Our Project True SStreet Chevrolet Camaro has been taking up space in our shop for longer than we intended when we kicked the build off a handful of years ago, but that’s all about to change, as we are just days away from burning rubber with the LS-powered street/strip machine.
Our goal with the 427-inch, Whipple-supercharged machine is to click off a 1/4-mile run in the nines, and get us to and from the track if we need it to. Just because it’s a relatively mild machine, though, doesn’t mean we can’t benefit from the use of traction control. After all, high-performance production cars come right from the factory with it these days, and well…this is a street car.
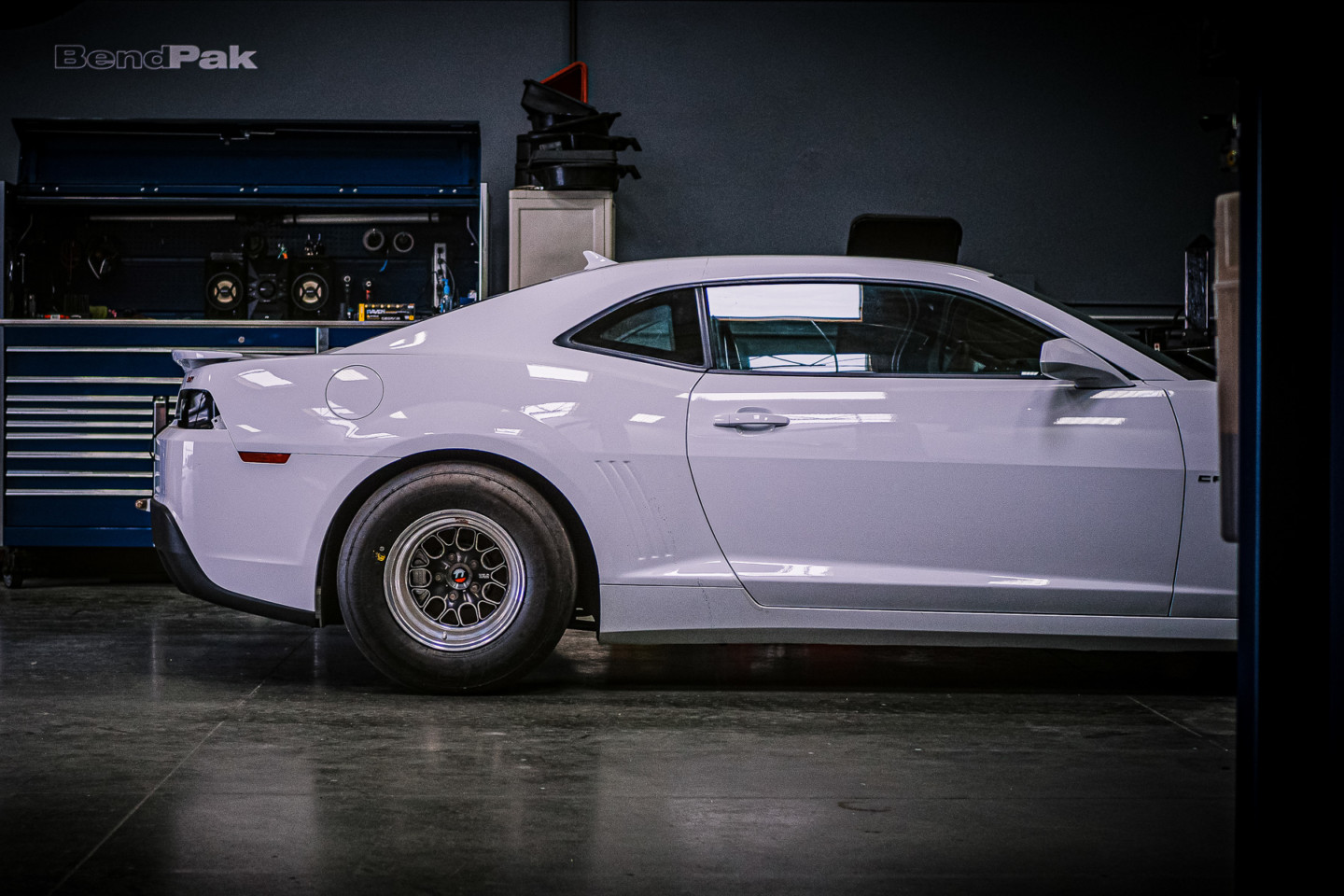
We’re down to the final nitty gritty details as we wrap up the True SStreet build and head to the racetrack.
Traction control is particularly beneficial for us, as we’ll be racing this car primarily in Southern California, where racetracks are scarce, and the surfaces we do have leave a lot to be desired. Nevermind that in the summer months — like, right now — the tracks are hot and greasy, making matters worse. Of course, we’ll be tuning the engine, the gear ratios, the AFCO front struts, JRi rear shocks, and our 4-link conversion to get us down the track efficiently, but for those moments that we miss the mark a little, Davis Technologies will be there to save our ass.
The Need For Speed
We acquired one of Davis’ TC3-SL units, a self-learning traction control system, to help us manage wheel speed in True SStreet. Davis’ TC3 (this lineup includes the base TC3, the TC3-SL, and TC3-SL Pro) was built from the ground up with speed and accuracy in mind. How fast? It samples driveshaft RPM at a rate of 1,000 times per second. Along with retarding engine timing, the unit can also drop cylinders in severe cases. But its very foundation — what traction control guru Shannon Davis hangs his hat on — is its speed and accuracy.
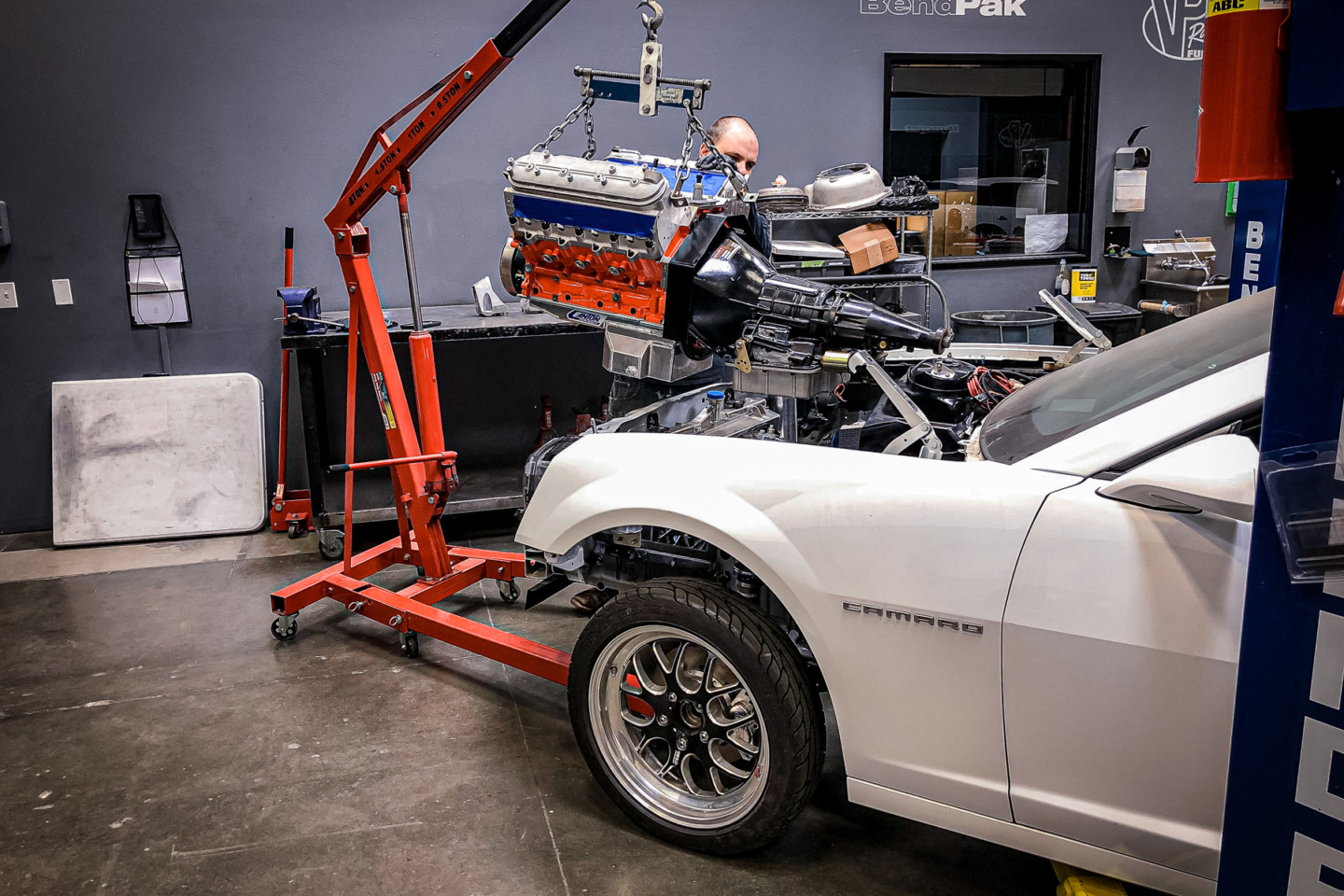
With our 427 cubic-inch, supercharged LSX dropped between the fenders, we’re on to wiring the car, including the Davis TC3-SL self-learning traction control.
“Step one to building a good traction control system is the speed at which it can measure RPM, so that we can react fast,” Davis says, adding “whether it’s front-wheel speed versus rear-wheel speed, driveshaft speed over a time plot, or driveshaft speed rate-of-change.
“Getting right down to the core of it, there’s a lot of ways to measure RPM, and some aren’t that good,” Davis continues. “If you had four magnets on your driveshaft, there’s four pulses going by, and you measure them for 1/10 of a second. And it’s going 6,000 RPM, which is 100 revolutions a second, or 400 pulses a second, in one second. You can measure the difference in 400 and 401, which is 0.25-percent of change. But if you’re measuring for one second for the resolution, it takes a second to react, to complete the measurement. So you’re a second behind. So it doesn’t take a rocket scientist to figure out that we need more magnets, because then we can measure faster.”
Davis measures 32 pulses — 32 teeth — per revolution, but rather than measure completed revolutions of the driveshaft, it is measuring only the edge of one tooth on the collar to the next. This means Davis is measuring in billionths of a second, or nanoseconds, between pulses. “At 6,000 rpm driveshaft speed, we’re getting 312,500 counts (or nanoseconds) between pulses, or the edge of each tooth on the driveshaft ring. And it can accurately process between 312,500 and 312,501,” he tells us. “So our resolution, at 6,000 rpm is 1 to 312,500.”
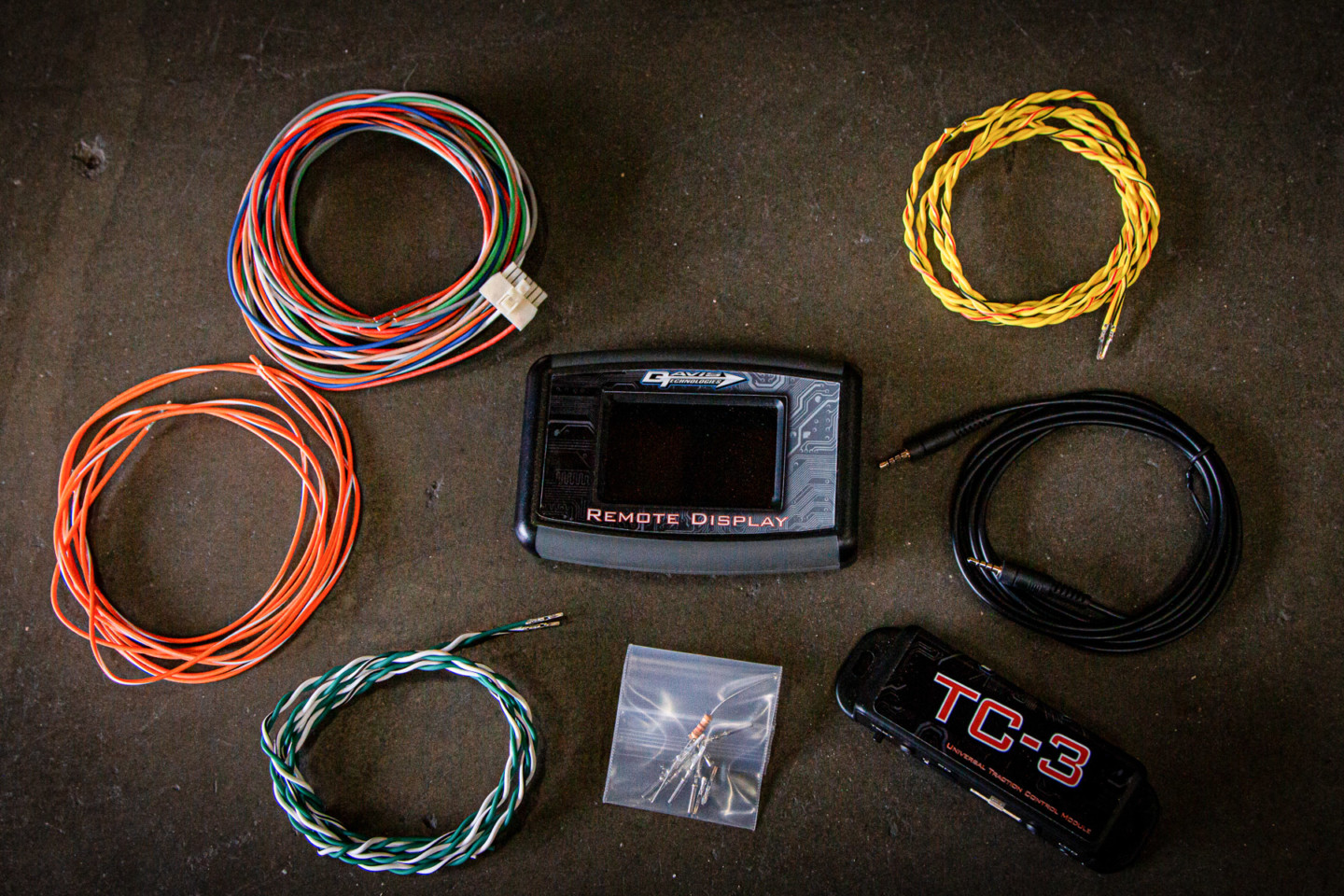
Our TC3-SL package included the TC3 unit, the optional remote display, the necessary wiring and harness, and remote display cable.
Just two wires — a signal wire for timing, and a signal wire for Smart Drop (we’ll get to that in a minute) — tell our Holley Dominator ECU what to do. The Davis box is making all the traction control calculations, and is telling the ECU what corrections in ignition timing to make on its behalf. The Holley Dominator box can react quick enough in concert with the Davis box to impact the next cylinder in line to combust. Davis laughs as he explains that the TC3 is calculating so quickly that it’s actually delivering a message via the ECU faster than the cylinders are coming by.
“We know a car is spinning. We’re sending out a command for it to retard timing before the next cylinder even has a chance to fire. Once the next cylinder comes by, we drop 5 degrees of timing and it makes a difference. We’re sitting there waiting for the next cylinder to fire, as the cylinders are 90 degrees apart. It takes two revolutions of the crank to fire all eight of them. Our speed limitation is the engine’s rotation itself. We can actually react faster on a V12 because the cylinders fire more often,” he says.
In addition to its standard rate-of-change traction control that is central to the Davis product, our TC3-SL features proprietary self-learning functionality, which takes traction control to the next level.
“The Profiler, which a lot of racers are familiar with, is a dot-plot, time-based driveshaft RPM-versus-time system,” Davis says. “It does precisely what you tell it to do. What we call traction control, or rate-of-change traction control, is monitoring the driveshaft for a sudden rate of change. If the rate of change suddenly spikes, it’s a good assumption that it’s spinning the tires. If it spikes beyond the threshold the user has set, beyond the sensitivity settings, then it makes a correction. But our self-learning traction control is learning what that rate of change is, updated every shaft revolution, and searching for a sudden deviation from the learned rate.
“If the last 1/32 of a turn of the driveshaft is faster than the average of the last full revolution, then a slip is detected.” The system constantly accounts for track conditions, tire conditions, and so on, to continually update the internal settings. These settings are updated as many as 1,000 times a second.
“So if it learns that in first gear you’re gaining 1,200 rpm per second, then 1,250 is a problem,” Davis adds. “Then, if it learns in second gear that you’re gaining 950 rpm per second and it measures 1,000, that’s also a problem. It wasn’t a problem a second ago, but it’s got an algorithm that is learning how it’s accelerating. It’s researching what it’s done in recent history, or in ancient history, like three revolutions ago, and deciding that ‘it’s been doing this, and it suddenly did this. That’s different, and we don’t want to do that.’ ”
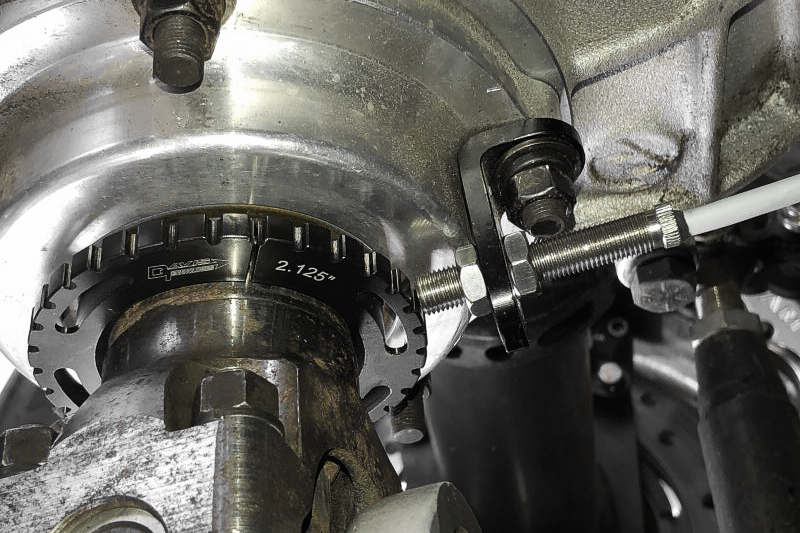
The 32-tooth driveshaft ring from Davis provides incredible speed and accuracy in the system, measured by the nanoseconds, or billionths of a second, dependent upon driveshaft RPM.
With the self-learning feature, the user doesn’t have to try to figure out the driveshaft RPM rate of change and set a “threshold,” as the system does it for you each and every revolution of the driveshaft.
The TC-3 is set up in the Davis software using a user-selectable sensitivity range (or “Mode”) of 1 through 8. By adjusting the sensitivity, the user can tune the system to correct larger slips, while not reacting to smaller, harmless slips. The algorithm then seeks a percentage of change in driveshaft RPM and adjusts according to mathematical calculations against your chosen sensitivity. The percentage of change is a proprietary, and thus top-secret, number. But rest assured, it knows what it’s doing. It then directs corrections in what Davis calls a “spread” of rate-of-change and alters ignition timing accordingly. The TC-3 can control timing to within 0.1 degrees up to 1,000 times a second.
In his example, if you have a spread of 100 (the rate at which the system reaches the maximum correction allowed) and max-retard is 10 degrees, if it spins 25 rpm, it will pull 2.5 degrees of timing. If it spins all 100 rpm, it’s going to take out 10 degrees. If it’s 101 rpm, then it enters into an optional feature called Smart Drop.
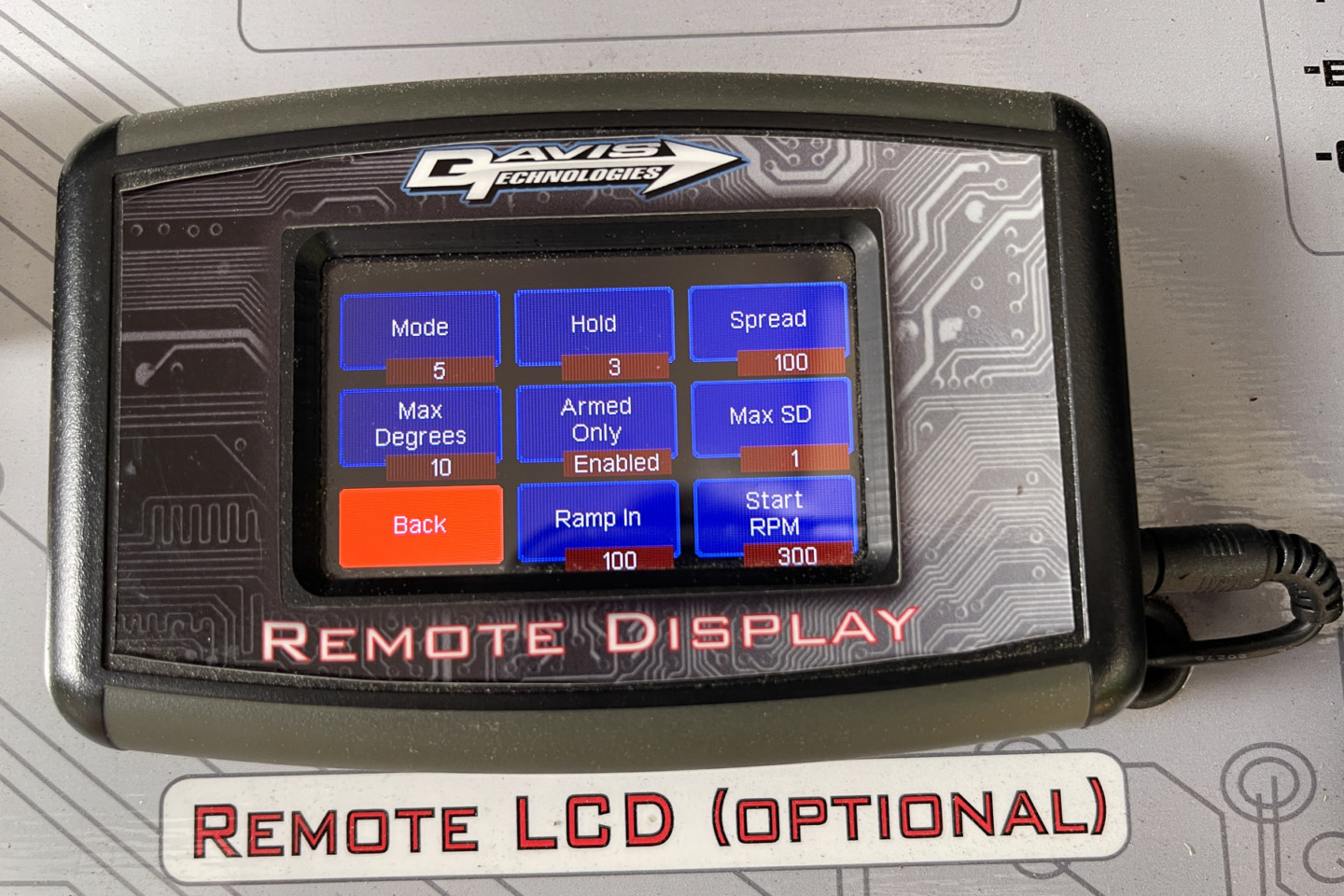
The optional remote display allows for up to six preset “tunes” to be called up and set in the TC3, even while in the staging lanes.
Smart Cylinder Dropping
SmartDrop works in unison with your ignition system to drop cylinders — to do what Davis says is “really get its attention” when tire spin becomes overly aggressive. This is cylinder dropping in an intelligent way. There are four levels — 1, 2, 3, or 4 cylinders out of 8; The TC-3 only sees the cylinders as A, B, C, D, E, F, G, and H. If you drop B (one cylinder, set on Smart Drop level 1), B is going to drop once, and is not going to drop again until it’s been fired seven more times, while each additional cylinder is dropped in the same fashion. The TC-3 does not know which cylinder is the No. 1 cylinder, but does know that if it has dropped B, then don’t drop B on the next revolution. SmartDrop level two would hypothetically drop A and D (2 of 8), and will fire each one six more times before it drops again.
If a correction is active, and the RPM spike exceeds the Correction Spread Value, then SmartDrop will be initiated. If spread is set to 150, then at 151 rpm the first level of SmartDrop will be triggered. After that, if the RPM continues to spike, the SmartDrop will increase to the next level when the RPM increases another 1/2 of the correction spread setting. So, if the spread is 150, then SmartDrop will increase every 75 rpm. The SmartDrop will only increase in level to the Max SmartDrop Limit.
So as an example, if the correction spread is 150, SmartDrop will increase every 75 rpm. So it would look something like this:
- Spike up to 150 RPM=Retard Only
- Spike of 151-225 RPM=Full Retard and SD level 1
- Spike of 226-300 RPM=Full Retard and SD level 2
- Spike of 301-376 RPM=Full Retard and SD level 3
- Spike of 377-xxx RPM=Full Retard and SD level 4
At its highest level, level 4, the engine would fire a cylinder, drop a cylinder, fire a cylinder, and so on. Davis says this arrangement allows it to be compatible with nitrous without issue, because it does not drop the same cylinder twice in a row. Thus, you’re not skipping a hole multiple times and letting it build up with nitrous or fuel.
“SmartDrop is very smooth, even on level 3 or 4. Level 2 is usually the most that is needed to control even a radial tire on a bad surface,” Davis explains.
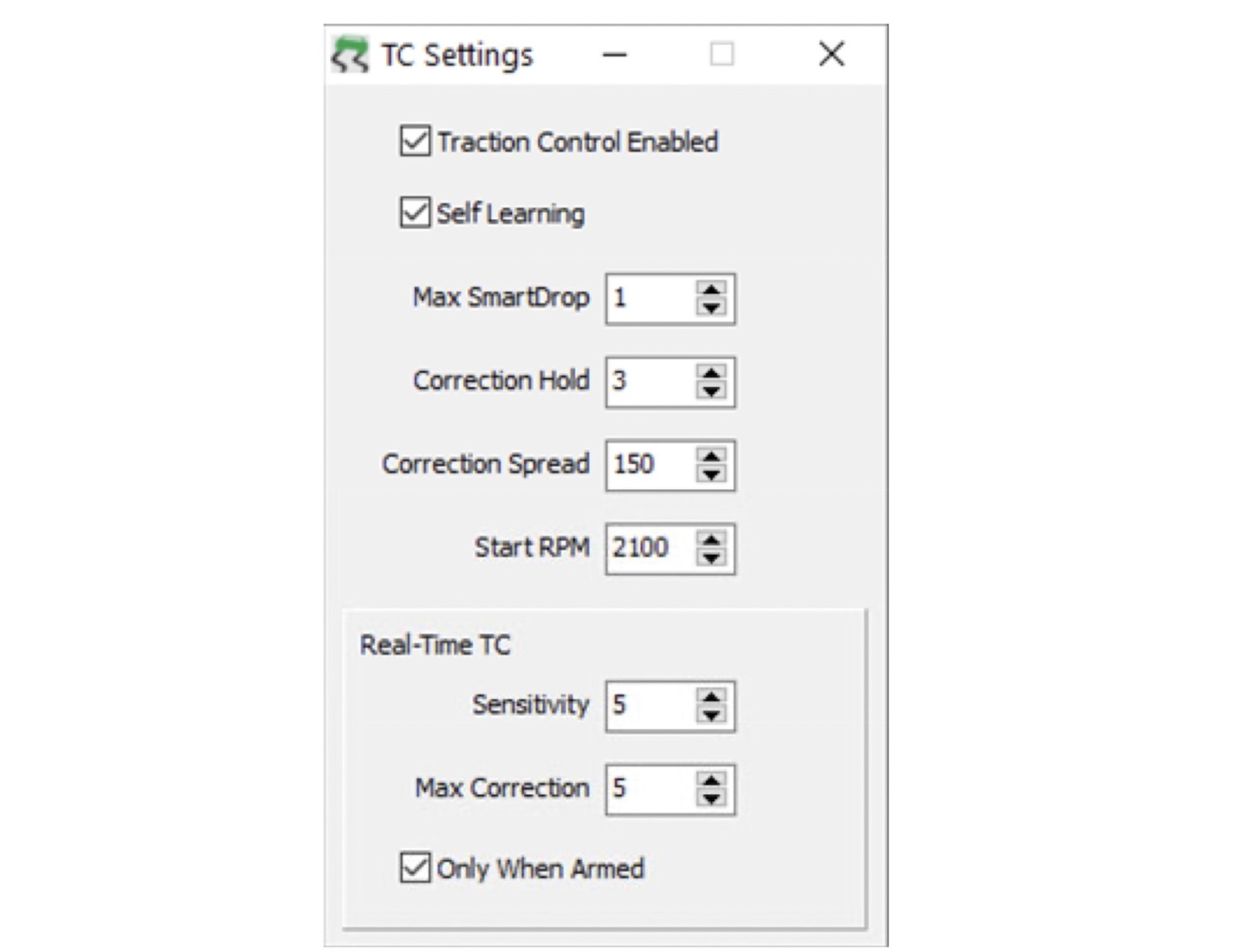
An example setup in the Davis software, including the sensitivity, maximum correction, and SmartDrop configurations.
No-prep racers have been known to utilize as many as four cylinders; Davis says a Pro Modified car on a prepped track can typically use level 1 and overcome any type of slip it would encounter. If SmartDrop is required, once the driveshaft senses the rate-of-change has returned to its acceptable learned rate, it will begin ramping back in the ignition timing that it removed.
When the TC3 is connected to a Davis Technologies Digital Ignition Controller, up to 30 degrees of timing and SmartDrop may be used to control the tire. When connected to a Holley EFI system like ours, up to 25 degrees of timing retard and SmartDrop can be commanded.
The TC3 can also be used with the Digital Ignition Controller (DIC) from Davis Technologies to control the ignition of most any type of standalone ignition system. Thus, an EFI system is not required to use the TC3 for traction control. This can be useful for updating an older race car with some of today’s latest technology. The DIC can be used to control timing and rev limiters, as well as SmartDrop cylinder dropping. The outputs from the TC3 can be used to signal the DIC to control the ignition to retard timing or drop cylinders. This signal can be analog or digital via CAN bus.
Software & Setup
The TC3-SL Pro goes a step beyond and gives the user individual control of the sensitivity and amount of retard in different sections of the track. So, one set of parameters can be for the launch, another for the 60-foot, and another from the 60-foot to the shift, and so on — the number of zones is unlimited. The TC3-SL-Pro also includes a Run Curve (a timing curve, or launch curve, where you drag the dots around and control timing throughout the run). Davis says this Run Curve is handy on something like an MSD 7AL or such that doesn’t have a launch curve built into control timing after the launch.
The TC3 uses Davis’ proprietary software; with it, one can set up all of the parameters for their traction control setup, including sensitivity (1 through 8, with 8 being the most sensitive), maximum retard, the spread (the gain, or how much percentage of slip it’s going to take to pull out the maximum amount of timing), start RPM, and ramp-in (how fast the timing is put back). This “tune” is then loaded into the TC3. The TC3 also has onboard data collection, which is saved to the SD memory card in the box itself. This collects the driveshaft RPM and the engine timing corrections that resulted. It will not, however, show SmartDrop. But, most users will typically have the driveshaft sensors connected to the ECU of choice, and all of that same data will appear in their ECU software.
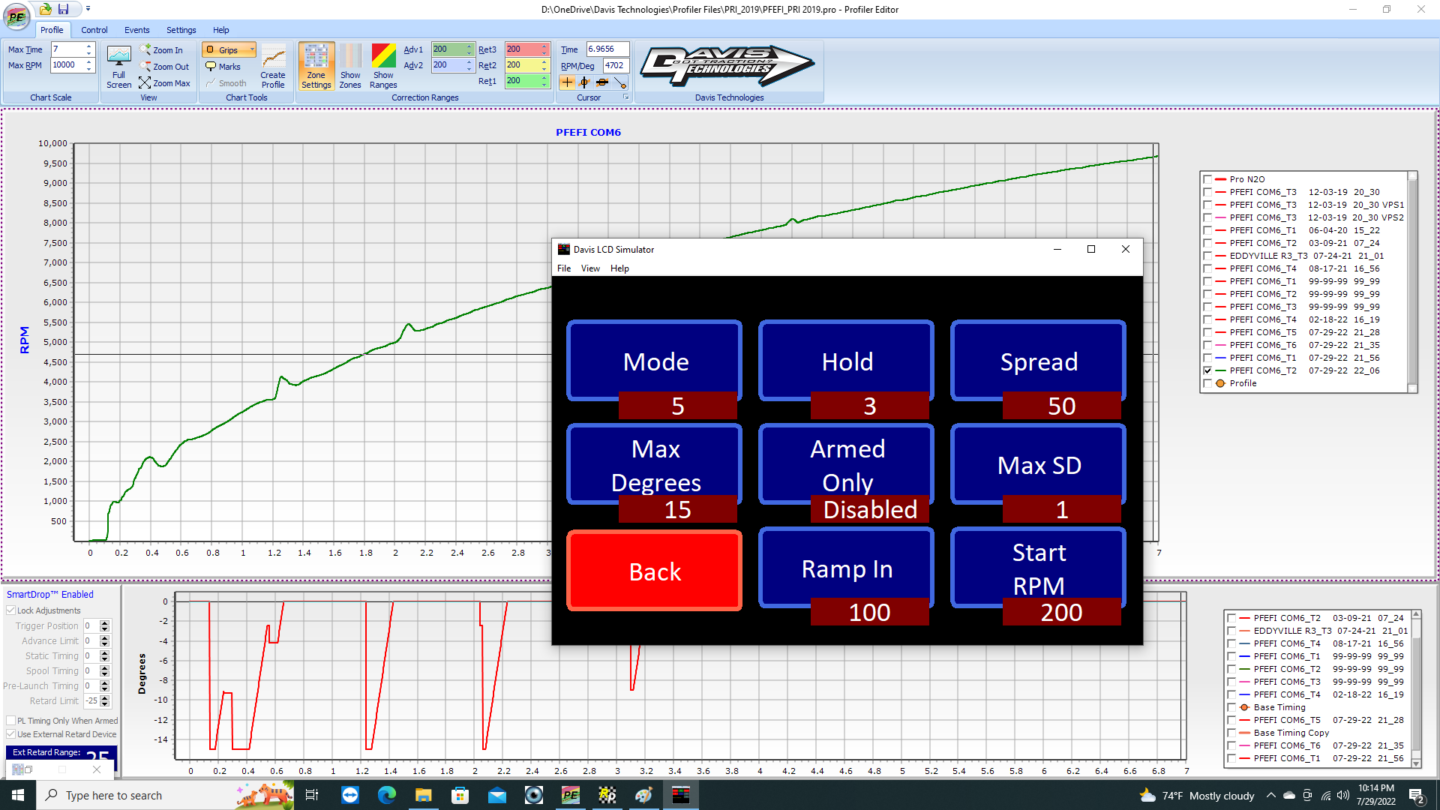
Shown here is the LCD Simulator setup screen on a laptop computer with settings for an example run. You can see the result of those settings in the graph.
Shown in the above settings screen, The Mode is the overall sensitivity of the system — the larger the setting the more sensitive, thereby making corrections on smaller slips. The range is 1-9. Hold is used to force the system to hold the correction for X number of revolutions of the driveshaft to give the vehicle some time to recover before the correction is removed. Spread controls the rate at which the system reaches the maximum correction allowed. Once a slip is detected, if the RPM reaches the top of the correction spread, then the correction will reach maximum. The correction is linear, so if the RPM spike only reaches 50 percent of the spread, then only 50 percent of the maximum correction will be allowed.
Max Degrees is the maximum allowable retard that will be allowed if the tire slip reaches the maximum Spread. Start RPM sets the RPM of the measured driveshaft below which the TC3 is not able to make a correction. This allows some cars to “get up on the tire” before any corrections are allowed. And lastly, Ramp In is the rate at which timing retard is restored after a correction has ended. Ramp in is calibrated in degrees per second; a value of 100 restore rate will take 1 second to restore 100 degrees of retard, or 1/10 of a second to restore 10 degrees. This is a linear rate, so the retard is eased back in so as not to upset the tire again.
Standard procedure for setup is to connect the TC3 box to your laptop computer via USB, complete your setup, and load it into the box. If, however, you purchase the optional hand-held programmer, one can pull up six saved “tunes” of their choosing. These are set up in the software via computer, and loaded into the box on-the-fly while in the staging lanes or anywhere away from the trailer and laptop.
Self-Learning On The Street
Davis does not recommend the self-learning functionality for normal driving, such as drag-and-drive style cars, or street/strip mixed duty like with True SStreet. When the car is cruising at a steady state on the highway, it will learn that very low acceleration and will try to react to almost any change in throttle, causing a surge. The SL systems can be placed in non-self-learning mode for highway driving and back to self-learning for the track.
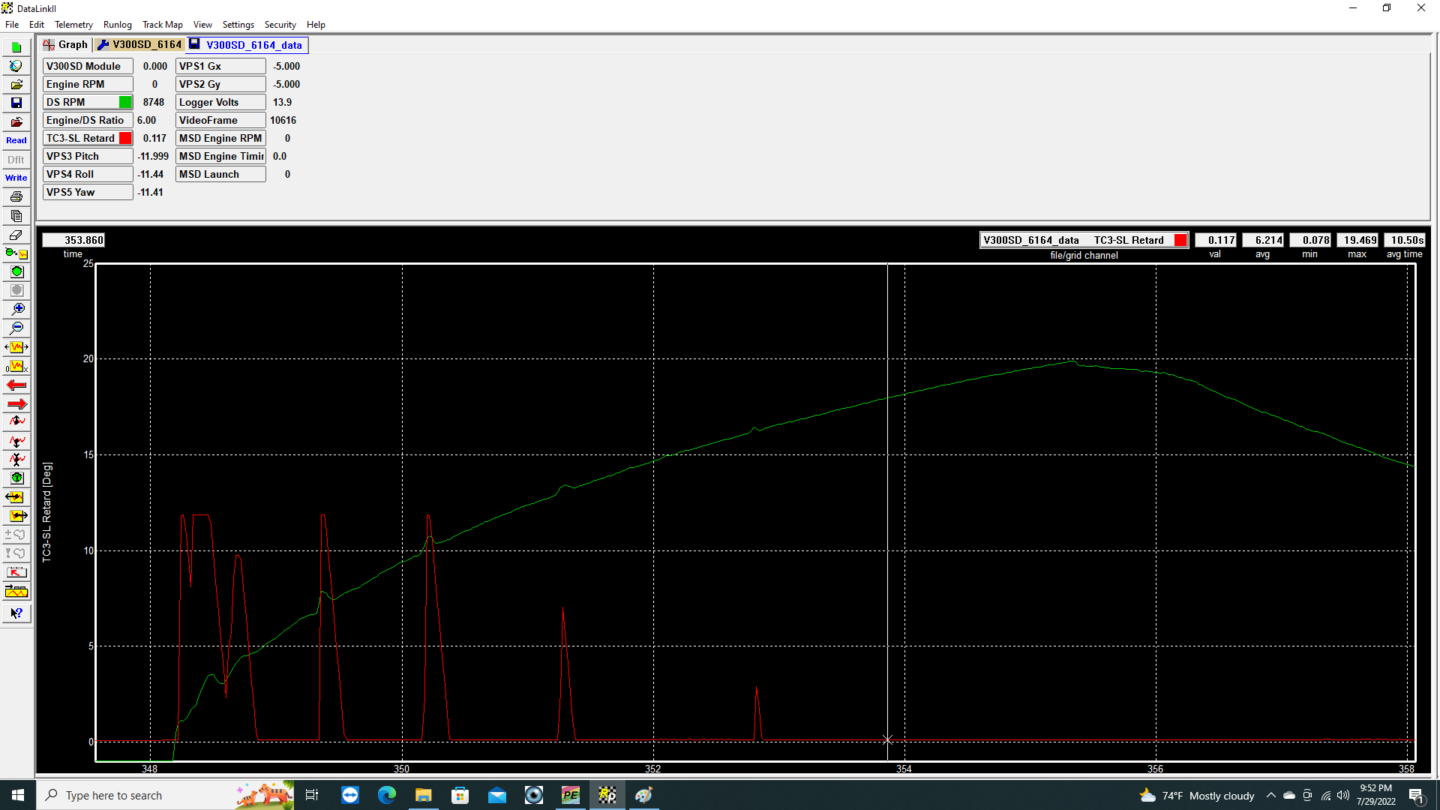
An example data graph though Racepak’s software illustrating the overlaid driveshaft RPM (green), measured in seconds, and the resulting ignition timing adjustments (red) made by the TC3.
“The self-learning features’ memory is a few driveshaft revolutions long, so if you’re cruising down the boulevard, it only knows steady-state driveshaft…it ‘learns’ zero acceleration,” Davis explains. “So any acceleration is seen as an error. It doesn’t know if the tires are spinning or not, it only knows that the driveshaft is accelerating. It’s looking at an algorithm of the last 4, 6, 8, 16, and 32 revolutions and trying to find a trend. If it exceeds a percentage set by the sensitivity, it’s going to try to correct it. It will learn the new rate pretty quickly and turn the correction off, so it’s not a huge hindrance, but for steady cruising, we just recommend turning it off. The non-self learning traction control will still help control any significant traction loss on the road, even driving in the rain.”
If you have a Davis Technologies Vehicle Position Sensor (we do not on True SStreet), you can also utilize its data in concert with the TC-3 for wheelie control.
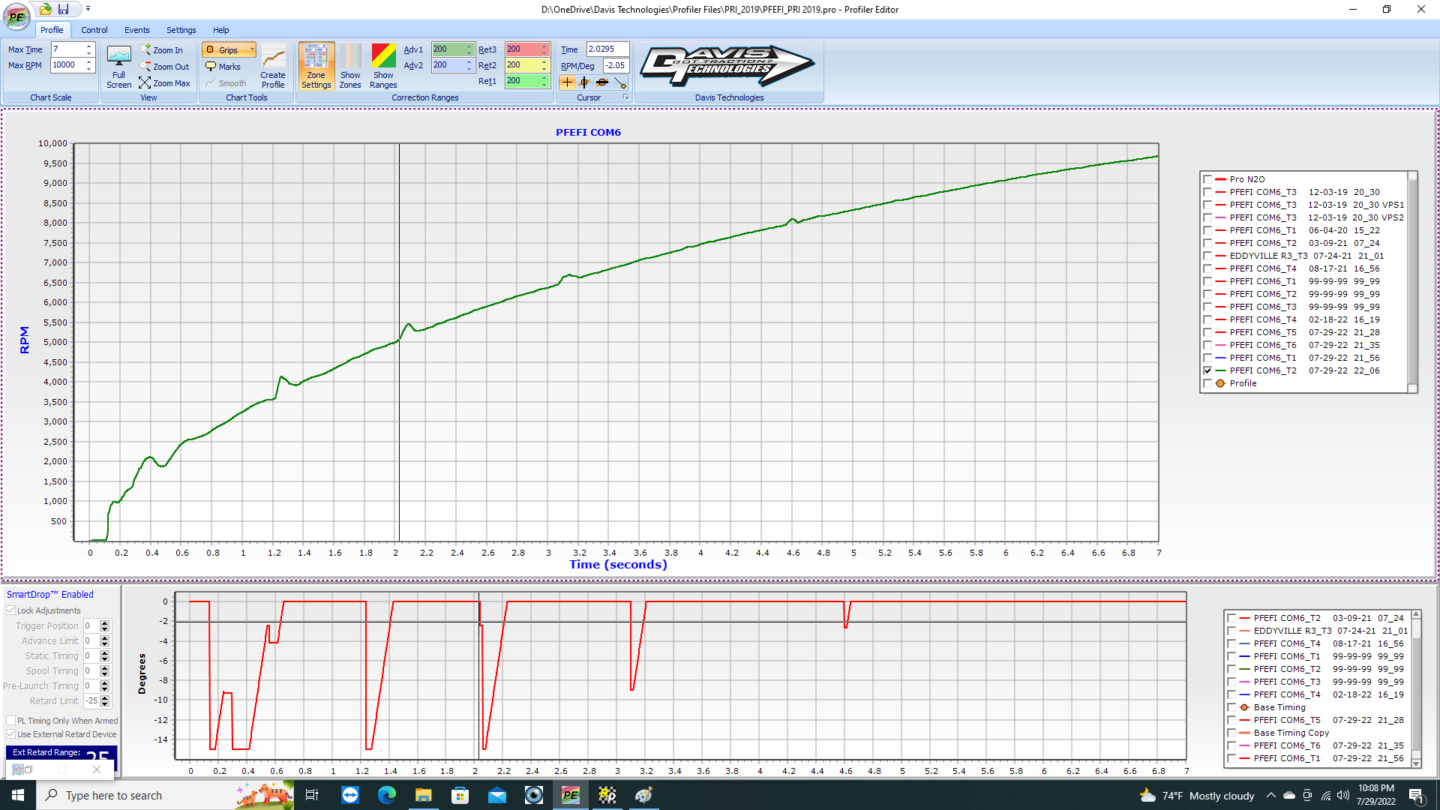
This is the same run data as above, illustrated in Davis’ Profiler software. Driveshaft RPM and ignition timing are plotted separately over the course of a run (in seconds).
The TC3 requires power and ground from the car; Davis recommends powering the TC-3 with an ignition-on power source providing 12-18 volts. A transbrake signal is required to reset the TC-3 and start a recording when released. The TC3-SL-Pro also uses the transbrake signal to start a run when using individual zone settings and the Run Timing Curve. The transbrake signal can be a positive or negative trigger. An arming switch can also be installed to enable/disable the traction control if desired; the ARM signal can be a positive or negative trigger.
Long thought to be exclusive to high-end, heads-up racing machines, Davis traction control — through its relatively affordable TC3 series of units — can improve the safety and reliability of your powerful street machines with the same speed, accuracy, and technology as those used by the pros. Keep it tuned here, as in the coming weeks we’ll be getting True SStreet on the track and gathering valuable data from, among other things, the Davis TC3-SL that we’ll be sharing with you.