Project 899’s stated goal of running 8.99 or quicker in the quarter-mile may seem easy, but to achieve that goal, the Camaro needs a suspension that works. The car did come with some aftermarket suspension parts, but they weren’t optimized for drag racing. We worked with the team at QA1 to select the right suspension parts to make Project 899 hook-and-book at the track.
The Right Parts For The Job
QA1’s Level 2 Drag Kit for the 1967-1969 F-body was the perfect fit for our front suspension needs. This kit comes with QA1’s front double-adjustable Pro Coil System shocks, upper control arms, lower control arms, tie-rod adjuster sleeves, a thrust bearing kit, and a spanner wrench. The great part about this kit is that it bolts right up to the OEM suspension locations, is adjustable, and comes with springs that are designed to work with small-block Chevy and LS/LT combinations.
We used everything that QA1 had in its catalog for the 1969 Camaro.
The Camaro’s rear leaf-spring suspension was augmented by a beefy Strange Engineering rearend, but it still needed some shocks to complete the package. QA1 makes a set of double- adjustable shocks that are a direct fit for the 1967-1969 F-body, so we picked up a set of those for the build from Summit Racing too. These shocks will give us plenty of adjustment options at the track.
Why We Selected These Parts
As mentioned earlier, the aftermarket suspension the Camaro came with would be fine for a street cruiser, but we needed something that could make the car work at the drag strip. QA1’s Level 2 Drag Kit came with everything we needed to address the front suspension of Project 899 in one package. Let’s dig into why this kit fit our needs so well.
The bushings installed in the QA1 control arms are infinitely better than what the OEM units use. These bushings are made of a composite material and don’t produce much friction. The bushings create an environment where more movement is allowed at the pivot point of the control arm. So, that lets the control arm to move freely, and help maximize the weight transfer to the rear wheels thanks to the reduced resistance these bushings provide.
The bushings that QA1 uses in these control arms play a critical role in how the suspension performs. Since these are low-friction bushings, that allows the control arms to move freely and make the suspension very responsive.
QA1 designed the control arms to have more caster built into them versus the OEM parts that came on the car. The additional caster is going to give you more straight-line stability under hard acceleration. Each control arm is made of high-strength steel that enables thinner wall construction, thus reducing the weight of the control arms. According to QA1, the upper control arms weigh less than seven pounds per arm, while the lower control arms clock in under 10 pounds per control arm.
The upper control arms come with an integrated droop screw. This screw is an outstanding suspension tuning tool because you can use it as a travel limiter that prevents the shocks from fully extending. You can also use the droop screw to control how much weight is transferred to the rear tires when the car launches. These screws also eliminate the need to add a set of travel limiters to the front suspension.
Steve Smith from QA1 explains why these droop screws are such an important tuning tool.
“You only have so much travel available. You don’t want the arms resting on the frame on the droop stops. This integrated droop screw prevents the upper control arm from laying on the frame on the droop stop, or the shock from being at full extension. If you’ve got a car that’s working well and don’t need a ton of transfer, you can lock this adjustment down.”
The team at Big 3 Racing is highly skilled at building anything, but their job to assemble the front suspension was made easier thanks to the design of QA1’s parts. QA1 works hard to make sure that its parts install like they are factory units.
“We put a lot of thought into the manufacturing process of these control arms. They have exceptional quality, which makes them easier to install. The control arms are welded together in a jig, and test fit in a jig prior to powder coating and final processing. Once you start welding on a control arm, they can distort or move around due to the heat. That’s why we use jigs, to prevent the control arms from falling out of spec,” Smith says.
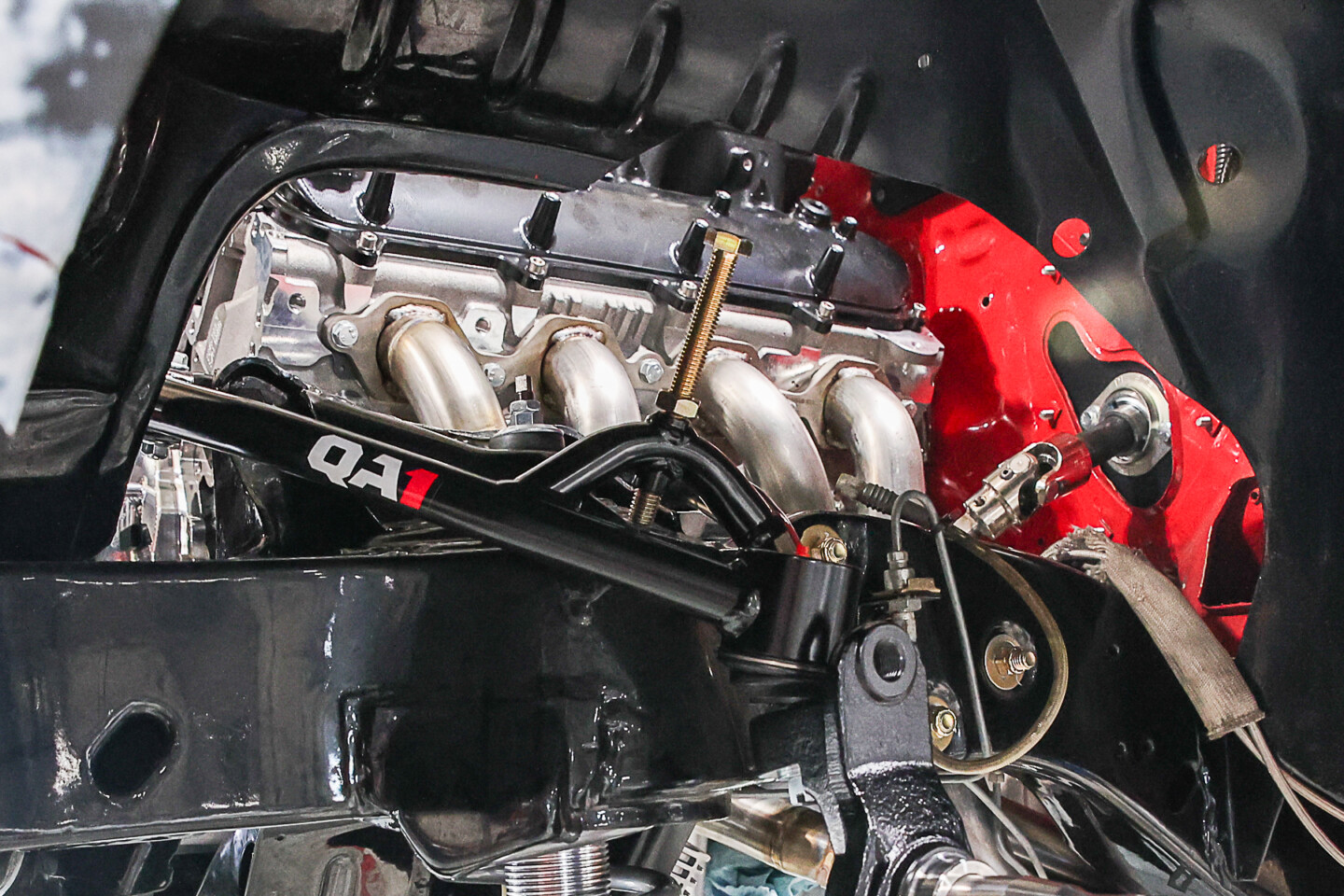
The integrated droop screw on each upper control arm will give us more suspension tuning options at the track.
If you have a set of double-adjustable shocks up front, the integrated droop screw is really important. You want to have the ability to adjust the shock’s rebound more, so the adjustable droop screw gives you that option since it gives you more of a window to tune the shock.
“If you’ve got a double-adjustable shock, and you’ve got the rebound cranked all the way up trying to limit the upward motion or a wheelie, this adjustable droop stop can be another tool you use to try and get the results you want. You’ve got a couple of things in play when a car goes wheels up. If you’ve got control over the rebound in the shock, and this adjustable droop limiter on the upper control arm, that gives you two tuning tools for the front suspension,” Smith says.
Let’s talk about double-adjustable shocks and why we went with them for this build. There’s one word that sums up the reason we used double adjustable shocks: control. A double-adjustable shock allows you to control both the rebound and compression of the shock. That means you can make adjustments based on how the car is performing, the track conditions, and how you’re applying power too.
QA1's double-adjustable shocks provide numerous tuning options.
“If you’ve got a single-adjustable shock and the car is coming up the way you wanted, but it’s coming back down hard, you can only adjust for one of these things. The double-adjustable allows you not only to control how the car comes up, but also how it’s going to come down. You can set up how the front suspension comes up independently of how it comes down, so you get the best of both worlds when it comes to adjustments. This means you can make adjustments to one, and not have a negative impact on the other,” Smith explains.
Since Project 899 is still a street car at heart, and will be driven to the track, double-adjustable shocks are a great choice. You basically get two shocks in one that will work at the track or on the street. All you need to do is figure out what settings work best for each situation and make adjustments as needed.
“These shocks will work great on the street or the track. You can soften the compression to absorb imperfections in the road. The rebound can be stiffened up to give you the ride you want on the road. You have the ability to dial in the type of ride you want on the way to the track, and then adjust the shocks to hook as much as you need while racing,” Smith states.
The double-adjustable shocks are great, but you still need the right springs to unlock all the performance advantages they can provide. This is where working with QA1 really pays off, they made sure we got the right suspension and spring package for our application.
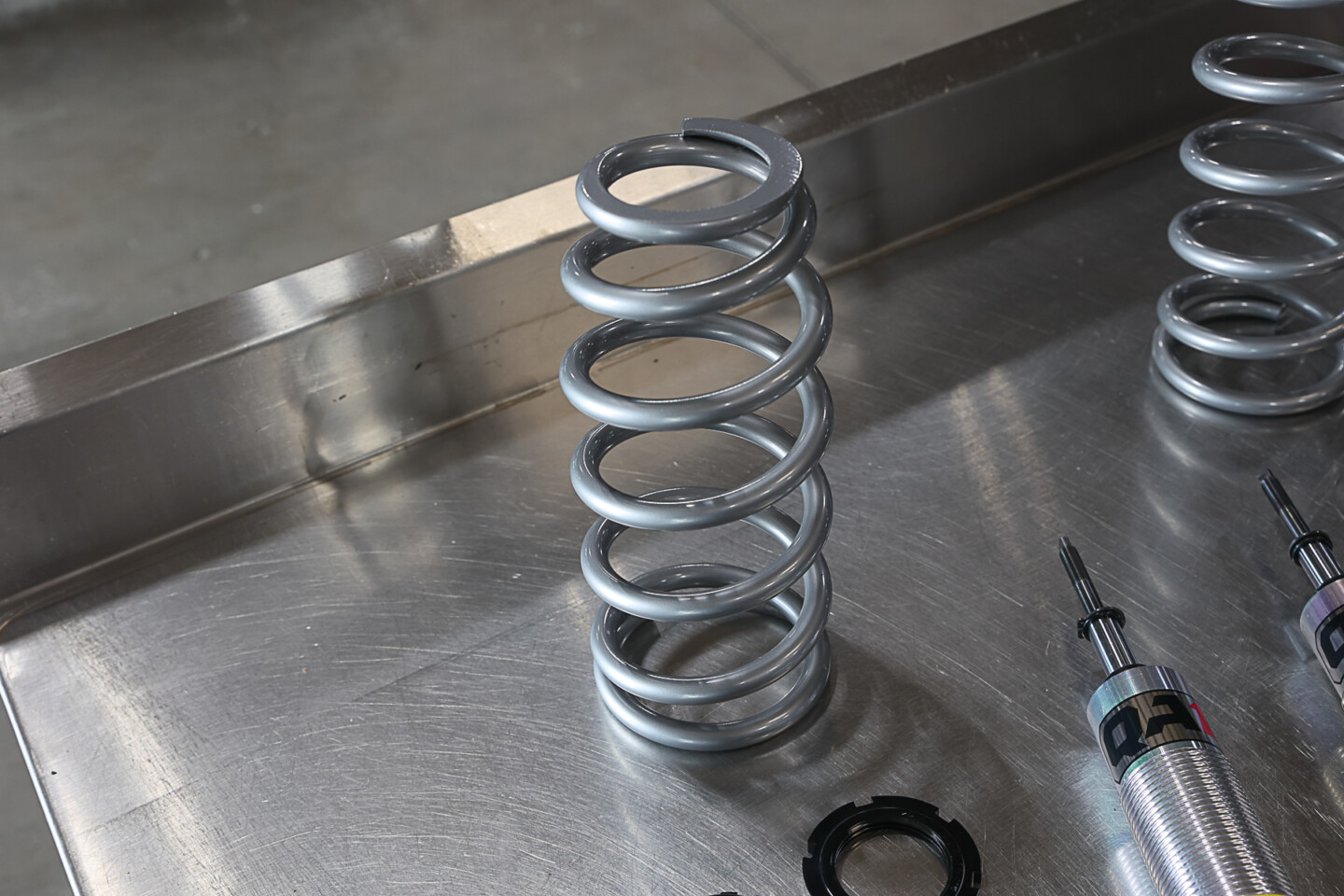
The soft springs QA1 sent are going to help transfer weight to the rear tires when we hit the track.
“We send the drag racing kits out with certain springs to maximize performance. The softer spring rates help with stored energy and getting the front end up in the air. That’s why we use a softer spring in these kits. It gives you more stored energy and helps the front end pop up easier,” Smith says.
A suspension that’s set up for drag racing is going to help Project 899 achieve its ET goal of 8.99 at the track. The QA1 suspension parts we picked up from Summit Racing are going to really help us accomplish those goals and hopefully more.
As part of our 30 days of Project 899, we will be bringing you in-depth tech content on the engine build, transmission, rearend, suspension, and coverage of the entire build going together. There will also be video content showing the entire nine days of the build including commentary and explanations from our team, bloopers and outtakes, and hurdles we encountered that had to be overcome to meet the deadline. If you haven’t already, follow LSX Magazine on Facebook and Instagram, and subscribe to the Power + Performance YouTube Channel to catch all of the Project 899 content we have coming.