Dart Machinery‘s new LS Next2 engine block offers the leading edge of technology advancements for the LS-based engine platform. In May, the first-anywhere details on the block’s design and construction were released right here; that article discussed the methods employed by the Dart team during the block’s development process.
As part of that process, a partnership with Dart was established to source one of the company’s billet-aluminum LS Next2 blocks. It was delivered to Bryan Neelen and the guys at Late Model Engines so that it could be turned into a state-of-the-art, top-flight engine topped off with the ultimate in running gear, and fronted by a ProCharger F-1X-12 supercharger.
The intended purpose? To provide the BlownZ project car — a supercharged monster of a machine — with the best possible powerplant using the LS engine platform. BlownZ has been at the forefront of LS engine development ever since it entered into the Power Automedia stable of project vehicles, and has won numerous races on the West Coast in the process.
The initial article from May covered the down-and-dirty details on the engine block’s construction; this article will cover everything from the initial machining processes on the block, through all of the components selected to withstand the rigors of all-out performance on an engine capable of running well into the six-second quarter-mile zone; in the process, the latest developments in LS engine construction will be employed to maximize horsepower potential and engine longevity. Read on for the details!
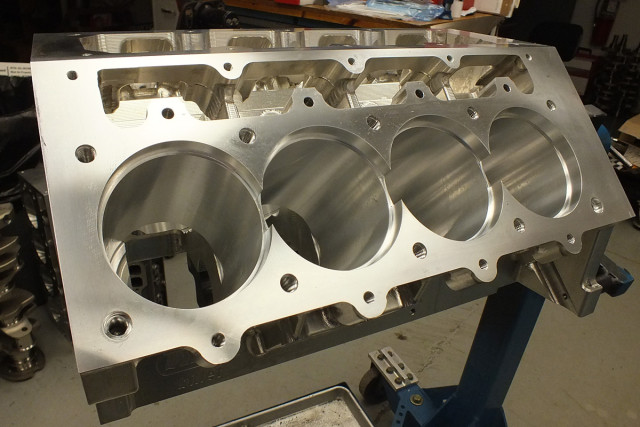
Dart’s LS Next2 billet block is designed from the outset to withstand the rigors of serious competition. The bare block received a set of sleeves to accept Diamond hard-anodized pistons.
Why The LS Next2?
Engine Spec Box
- Block: Dart Billet LS LS Next2, 9.750-inch deck height
- Crank: Bryant Racing Billet 4.125 stroke BBC Snout, 2.750 Main
- Rods: GRP Pro Series Billet, 6.300-inch long, .927-inch pin
- Pistons/Pins: Diamond Racing Hard Anodized, Trend TP-1 DLC-coated pins
- Rings: Total Seal M2
- Damper: ATI Racing Super Damper
- Camshaft: Custom solid roller
- Pushrods: Trend Performance
- Lifters: Jesel Keyed, .937-inch diameter
- Oiling System: Dailey Engineering Dry Sump
- Cylinder Heads: Edelbrock LS-R by Race Flow Development
- Rocker Arms: Jesel aluminum intake, steel exhaust, 1.8:1 ratio
- Camshaft Drive: Jesel belt-drive
- Valves: Ferrea Titanium
- Valvetrain: PAC 1.522-inch-diameter double springs, retainers, locks, locators
- Intake Manifold: Wilson Manifolds billet/sheetmetal
- Poweradder: ProCharger F-1X-12 supercharger
- Supercharger Drive System: Component Drive Systems’ gear drive
- Exhaust: Custom headers from REF Unlimited/Burns Stainless
- All Fasteners: ARP
In fact, despite the LS engine’s propensity for excellent road-race performance in Z06 Corvettes and Z/28 Camaros when properly equipped, the LS Next2 was developed strictly to meet a need in the drag racing marketplace.
“There are things that go on in a drag race engine that don’t happen in a road-race, circle-track, or street engine,” says Maskin.
The main thing is the rate of acceleration. For example, a Pro Stock car is in second gear for three tenths of a second — that means the car is accelerating from 8,500 to 11,000 rpm or higher in three tenths of a second. The only other form of motorsports where an engine is called on to do that would be Formula 1 or IndyCar, unless it’s disconnected from the drivetrain.”
To address the extreme duty requirements faced by engines placed into drag racing duty, the LS Next2 uses a larger crankshaft main bearing diameter than the factory LS block — 2.750-inch for the LS Next2 versus 2.559-inch for the stocker — and in the process makes use of a crankshaft that’s inherently stronger.
The larger main bearing dimension in the LS Next2 came to pass through a discussion with one of Maskin’s engine builder partners, who discovered that a customer’s standard LS Next engine (with the 2.559-inch main bearing dimension) was having some issues with cap walk when trying to put a set of twin turbos in front of it and make 2,500-plus horsepower.
The LS Next2 has been thoroughly re-engineered to not only improve the thickness and strength of the entire block, but also to take advantage of the oiling improvements Dart has engineered into its LS Next and LS Next2 product lines.
“According to my sources, the stock LS7 uses somewhere around 18 gallons per minute revved up, while our design uses much less and still provides more-than-adequate oiling across the board,” explains Maskin.
The 2.750-inch main bore housing in the LS Next2 is .191-inch thicker than the stock LS dimension and adds much-needed strength to the crankshaft area. Billet steel caps are used. The extra head bolt bosses at the outside of each cylinder can also be seen here.
(Left) The top-side head bolt hole can bee seen in the upper left of this photo. These are fastened from underneath the deck with a nut and washer. (Right) Dart has engineered the strength in throughout the block, with external ribs machined into the material to provide the fasteners with a load path to dissipate stress.
This 441 cubic-inch bullet built from the LS Next2 uses one of Dart’s 9.750-inch deck height blocks that has been treated to some of the company’s tricks. One important item is the use of a camshaft that’s been raised .388-inch from the stock dimension. This accomplishes two things — to raise the camshaft out of the way of the rotating assembly and permit more crankshaft stroke to be used in the engine, and also allows for the use of much shorter, stiffer pushrods to gain greater valvetrain stability in the process.
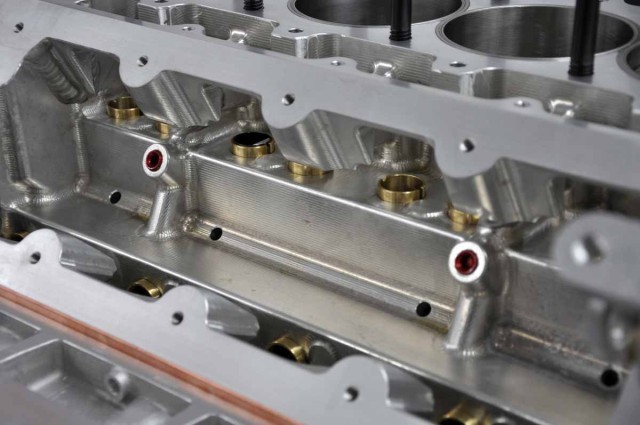
The relative strength of the LS Next2 billet block can be seen internally, with beefy aluminum everywhere the eye can see. In this photo, another view of the lifters bushings is also available, as well as the oiling circuits.
The 4.125-inch-bore billet aluminum block uses half-inch main studs, six bolts per cylinder head, a 55 mm roller camshaft, and .937-inch lifter bores. Beefy is the name of the game here — strength all around in the valvetrain to handle the stress of the supercharger.
Outfitting The Bottom End
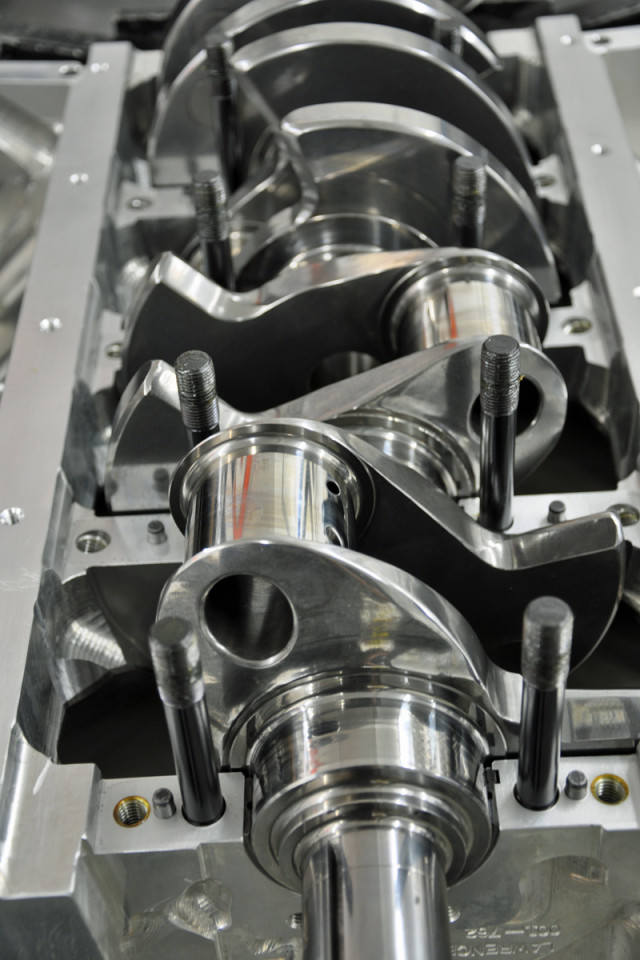
There’s no alternative way to describe the billet Bryant crankshaft; the word ‘jewelry’ comes to mind. It’s a shame this beautiful component has to be hidden within the crankcase.
The issue of strength continues into the area of the rotating assembly. The fine folks at Bryant Racing answered the call with a billet crankshaft designed specifically for this application. It uses the aforementioned 2.750-inch main bearing dimension coupled with a big-block Chevrolet diameter snout and standard LS snout length.
As this engine is using a six-stage dry sump oiling system and billet oil pan from Dailey Engineering, the extended-length crankshaft snout typically seen on LS7 applications was not required. Moroso oil pan rail spacers are required; these help the LS Next2 to mimic the dimensions of the factory LS block and allow the oil pan to bolt right up.
The crank uses a 4.125-inch stroke and 2.100-inch rod journal, combined with eight full counterweights designed to help keep damaging harmonics at bay. The connecting rods are GRP Pro Series 1201 billet aluminum pieces that measure 6.300-inch center-to-center and feature a .927-inch pin bore. Both crankshaft and connecting rods ride on Clevite bearings. One of ATI Racing‘s Super Damper harmonic dampers hangs from the snout and keeps engine vibration in check.
ARP, GRP, and Diamond Racing come together to provide the rest of the rotating assembly. The GRP Pro Series billet aluminum connecting rods ride on coated Clevite bearings, and the hard-anodized Diamond pistons are suspended on DLC-coated Trend TP-1 pins and wrapped in application-specific Total Seal M2 piston rings.
ARP‘s L-19 7/16-inch capscrews are used to secure the halves of the connecting rods to one another; the L-19 material is special in that it is a vacuum-melted alloyed steel that’s mixed with appropriate quantities of chromium and carbon to achieve a high hardness, and offers tensile strength up to 270,000 psi. The rest of the engine uses ARP fasteners in every threaded hole for durability — mains, ARP2000 head studs, damper bolt, flywheel bolts, and more.
Swinging on the ends of the connecting rods are an octet of Diamond Racing pistons and Trend Performance piston pins. The pistons have been optimized for the billet-block application and provide 10.5:1 compression in this application. They are outfitted with hard anodized tops for heat resistance, along with anti-friction skirt coating. The slugs are also equipped with lateral gas ports to keep the rings sealed up tight to the cylinder walls. Double pin oilers lubricate the Trend TP-1 DLC-coated .927-inch x 2.500-inch wristpins.
Custom Total Seal M2 piston rings are used in the top ring groove, measuring 1/16-inch, with AP Napier second rings measuring .043-inch, and 3mm oil rings in the bottom groove. This package has been developed by LME for use in high-horsepower supercharged engines such as this one.
Astute readers will begin to sense a theme here — improved strength and reduced friction. These are constant themes throughout this entire project. The engine is destined for a race car that’s competing and winning race events against some of the toughest competition in the world in the small-tire game, every single part needs to be optimized for the application. There simply is no corner-cutting anywhere in the program.
Deep Breathing
Excellent success over the years on BlownZ’s LS engines has been realized through the use of Edelbrock‘s LS-R cylinder heads — these are currently the state-of-the-art for the LS platform, and they are taken up a notch by sending them out to none other than Race Flow Development‘s Curtis Boggs to have the ports and chambers tuned up for this application.
In order to maximize performance, Boggs finalized the heads with 52cc combustion chamber dimensions. Other than the porting process to optimize the runners for this supercharged application, Boggs performs another modification that’s becoming more popular in the world of serious, heads-up racing.
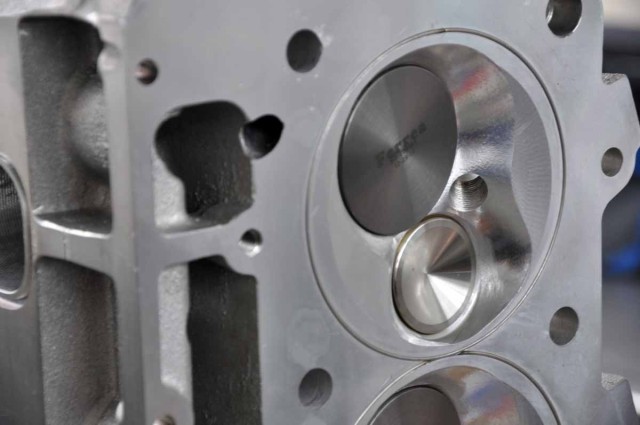
The Edelbrock LS-R combustion chamber softening performed by Race Flow Development can be seen here; it’s the shallow hemispherical cut from the outer edges of the bore towards the combustion chamber’s roof. Titanium Ferrea intake and exhaust valves are installed to combat the immense heat of the supercharged combination. RFD’s Curtis Boggs tailored the intake and exhaust ports for optimal performance. Combustion chamber volume is set at 52cc.
“Power-adder engines have a problem with pre-ignition, or detonation. The primary place where the detonation starts is in the quench area,” says Boggs.
By getting the valvetrain geometry right, you are reducing side loading on the valve stems and guides as well as obtaining all of the available lift the cam lobe and rocker ratio has to offer. — Bryan Neelen, Late Model Engines
“In a naturally aspirated engine, the quench area accelerates the flame front and helps atomize fuel in the chamber and push everything towards the center of the chamber. In a power-adder engine like this one, that’s a disadvantage. You’re stuffing so much more fuel and air into the chamber, or adding so much nitrous in those combinations, it will make the engine very detonation-prone. By softening the chamber you’re trying to slow down the flame front and reduce the chance for detonation,” says Boggs.
The induction system does not only consist of cylinder heads; a state-of-the-art aluminum intake manifold was also procured from Wilson Manifolds, designed to mate perfectly with the RFD/Edelbrock cylinder heads and provide the ultimate in efficiency.
More jewelry appears on the top side of the engine, where the combination billet/sheetmetal intake manifold from Wilson Manifolds was designed to provide balanced airflow to all cylinders. Watch for an in-depth article involving this manifold soon.
The manifold is a two-piece design, with the lower half crafted from beautiful billet aluminum and the top side consisting of one of Wilson’s traditional sheetmetal designs built to the specifications required for superior performance on this engine. The bottom section transitions from round at the top of the runners to mimic the shape of the intake ports at the bottom end. The tops of the runners have been radiused to allow smooth entry for the air as it is forced in from the supercharger.
Sealing Up The Cylinders
The custom-cut Pro Copper head gaskets from SCE have been been previously discussed in this article. The use of this design works for the dry-deck billet engine and has just one job — to keep the combustion pressure within the cylinders where it belongs. The solid gaskets feature 4.140-inch bores, .080-inch-thick construction, and cover the six-bolt design to match up with the Edelbrock cylinder heads and LS Next2 block for superior sealing. SCE’s Ryan Hunter says that the company can manufacture this type of gasket for just about any engine where a dry-deck configuration is used. The gaskets work in conjunction with an O-ring placed at the top of each cylinder for maximum sealing capability.
It’s also designed for ease of service — not only does the top half simply unbolt from the lower, it’s also equipped with a V-band connection at the manifold mount to easily connect to the inlet pipe from the air-to-water intercooler. A Wilson 123mm EFI throttle body with 5-inch V-band connector is used.
On the exhaust side, Burns Stainless and REF Unlimited stepped up to detail what was involved in creating a set of custom-fabricated stainless-steel headers to remove the massive airflow from this engine. Efficiency was the main goal during this process, and that dictated the material choice.
“Typical 1010 carbon (mild) steel conducts 219 percent more heat per foot than do the types of stainless steel we use in header fabrication. By contrast, quite a bit more heat stays inside the stainless header tubes and does not get passed into the surrounding air. By not allowing the contraction of the cooling gases as they flow down the tubes, more exhaust velocity is retained which promotes better scavenging at the collector. This retention of velocity increases the overall header efficiency,” says Vince Roman of Burns Stainless.
Some of the tips they shared during the process can be found in this article.
Valvetrain Specifics
With the huge horsepower potential on tap from this blown beast, controlling the motion of the valves is critical — if they’re open when they are supposed to be closed, then performance suffers. In order to ensure that the greatest chance for success exists with this engine program, a custom solid-roller camshaft with super-duper-top-secret specs was selected to actuate the Jesel 1.8:1 shaft-mount rockers through Trend pushrods and .937-inch Jesel offset lifters.
“LME focuses on the optimization of valvetrain geometry in every engine we build. This is one aspect of the assembly we often see overlooked. By getting the valvetrain geometry right, you are reducing side loading on the valve stems and guides as well as obtaining all of the available lift the cam lobe and rocker ratio has to offer,” says LME’s Bryan Neelen.
(Left) Measure, measure, and measure again. One item that LME prides itself on is the ability to tune up the valvetrain geometry so it's just right. (Right) Note the use of two different styles of rocker arm for intake and exhaust, and also the notches that are snipped out of the Fel-Pro valve cover gasket material for rocker clearance.
The use of different materials for intake and exhaust rocker arms has specific roots in the type of power-adder used on the engine. Aluminum rockers are used on the intake valves, but steel rockers are used on the exhaust side due to their strength and heat resistance. Although the steel rockers are heavier in total weight, they are lower in actual reciprocating weight, making them lighter at the valve. These are used because the supercharged engine tends to produce high heat on the exhaust side.
The engine is also set up to use one of Jesel’s tried-and-true belt drives for the LS Next2 block with the raised camshaft option. The camshaft belt drive uses a unique, patented High Torq Drive reinforced belt that spins with less friction than chains or gear drives, and also works to absorb the engine’s harmonics to keep the camshaft’s timing in check.
The belt drive pulleys feature externally-adjustable cam timing marks, along with Teflon-coated camshaft and crankshaft seals designed to withstand high vacuum and boost situations.
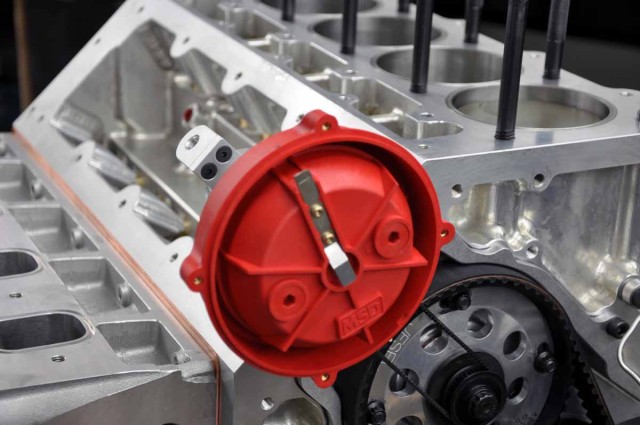
Jesel’s cam-driven distributor setup is used for optimum timing accuracy in this application. By driving the distributor with a belt from the camshaft nose, timing imprecision is minimized.
Speaking of timing, one of Jesel’s Extreme Series Distributor Drive systems has also been selected. This unique system bolts right on to the front of the engine, and uses a drive belt that’s spun directly from the nose of the camshaft. There are a number of reasons to use this unit, chief among them reducing unwanted timing retard that can happen at high RPM in the case of extreme torsional load on the camshaft. Since the distributor is driven right from the nose of the camshaft, this potential big problem is completely removed from the equation.
The cylinder heads are outfitted with Ferrea‘s titanium intake and exhaust valves; these are designed to handle the immense temperatures seen in the combustion chamber from our supercharged combination. PAC 1359 double valve springs and a complete assortment of PAC retainers, locks, locators, and shims are used to control valve motion. The 1.522-inch-diameter dual springs are installed at 450 pounds on the seat, have an open load of 1,250 pounds, and will handle up to .900-inch maximum lift, although the specifications on this particular camshaft won’t be disclosed (wink-wink). The springs are installed at a 2.200-inch height.
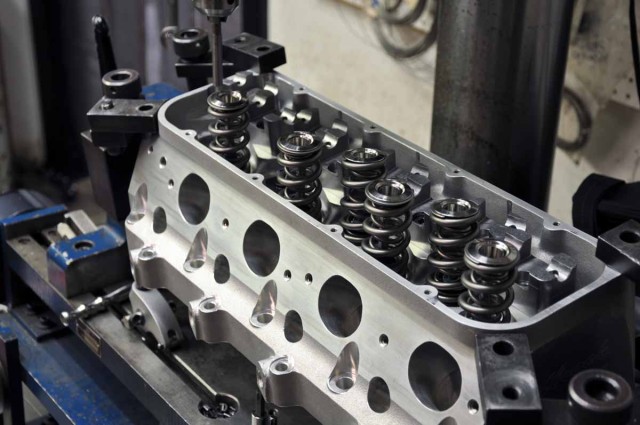
PAC dual valve springs are necessary to control the valvetrain motion in this engine; boost presents concerns not seen in naturally aspirated engines, and the springs must be up to snuff. Port volumes are, let’s say, ‘adequate’.
“We also like to physically measure the net lift of the cam during mockup. This means measuring cam lift with the actual springs, rockers and pushrods being used. This allows us to take rocker and pushrod deflection into account. Having this information on hand allows us to tweak the installed heights on the springs for optimal coil bind distance. Optimizing the spring heights can increase RPM capabilities, improve spring life and reduce spring failure,” Neelen explains.
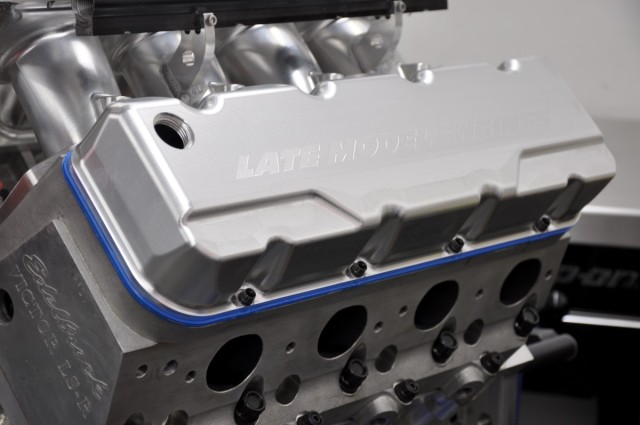
No engine of this caliber should be installed without giving thought to its appearance; to that end, the folks at Granatelli Motor Sports helped to set the engine up with a sweet set of their billet-aluminum CNC-machined valve covers, custom-engraved with the LME nameplate. These things are serious show-stoppers.
Pumping Up The Power
The aforementioned ProCharger F-1X-12 supercharger uses the latest in airflow modeling and compressor wheel development to provide the power required to run at the top of the heap in the chosen race classes where BlownZ regularly competes.
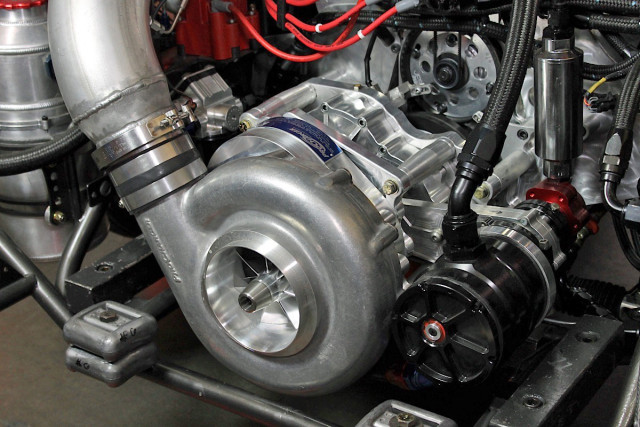
ProCharger’s F-series supercharger has proven itself in hundreds of street-car races all over the globe. The F-1X-12 used in this application has powered BlownZ to a best of 7.09 at 203 mph to date, prior to this new combination.
The F-1X-12 uses the standard F-1X impeller design and places it into a larger, 12-inch volute with 6.5-inch exducer dimensions. The company has also engineered discharge guide vanes into the design for greater efficiency and power production. The F-1X-12 was originally conceived to meet sanctioning body rules in the X275 and other small-tire classes, and has proven its performance in competition on BlownZ.
In this application, the supercharger is driven using a reverse gear drive system from Component Drive Systems, a division of Chris Alston’s Chassisworks. One major advantage to using the CDS gear drive is the capability to use many different internal gear ratios in the drive system to allow the user to over- or underdrive the supercharger to meet the target supercharger rotation speed and power output.
The CDS drive system uses a 1 3/8-inch-wide gearset for maximum strength and has a number of other sweet features, like a built-in timing pointer and crank trigger pickup mount for simplicity. There’s a built-in sight glass to monitor gear drive oil level and quality, multiple auxiliary shafts provided to drive additional accessories at crankshaft or blower RPM levels, and even accessory drives optionally available to provide alternator, fuel pump, and vacuum pump pickup points.

The CDS geardrive is well thought-out, with mounting points available to drive multiple components right from the plate, like the vacuum and fuel pump among others.
The drive hub bushings provided by CDS are made from high-density urethane that’s available in multiple durometers. These help to suck up some of the aggressive harmonics produced by the supercharger/gear drive combination and help to extend the bearing life of the system.
Although the CDS system is in use with a ProCharger in this particular application, the company also offers also kits available for Vortech and Paxton superchargers, as well as a dual-supercharger drive system that’s, simply put, a work of art. The multitude of options available with the CDS gear-drive system can’t be covered in the limited space available here; this article detailing its capabilities is a must-read.
In Conclusion
The components used in this build are the very best of the best; there were no corners cut or punches pulled during the design and implementation of this engine program. While competitive reasons prevent explanation of some details, the major components used in the build along with some of the theories behind its formation are presented here to give a glimpse into a top-shelf engine program. BlownZ is in the thick of the hunt no matter where it competes, and the engine program is a large part of that race-day success. With this newest iteration of the engine program, the BlownZ team will be zeroed in for record-setting achievements and consistent, race-winning performances.
So far the car, with this engine installed, has been a best of 4.58 at 165.9 mph in the eighth-mile on a shakedown pass, with the identical cast-aluminum version of this engine.