street performance-type engines, that don’t see very high RPM, and have lower spring pressures can work fine with thinner wall lighter pushrods.”
We touched earlier on the fact that a longer pushrod will need a thicker wall thickness to achieve the same stiffness, but another is that a larger-diameter pushrod will be as stiff, if not stiffer, than a smaller-diameter pushrod with a thicker wall. “A larger diameter pushrod spreads the load over more surface area, which is good. In many cases, there is not adequate clearance for larger diameter pushrods, so a smaller diameter with thicker walls is a solution,” conveys McInnis.
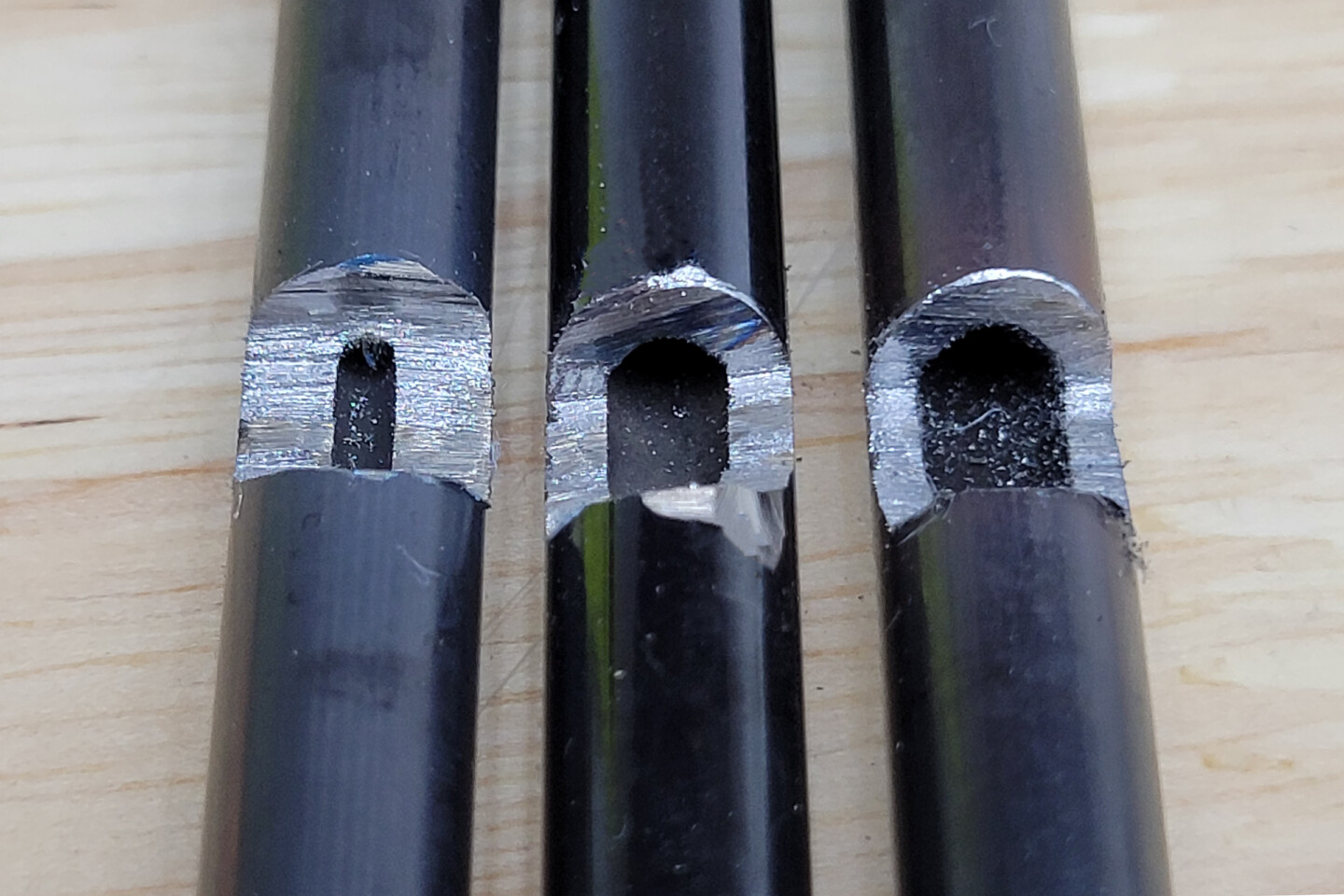
Here, you can see that all three of those pushrods have different wall thicknesses. On the right is a pushrod with .an 065-inch wall thickness. In the center is a more typical .080-inch wall-thickness pushrod, and on the left is a much more stout .120-inch wall-thickness pushrod. Excuse the messy cuts, getting through a hardened pushrod isn’t the easiest thing to do.
Another factor to consider is the valvetrain geometry and pushrod angle of the engine design. “Oblique angles which create side loading will also cause deflection,” relates McInnis. Luckily, wall thickness is an easily adjusted parameter, as long as there remains enough inner diameter to not become a restriction to oil flow.
At the end of the day, what it comes down to is that the engine parts combination will dictate the length of the pushrod as well as the maximum diameter pushrod you can run. You can adjust wall thickness within the pushrod parameters to get your desired strength and stiffness while balancing the weight of pushrod. If your combination has increased valve spring pressure, cam lobe aggressiveness, and/or RPM, you should be upgrading your pushrods to better withstand the new stresses being placed upon them.