General Motors has built some great things for us over the years. They’ve been known to innovate and make engines with massive power. However, over the years they have also been known to build rearend assemblies that turn into spaghetti at the race track. Well, we can’t all be perfect and the ol’ General certainly isn’t perfect. He did manufacture the Pontiac Aztec. But, we are here to talk about a different Pontiac, a Trans Am, with a notoriously weak rearend in it. The plan for this car is to head to the track and make laps, not to make metal spaghetti with the rearend. So how do we solve this problem? With a Ford-designed part (I’m sorry to say to you GM faithful) and some help from our friends at Moser Engineering in the form of their MusclePak rearend assembly.
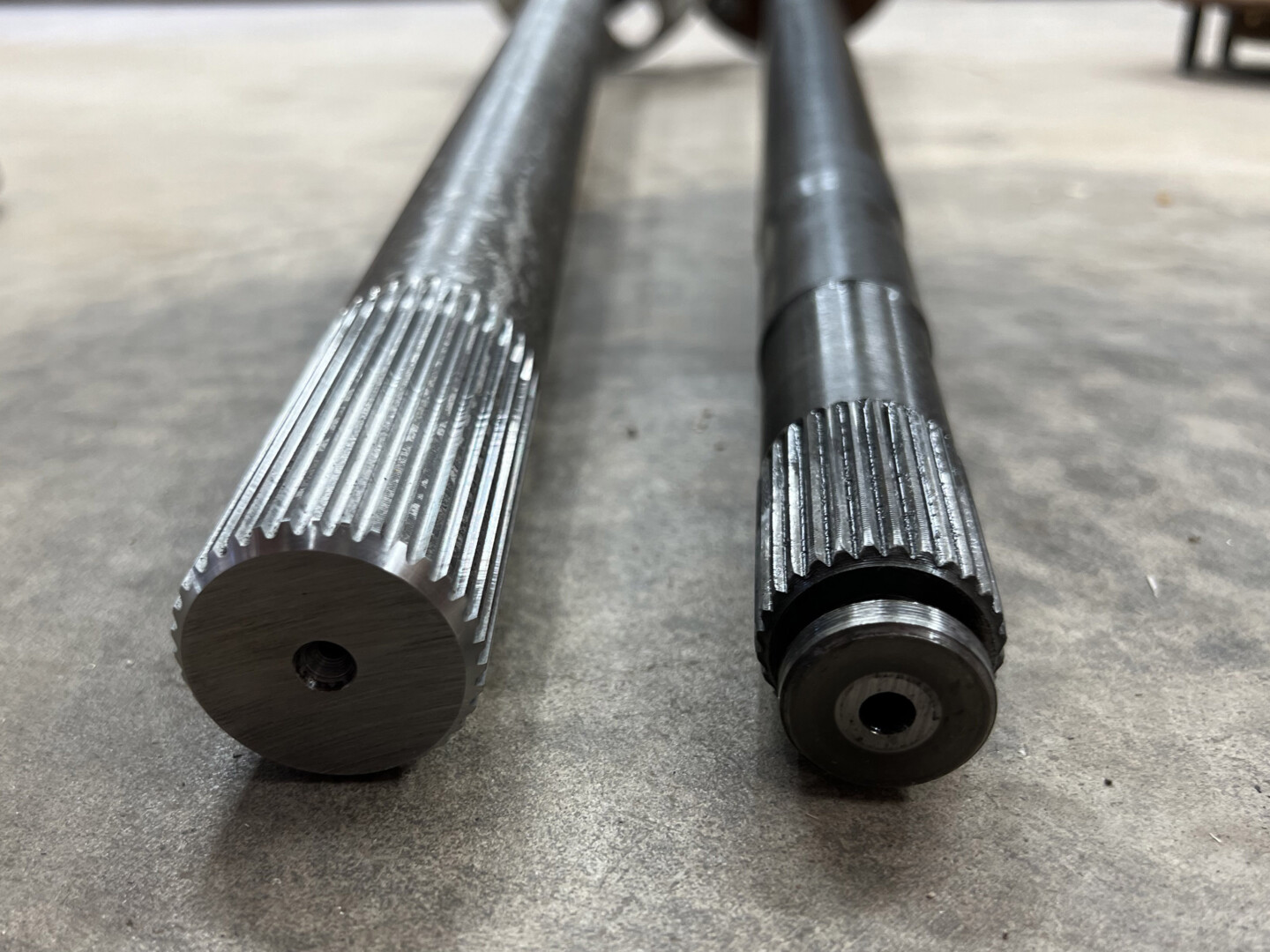
The difference is obvious. On the left is a Moser 1-3/16-inch axle for a 9-inch rear end, and on the right is a stock GM fourth-gen F-body axle. Which one do you think is more likely to break at the track?
I don’t want to beat GM up too badly here, their engineers are smart folks and they built their rearend assemblies to be efficient. The lighter the better, because less weight helps improve fuel mileage and acceleration. They were always hunting for the magic thickness of metal to beat the CAFE standards for fuel mileage and also not fail under stress. Where things get messy is when passenger cars are modified to go to the track, pushing the vehicle’s limits beyond what the engineers based their calculations on. That’s when parts can fail, and this is where Moser comes to the rescue.
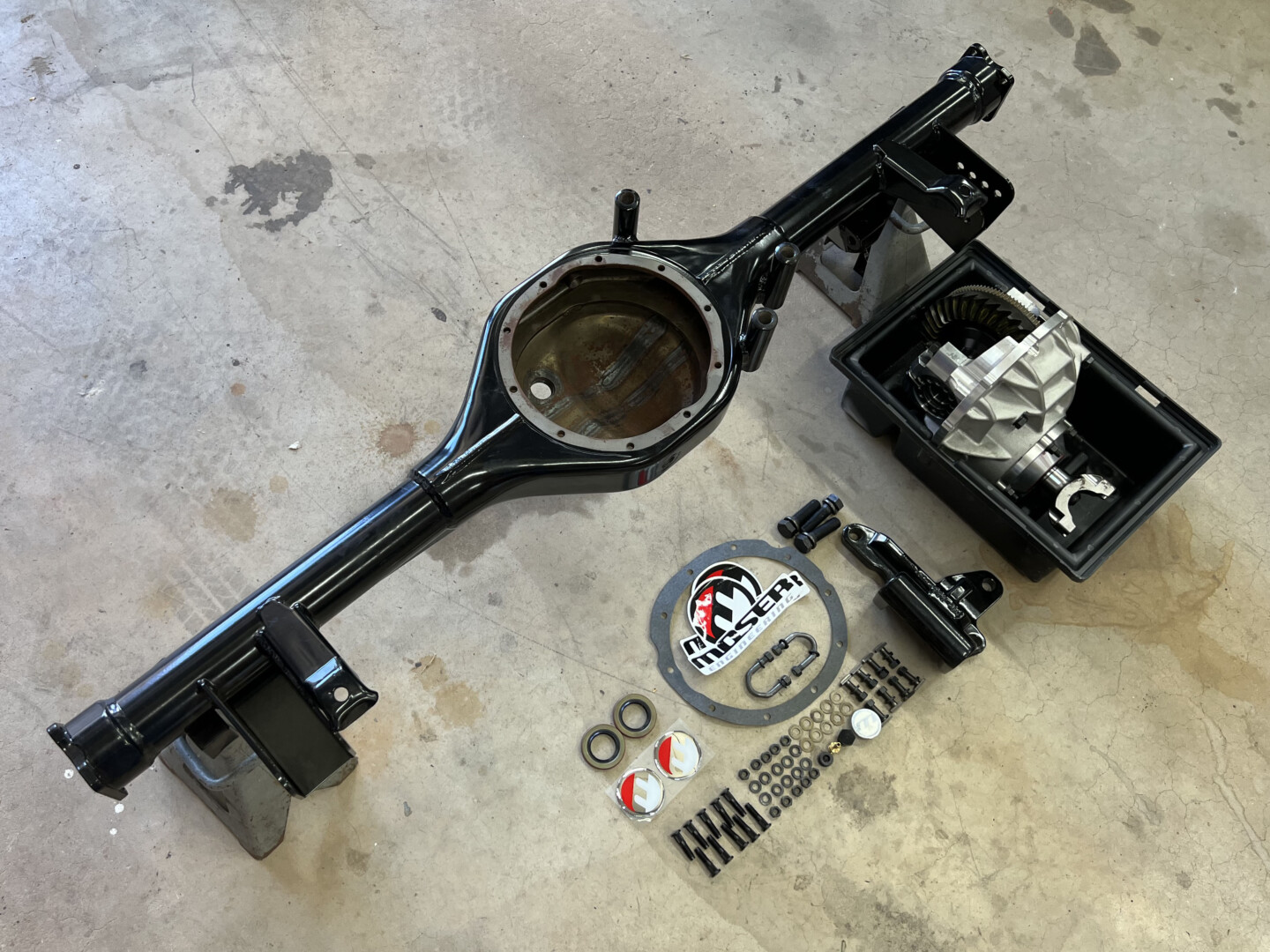
It is Christmas in July for Project Dirty Bird. Our Moser MusclePak assembly includes the axle housing, axles, a 9-inch third member with a WaveTrac differential, and all the fixings to bolt into a fourth-gen F-body.
Building On The Past
What the aftermarket industry and hot rodders have known for years is that if you want a strong solid rear axle assembly for serious drag racing or track duty you find a Ford 9-inch rearend out of a truck in a junkyard, you narrow it, weld a few mounting brackets on it and never have to worry about it again. That design, originally from a 1957 F100 believe it or not, has proven to be nearly indestructible for over half a century. When Moser tells you their MusclePak 9-inch rearend assembly will be the last one you put in your car, they have a lot of history and data to back that statement up. This package is stout.
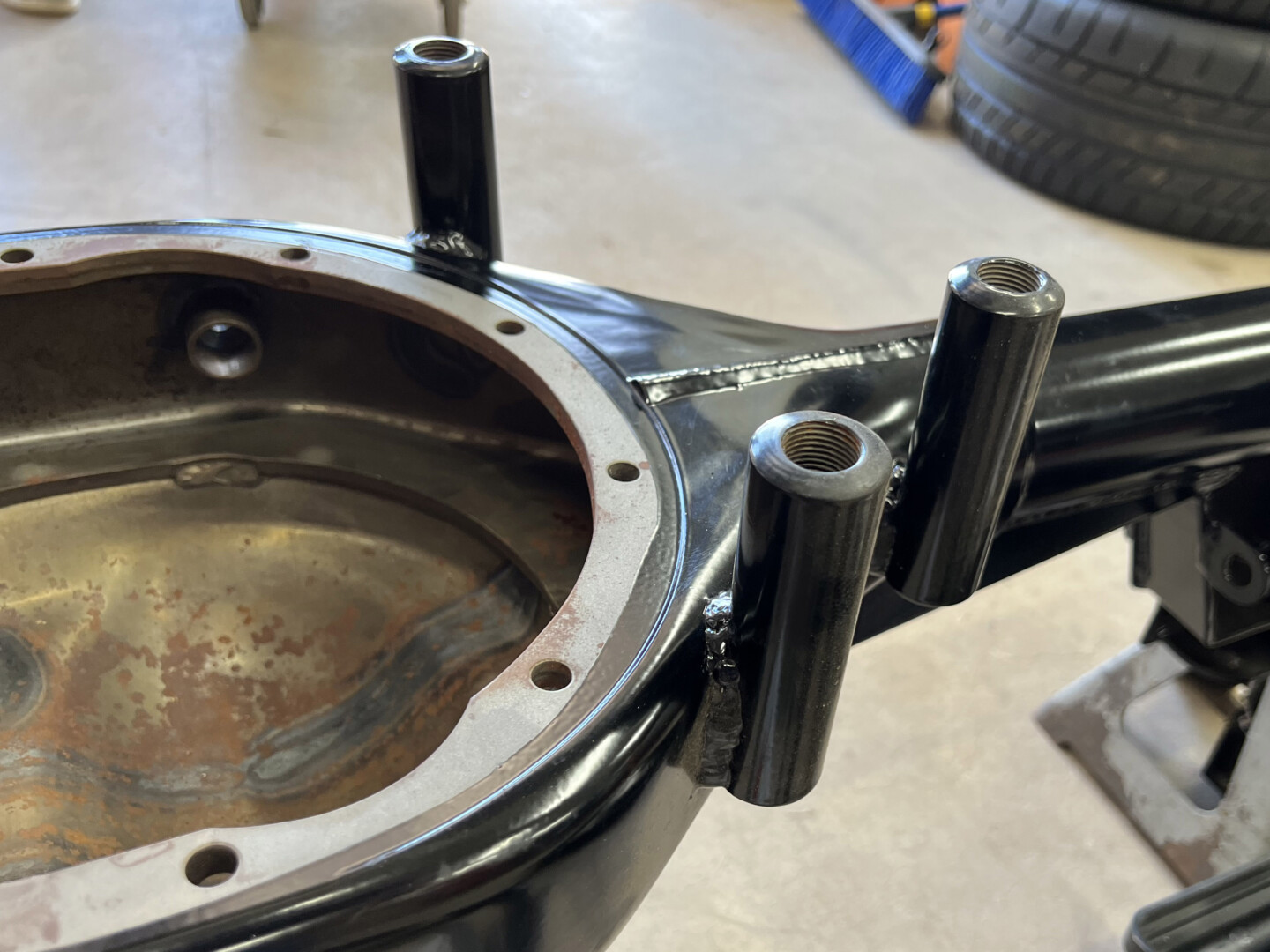
What sets Moser apart from other aftermarket rearend manufacturers is their assemblies are built in the United States with US steel and they are designed with the correct mounting points for specific installations, in this case fitting the Ford part in a GM vehicle.
Not only is the Ford 9-inch design stout, but Moser has improved that design and enhanced it to be even stronger. Shane St. Myers, sales technician at Moser Engineering located in Indiana, explained why their axles are so good. “All of our stuff is fabricated here in the United States using US steel. Our welders are professionals and our jigs are heavy-duty. We have designed a hybrid 9-inch housing that uses full three-inch axle tubes.”
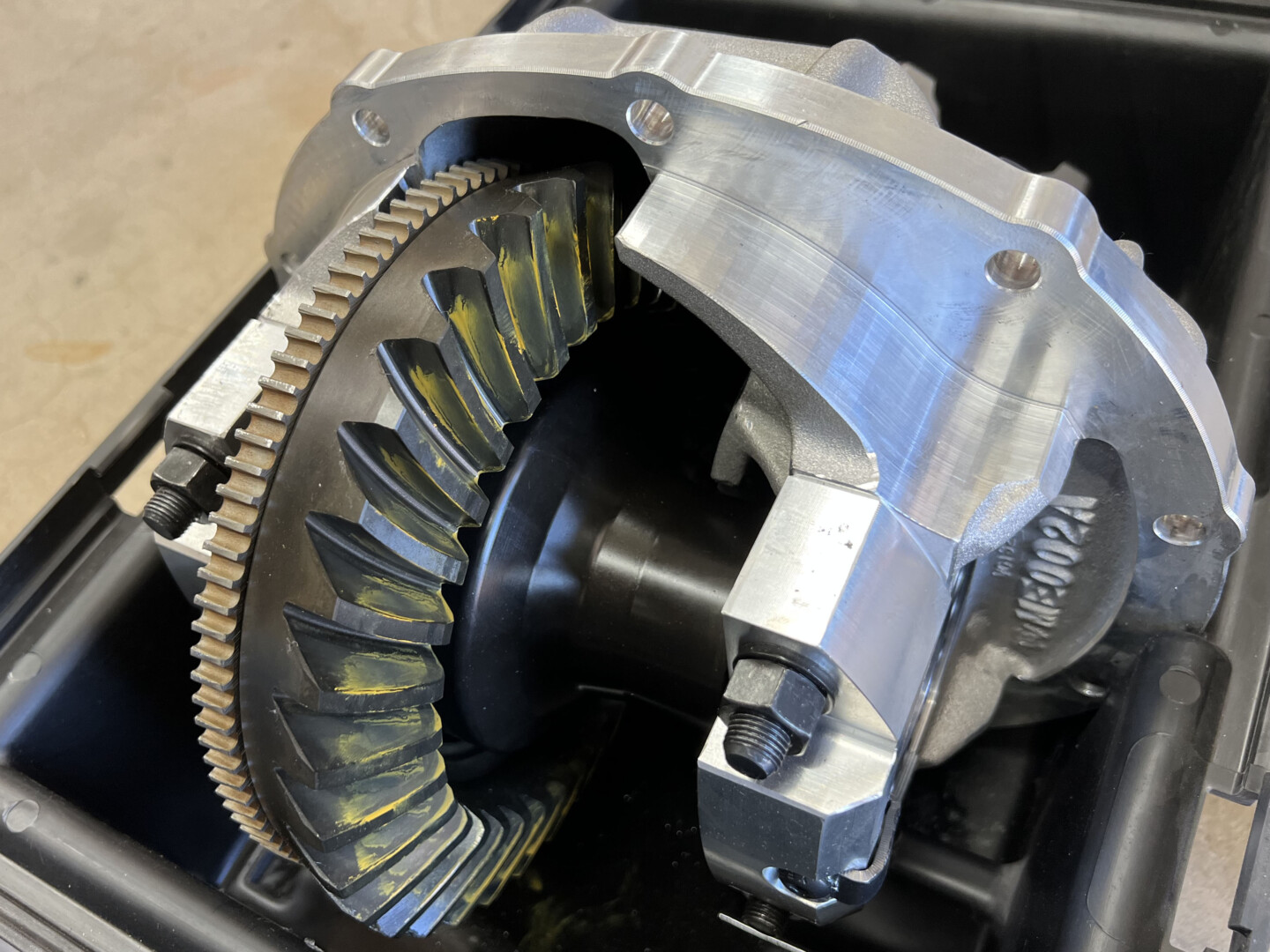
The third member arrived from Moser already assembled with the 3.89:1 ring and pinion set with the proper backlash and the Wavetrac limited slip differential installed. All that was left to do was bolt it into the housing and add fluid.
Made To Order
When ordering a Moser MusclePak assembly they need to know the vehicle it is going in to ensure the spring perches, suspension mounting points, and brake attachment holes are in the proper position. They also want to know how much horsepower you are throwing at the rearend and what you want to do with the car. “I ask people if they plan on drag racing the car, road racing the car, or if it will be a street car with occasional track days or autocross,” said Shane. “If it is going to be a street car with some autocross time I recommend they don’t choose the full floating axle option as it is a more expensive rearend.”
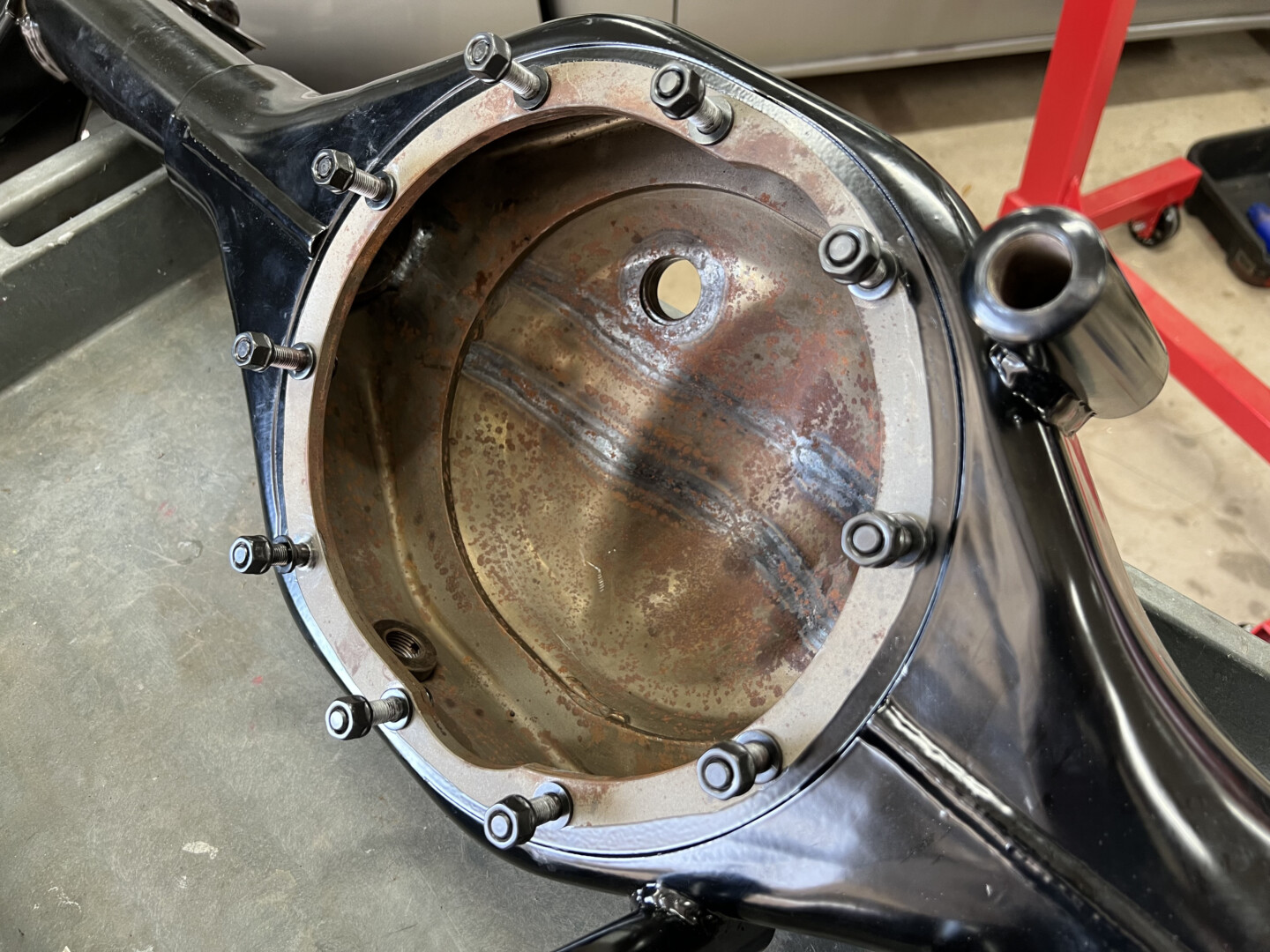
Yes, there are ten bolts that hold the third member in the housing but this ain’t no 10-bolt GM axle housing. In fact, this Ford 9-inch is much stronger than even a GM 12-bolt.
Shane can also help with choosing the optimal gear ratio for customers, “I ask if it is a naturally aspirated (N/A) car versus a turbo car because that will make a difference in the gear ratio. An N/A car may love 4.11 gears whereas a turbo car needs a 3.50 set to compliment the engine, which wants to spool up.” Since we are running a Tremec Magnum F “wide ratio” manual transmission with a 2.97 first gear, Shane recommended Moser’s Pro/Street 3.89:1 gear set with our Muscle Pak rearend package. This gear set is from US Gear and is made using 8620 steel. Since we will be driving Dirty Bird on the street, using it in autocross, and not making four-digit horsepower, this gear set is an excellent choice.
And Shane’s knowledge doesn’t stop there. He will also help customers pick the right differential. Racers know “it’s all about the diff.” The best way to get out of a corner quickly is with a good differential. Because we plan on doing some autocross with our Formula, we chose to go with a Wavetrac differential. This gear differential applies power equally to both wheels normally, but what is unique about the Wavetrac is that it will continue to apply power to the wheel with the most traction when the other wheel is unloaded such as during hard cornering. The Wavetrac differential is made with high-strength 9310 steel gears inside case-hardened billet or forged steel housings and assembled with ARP fasteners throughout. Additionally, this differential requires no maintenance or rebuilds while in service. Shane recommends the Wavetrac because it is made in the USA, comes with a lifetime transferable warranty, and because it works great for putting down power.
One of the things that separate the Ford 9-inch design from a GM design is the fact that the housing (which holds the axles) and the third member (which holds the gears and differential) can be quickly and easily separated. If you have another third member with a different gear ratio ready to go into the car, you can quickly install it and find those precious tenths of a second that separate first from second place at the track. Shane said he has swapped out a third member on a Ford 9-inch in fifteen minutes while lying in the mud at the races. To do the swap you pull the axles, you unhook the driveshaft, and 10 bolts later the third member is out.
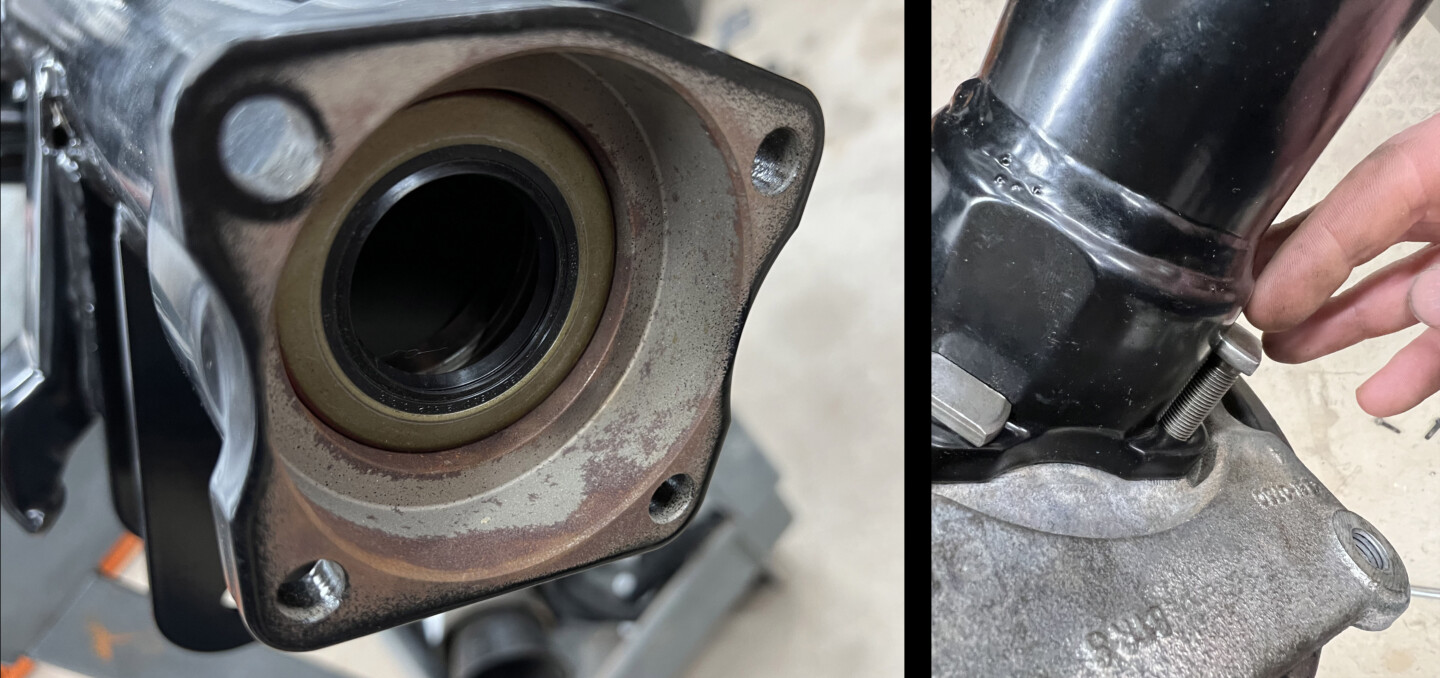
Fresh axle seals were pressed inside the housing. You can see the end of the axle tubes are already set up to accept the fourth-gen F-body brake mounting assemblies.
Unless you are only drag racing a quarter-mile, there is no perfect gear ratio for every track. Being able to change gears easily can really make the difference in performance and that is what the Ford 9-inch design allows for. And these rearends can easily withstand 1,000 horsepower which is why, according to Shane, “This is the last rearend you will buy.”
A Moser MusclePak Just For Dirty Bird
Using Shane’s advice, we ordered a Moser Ford 9-inch rearend with a Wavetrac differential that would bolt directly into a fourth-gen F-Body. Then we waited for the big box to arrive. When it did, we were pleased to see the attention to detail in the fabrication. The welds looked great and the fit and finish were spot on. The spring perches were in the perfect spot for our Formula. The rear brake assemblies bolted right up to the rear end without any modifications. The Moser kit was an easy install from start to finish.
This assembly is built to be tough, which means heavy. Although the rearend easily bolts into our fourth-gen Formula, care must be taken while doing so as to avoid smashing any toes or fingers. Thanks to the heavy-duty jigs Moser uses the spring perches, lower control arm mounts, and panhard bar mount are all exactly in the right locations.
The third member arrived already assembled with 3.89:1 gears installed on the Wavetrac diff and set to the perfect backlash. All we had to do was bolt the third member to the rearend housing using the 10 provided studs and nuts. With the help of a trusty floor jack, we lifted the rearend and connected the suspension components to keep it in place in its new home.
With the rearend installed in the car, all that is left to complete the installation is bolt the driveshaft to the pinion gear, reconnect the brakes, and put on the Moser axle caps.
Shane said this would be the last rearend we buy, and after installing the unit I can understand why. This thing is super tough. We are looking forward to the acceleration the new gears and Wavetrac provide on the autocross course. We have a few more details to knock out on Project Dirty Bird, but it will see the track sooner than later. Thanks to this stout new rearend from Moser, we will be making laps and not rearend gear spaghetti.