Late last year, we touched on “The Whipple Difference,” which is a phrase our friends at Whipple Superchargers live by. That segment just whet the appetite of our power-hungry readers. In fact, to be quite honest, most of you wanted more — and we can’t blame you. We left you with boost on the mind, and you were craving more in-depth tech on twin-screw superchargers. Today, that craving can be satisfied.
To find the perfect size core, it’s a fine balance between computer modeling and real world testing. — Dustin Whipple, Whipple Superchargers
As you keep reading, you can expect a full download on twin-screw superchargers. We discuss some of the features and benefits of this style of positive displacement blower, as well as the pros and cons, research, design and development. It’s important to keep in mind that this column isn’t necessarily geared toward any specific make and model – though its parameters do primarily focus on offerings from The Big Three domestic auto manufacturers.
Positive Displacement
First and foremost, it’s important to note that not all superchargers are the same. We’ll keep this portion brief, but it’s worth noting for anyone wanting to know the differences between them. For all intents and purposes, there are three common styles of supercharger used today on vehicles – centrifugal, roots, and twin screw. Whipple exclusively produces the latter of those three superchargers, though we’re sure you already knew that.
“The truest definition of a screw-type compressor is a positive-displacement device with an internal pressure ratio,” Dustin explained. “It’s an internal style of compression, meaning the air exiting the compressor is at an elevated pressure before it enters the common manifold. This pressure increases as the air flows through the supercharger is described as its pressure ratio.
“What differs mainly from a roots style of compressor is that we can be more efficient any time there’s a positive pressure involved, i.e. boost” Dustin continued. “We pressurize the air prior to it entering the intake manifold, which allows less chance of leakage, and less power consumption.
“This all equates to a lower discharge air temperature, and thus a more efficient mass flow of air.”
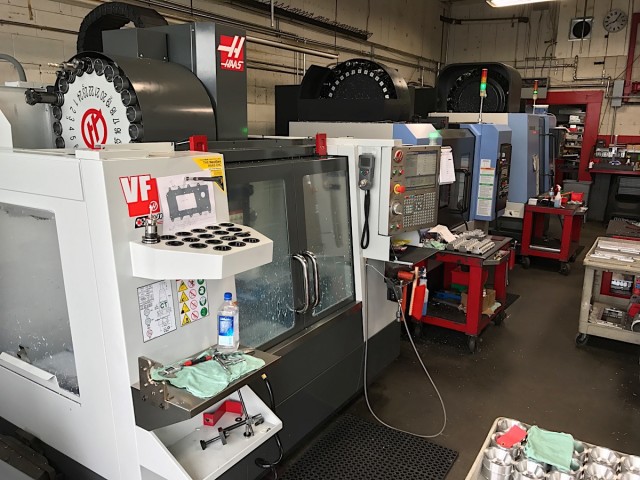
Whipple has its own in-house CNC shop where everything from twin screw rotors, to billet inlets and even billet rotor housings are machined in this facility.
Streetable Benefits
Not everyone has a full-tilt racecar, and some of us even drive our hot rods on the street. For those reasons, we inquired with Dustin about the maintenance involved in a twin-screw application.
“On the maintenance side, it’s very easy to maintain,” he explained. “The only requirement is to change the supercharger oil every 100,000 miles. Other than that, we recommend changing the belt every 20,000 miles. In terms of general maintenance on a street application, everything is pretty much the same as stock.”
Dustin did say that those maintenance intervals will depend on the application, of course.
“As far as drivability is concerned, a positive-displacement supercharger has a significant advantage you’re getting positive pressure anytime you want it,” he continued. “Just a slight dip into the throttle, and you’ll be in boost. Enthusiasts who may not have access to a boost gauge right away are unaware of this; but the daily driving fun factor is greatly increased with the positive displacement for this reason.”
Dustin said that any time you lightly enter into the throttle, there’s an under-the-curve power scenario [separate from wide open throttle] that you’ll feel.
“There’s a lot of midrange and part-throttle areas that the supercharger is working efficiently at, making the engine more efficient, and making more power – and that’s a huge advantage over any other type of forced-induction application.” he explained. “It’s a difficult area to measure, meaning the useful RPM range of normal driving – but a twin-screw supercharger tremendously increases performance in those areas, separate from even wide-open throttle. The overall performance is enhanced, and you feel like you have a much larger cubic-inch engine at any throttle input.”
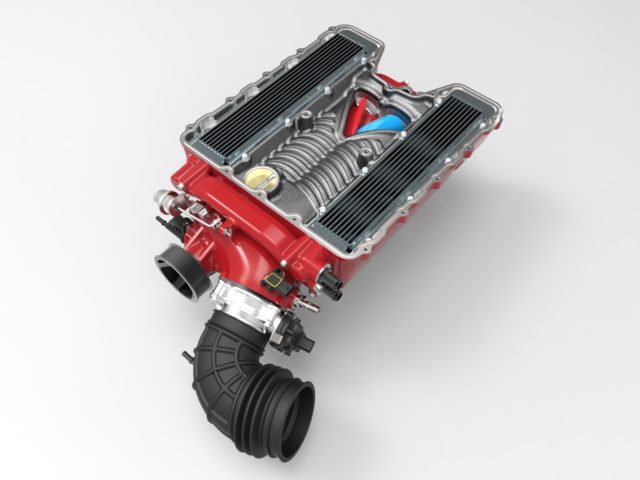
Not all Whipple units look the same, either. This is a unit for a 2016-plus Camaro SS, but the previous fifth-generation Camaro’s kit looked quite different.
While it’s obvious that your hot rod’s fuel economy could change after installing a twin-screw supercharger, it might not be as much of a decrease as one would assume. Because Whipple superchargers use a high-flow bypass valve, normal city driving, and low-RPM highway cruising, can actually mimic a naturally aspirated application quite well thanks to the bypass valve equalizing pressure above and below the supercharger, resulting in significantly lower parasitic losses.
Keep in mind, even with some of the smallest superchargers Whipple has to offer, these kits are, in some cases, nearly doubling your factory horsepower – we’d be hard pressed to say that someone wouldn’t expect a decrease in fuel economy.
Engineered Intercooling
With most types of forced induction (save for nitrous, of course) for the street, it’s a good idea to incorporate the use of an intercooler. We’re familiar with intercoolers as a device that cools the intake air, and are commonly used on forced-induction applications for both the street and the strip. This device typically cools the air that is compressed by a power adder, and in turn reduces its intake temperature, resulting in a density increase of the air supplied to the engine.
How well the intercooler works is directly related to how it’s designed, and not all intercoolers are designed the same. Our conversation with Dustin revealed that intercooler design is yet another example of that Whipple difference.
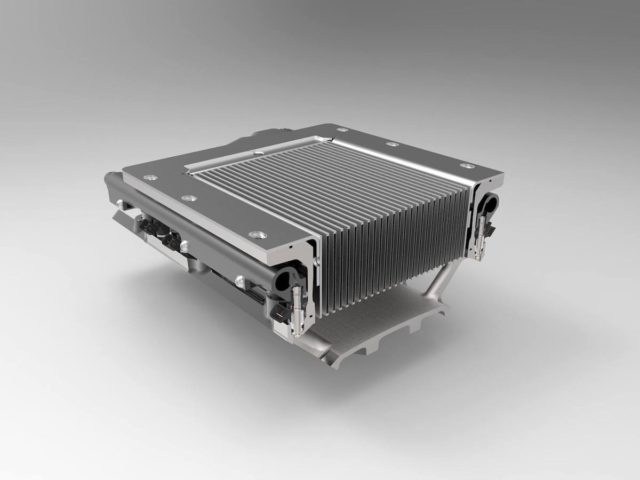
Positive-displacement superchargers like a Whipple twin-screw unit typically package an intercooler directly under the compressor screws.
“One aspect that dictates power is how cool you can keep the air charge coming into engine from the compressor while limiting its pressure loss. Separate from supercharger efficiency, the intercooler is the second key component to the supercharger system,” Dustin told us.
Whipple pays a lot of time and attention to the flow of air above the intercooler. The air exits the compressor from a relatively small area and managing that discharge air is key to maximizing the intercooler’s effectiveness.
According to Dustin, that air does not come out as an even flow over the core, which is why Whipple spends a tremendous amount of time developing its intercoolers. The amount of spacing that's required above the core is one factor, but the shape of the discharge plenum, will also dictate what is the best distribution on top of the core. After that, Whipple determines the actual size of the intercooler.
“We always maximize the size of the core without sacrificing efficiency,” Dustin told us. “From previous calculations as well as additional testing, we shoot for the maximum surface area, along with the maximum depth, to fit the largest core possible without affecting flow.
“There is a point where, if you go too big, the pressure drop will require more energy to push the air through than the energy losses from running at a slightly hotter temperature,” he added.
“To find the perfect size core, it’s a fine balance between computer modeling and real world testing. A good example of this is the S197 and S550 Mustang, where we were able to get a 33% larger intercooler core than our competition, and greatly increasing cooling potential. With the front feed inlet, we were able to design a more efficient manifold as well as the plenums above and below the intercooler.”
Compressor Sizing
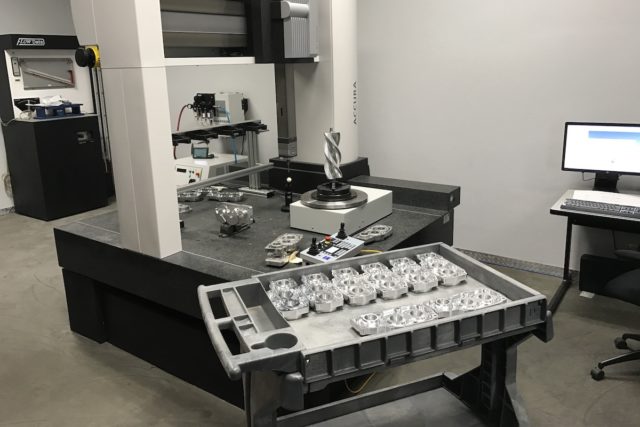
Dustin told us that the company’s CMM measuring machine is used to inspect its rotors to exact specifications, holding tolerances well within 50 micron from design. The rotors are inspected before and after machining, as well as after coating in batches. In regards to rotor cutting, Dustin said, “We brought rotor manufacturing and rotor development in-house in our climate controlled rotor room. With in-house manufacturing, we are able to develop new technology at a much faster rate. We’ve been developing some new technology for the past few years, and we’ll be releasing additional information very soon. We currently have two new generations coming, and many different sizes. The new rotor development is also for private label and applicable to OEM applications, something will be seen in the very near future.”
It’s important to remember that every kit Whipple designs is specific to that application – meaning nothing carries over from platform to platform. Whipple continues its quest for the highest flow possible by maximizing the most power available on pump gas first, and that starts with the correct sizing of the inlet and screw compressors.
What the company believes separates Whipple from its competition is that they incorporate an “oversize” attitude toward every component used in its kits. This means that, if Whipple can make a gain in power of just five horsepower using an alternative design, without sacrificing any efficiency, they will incorporate it into the final kit.
“On the inlet size, we typically use data calculated, as well as real world testing, to maximize its final size,” Dustin said. “The goal here is really to never truly hurt the flow coming out of the compressor, throughout the compressor’s range. For example, if you only want to make 500 horsepower today, you have the confidence of knowing these blowers are designed with a 1,000 horsepower inlet system in mind, built right into the whole package. We try to maximize the flow by matching the inlet size directly to the compressor size that we incorporate into that system.”
On the compressor side of things, Dustin told us it’s a similar fashion. Whipple’s goal is to ensure that the compressor is correctly sized for a specific engine, and to make sure that it’s in its “sweet spot” throughout the entire operating range.
“We try to incorporate the largest compressor size possible, without undersizing or oversizing it, to give you power at all times. If you oversize a supercharger, you may sacrifice some low end power. You may stay at the same horsepower (or slightly less) at the top of the RPM range. If you incorporate an undersized compressor, you’ll typically pick up low end torque, but lose horsepower — so what we’re really trying to achieve here, is a perfect balance of what the vehicle can take, and power and torque throughout the entire curve,” Dustin said.
Adiabatic Efficiency Explained
Terms like adiabatic efficiency (AE) and volumetric efficiency (VE) are thrown around a lot when discussing the different types of forced induction, but what exactly do they mean? In regards to a compressor, adiabatic efficiency is defined as the ratio of work output for an ideal isentropic compression process, to the work input to develop the required head. That might sound like a lot of mumbo jumbo, so we asked Dustin how exactly it works, and how it’s measured.
“There are two measurements here – volumetric efficiency and adiabatic efficiency,” Dustin explained. “VE in a nutshell is if a compressor is 3.0 liters, and that compressor is working at 100-percent efficiency, that compressor will flow 3.0 liters every single revolution. As VE levels decrease, you have to spin the compressor faster to try and get the same airflow out of it. VE is very critical on the airflow side.”
Adiabatic efficiency on the inlet side is the next step in the equation. Dustin told us that it’s somewhat easy to calculate if you have a true mass airflow reading – you could easily calculate the airflow, and the compressor efficiency.
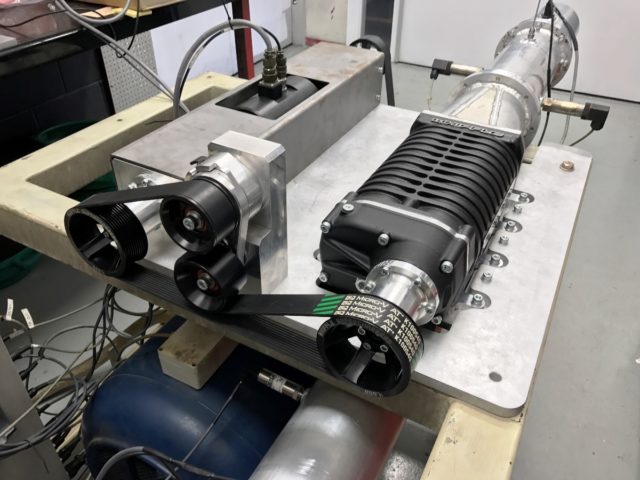
Whipple spends countless hours on a supercharger stand measuring everything from IATs, VE and AE to determine the correct size of the components used to create one of its supercharger packages.
“That compressor efficiency is just one part of the equation. The inlet system is the other part of it, because you could have a compressor that, on a supercharger testing stand, will flow X amount; but then, if you put a bad inlet on it or a bad throttle body, it can’t get the correct incoming airflow from the air box, and your effective VE will decrease drastically,” he explained. “The lower the VE is, the lower the AE is on the compressor side. This is because the system is having to work harder to move the same amount of air. We spend a lot of time on VE to ensure that the compressor flows as much volume as possible. That in turn keeps the compressor speed down, lowers the power consumption and the intake air temperatures.”
According to Dustin, the front feed design is something Whipple developed to minimize inlet losses typically associated with rear-feed supercharger systems. The front feed system reduces losses by limiting the bends, kinks and pinches typically associated with rear feed types. “We also have the ability to increase the plenum volume for better rotor filling, helping volumetric efficiency to stay near peak.”
Taking Your Temperature
In most cases, IATs are measured at the mass airflow sensor inside of the air intake, but Dustin said this isn’t the most accurate way to measure them. According to Dustin, finding the difference between the temperature at the MAF and the air post-intercooler, is the most accurate way of measuring them.
“Almost always, we incorporate the IAT sensors post-intercooler,” Dustin elaborated. “Therefore, we have the actual temperatures entering the combustion chamber. The other part of that is, in a lot of our systems, we have the advantage of being able to rewrite Ford’s software to allow us to run two sensors. We’ve run one sensor on the inlet side at the MAF where the air is being taken in, and another sensor post-intercooler – so we’re actually able to get the Delta between the two.”
This method allows Whipple to do far more with its calibration; whereas alternative aftermarket versions will require you to pull the sensor from the mass airflow sensor and direct it into the manifold, giving you only a singular reading.
“You won’t have variance with this method,” Dustin said. “These readings help us set more safety standards, and allow for more timing safely. Having the Delta between the two allows us to tune more aggressively, yet stay conservative enough to be in the ‘safe zone’ for tuning.”
Postitive Differences
You often hear others comparing roots-style superchargers to twin-screw iterations, and it’s easy to see why. Both of these supercharger versions are similar in appearance, and even construction – but that is where the similarities end, as Dustin told us.
“The main differences basically boil down to two things – the first being temperature,” he said. “In generic terms, the roots style supercharger has a hotter discharger temperature. So, as manifold pressure increases, the Delta between a twin screw compressor and roots gets greater.
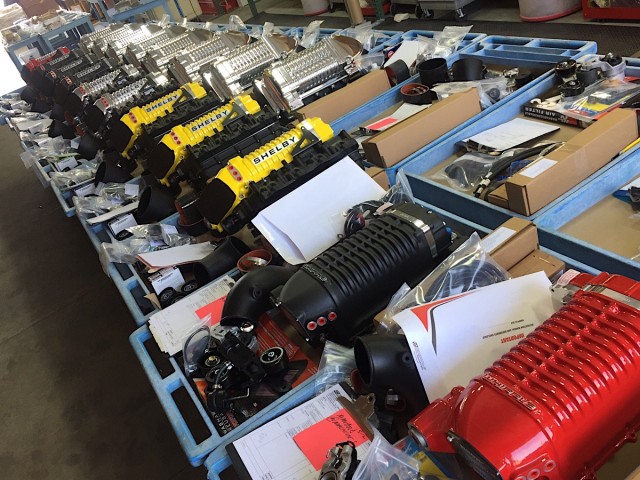
Cars like the Mustang Cobra Jet and the Shelby Super Snake utilize Whipple twin-screw superchargers out of the box.
“In turn, what you can typically do with timing and air/fuel ratio on a twin screw style of supercharger, is less as the RPM and timing increases on a roots style. The longer you’re on the throttle, and the longer it’s in boost, the higher the temperature will rise with a roots-style blower, so long as all parts are equal,” Dustin elaborated. “That typically means that the roots blower would fall off on the top end because the temperature is ever increasing. Of course, part of the equation is when it’s leaking more, it’s taking more power to drive – it’s a direct relationship between temperature and power consumption. The parasitic loss and the temperature will grow as the RPM is increased.
“The second is leakage. With the roots not having internal pressure, the leakage is much greater, meaning its specific power is higher than a twin-screw. The higher the leakage, the more energy it will take to flow the equivalent air as a properly sized twin-screw,” he added.
Conclusion
From concept, design, test and manufacture, we’ve learned that our friends at Whipple Superchargers are quite literally a one-stop-shop for everything forced induction related, and that doesn’t stop at just a “kit” level. As Dustin reiterated to us, these kits are designed to each vehicle platform specifically, and are meant to grow with an increased power level as enthusiasts continue to modify their cars. We’ve learned what Whipple’s definition of efficiency is, and we’ve learned how its twin screw superchargers fare against the current competition in the world of modern superchargers. That leaves us with one question – what’s in store for the future of Whipple?
“We are almost complete with our 2018-plus Mustang and F-150 supercharger kits, which is a whole new kit for us due to the engine change. We’re using an entirely new supercharger design including a new rotor profile for an entirely new supercharger system, which will include a new calibration as well. Everything is virtually new with this kit, and almost nothing has carried over.”
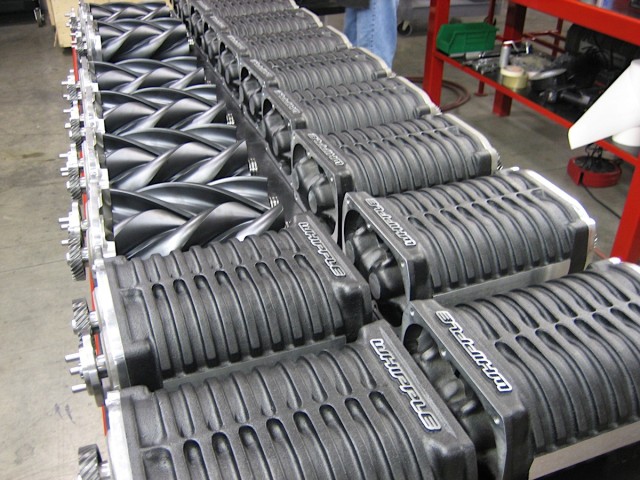
Blue Oval enthusiasts keep an eye peeled in the near future for a tech article on a Whipple supercharger install.
Dustin also relayed that the third generation of superchargers is coming quickly. “We’ve made some small steps from Gen1 to Gen2, but Gen3 is a much more significant step,” he said. “With the addition of in-house manufacturing, use of much more powerful software, CFD and key engineering, the next evolution is impressive. If that’s not enough excitement in one sentence, a fourth generation is already in the works. For GM enthusiasts, the company’s Camaro, CTS-V, and ZL1 kits are now available,” he concluded.
And finally, for Mopar enthusiasts, you can crank your Hellcat up to a massive 4.5-liter supercharger system, which uses the new third generation rotors that feature a significant increase in efficiency. For more information on Whipple Superchargers’ systems, we invite you to checkout its website for yourself.